Shaft Coupling: Definition, Types, Uses, Working Principle & Advantages [Complete Guide]
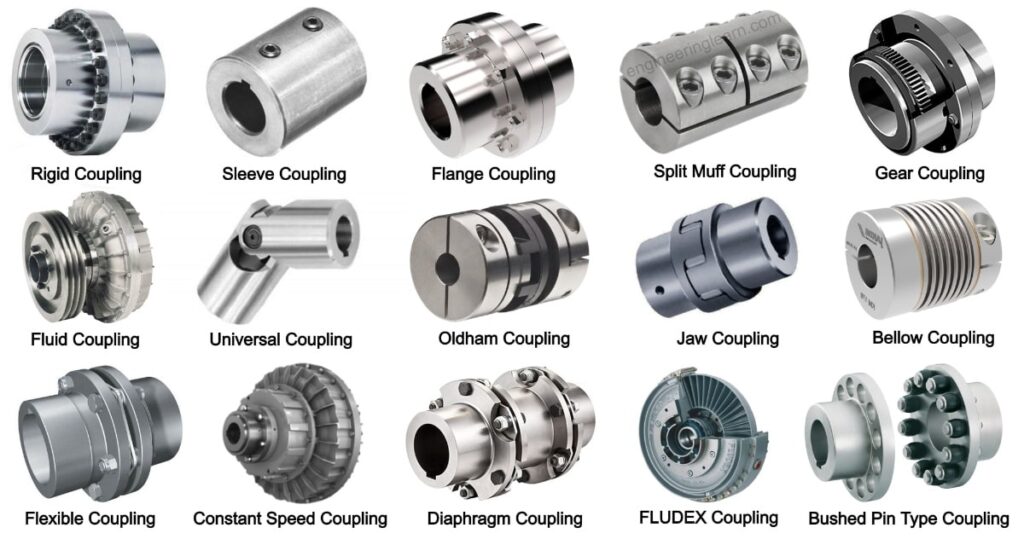
What is Coupling?
Shaft Coupling: Definition, Types, Uses, Working Principle & Advantages [Complete Guide] :- A coupling is referred to as a type of device which is usually found having its application in order to connect the two shafts together for the purpose of power transmission. Couplings are mostly found being either rigid or flexible which depends according to the alignment accuracy as well as the torque requirement. There are various types of shafts which are found being available that can be used depending upon the requirement.
Shaft Coupling
The shaft coupling is referred to as that mechanical component which is most commonly used for the purpose of connecting two rotating shafts like the driving shaft in order to let the driven shaft work for purpose of transmitting power. Shaft coupling is commonly used in mechanical instruments like motors, pumps, generators, as well as compressors.
Working Principle of Shaft Coupling
The working of a coupling device is usually found being less complicated which can be easily understood even by a lay man. The main working of the shaft coupling is to connect two shafts of either the same diameters or of different diameters together.
The motor is responsible for transmitting the power from the drive side and the propeller which is found on the driver side. It is important to know that the coupling does not transfer the heat of the motor to the driven side. Flexible coupling is the one which is segregated into two groups one is known as metallic and other is elastomeric. The metallic types are found being responsible for using the freely fitted parts that are found either rolling or sliding against one another or, on the other hand. Other than this all the non-moving parts are found being bend in order to take up the misalignment.
On the other hand, the elastomeric types are found being responsible for gaining flexibility from all the non-moving, elastic, or plastic elements which are responsible for transmitting the torque within the metallic hubs. There is a scope of connecting both the shafts together by the process of coupling. There is no constraint even if the shaft diameter seems to be different. Important is the motor of the driving side along with the propeller of the driven side. Coupling absorbers are responsible for absorbing the shock as well as the vibration from getting transferred. This helps in protecting the surrounding components from being damaged.
Uses of Shaft Coupling
Shaft coupling is found having various uses which are described below. Scroll down to know more about their uses.
- For connecting the shafts of units that are manufactured separately like a motor and a generator.
- In case of misalignment of any of the shafts.
- Provides mechanical flexibility.
- Absorbs the transmission of shock loads.
- Protects against excessive loads.
15 Various Types of Coupling
There are various types of couplings which are found being used as per the requirement:
- Rigid coupling
- Sleeve or muff coupling
- Split muff coupling
- Clamp or split-muff or compression coupling
- Bushed pin-type coupling
- Flange coupling
- Gear coupling
- Flexible coupling
- Universal coupling
- Diaphragm coupling
- Oldham coupling
- Bellow coupling
- Fluid coupling
- Variable speed coupling
- Constant speed coupling
1. Rigid Coupling: ( Types of Coupling )
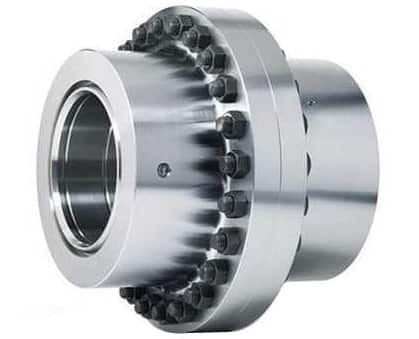
A rigid coupling is referred to as that coupling which is usually used whenever there are two shafts that seem to be perfectly aligned with each other. These couplings are found being suitable in close alignment only. For example muff coupling, Split-muff coupling, and Flange coupling are some of the well-known example of rigid coupling.
2. Sleeve or Muff Coupling: ( Types of Coupling )
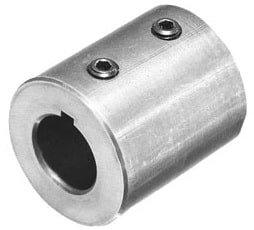
Muff or sleeve coupling is referred to as one of the simplest type of rigid coupling which is commonly known to be made up of cast iron.
Construction of Sleeve or Muff Coupling
Muff coupling is found consisting of a shaft, key, sleeve or muff, along with this it is found having a hollow cylinder with an inner diameter of the same dimension as that of the shaft. These types of couplings are found fixed over the ends of the two shafts which is usually done using a gib head key.
The power transmission in such couplings is done using one shaft to the other shaft using a key and a sleeve. It is very necessary to know that all the elements need to be strong enough in order to let it transmit the torque.
3. Split Muff Coupling: ( Types of Coupling )
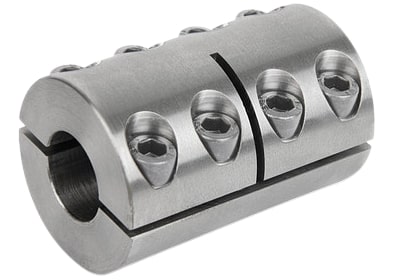
Both the ends of the shaft are found being connected to each other using a key which is thus fitted in the keyway of the shafts. Most commonly one end of the muff is found being fixed from below, whereas the other end is the one which seems to be attached from above. Both of the ends are found being held together using the bolts and nuts.
This coupling is found quite responsible in order to avoid failures and is also widely used in the heavy-duty speeds. There is no need to change the position of any of the shaft in order to assemble or to disassemble the coupling.
4. Clamp or Split-muff or Compression Coupling: ( Types of Coupling )
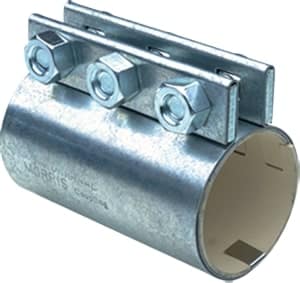
Clamp or Split-muff or compression coupling is also commonly known as split muff coupling. In such types of coupling, the muff or the sleeve is found being made of two halves which is then bolted together. Both the halves are the ones which are found being made of cast iron which are thus connected together using the studs or bolts.
5. Bushed Pin-Type Coupling: ( Types of Coupling )
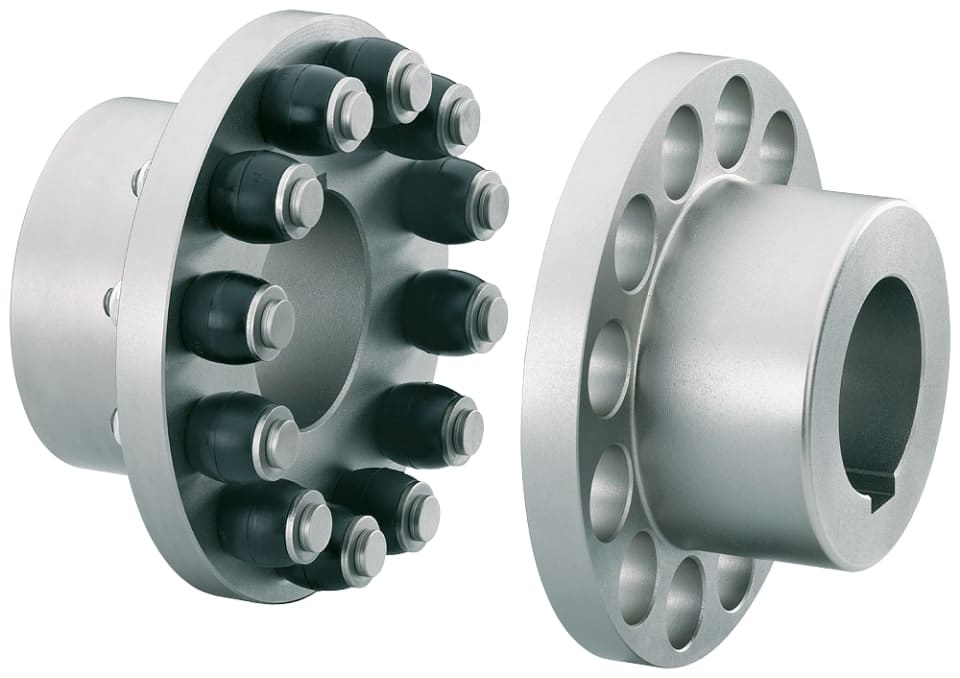
Bushed Pin-type coupling is referred to as the one which is most commonly used for the slight parallel misalignment, angular misalignment, or any type of axial misalignment of any of the two shafts. This type of coupling is found to be a modified version of rigid flange coupling. These are found consisting two halves which are usually dissimilar in the construction bolts which is known as pins, rubber bushes that are used over pins.
There seems to be a clearance of around 5 mm within the faces of both halves of the coupling. There seems to be no rigid connection within them whether the drive done through compressed rubber or leather bushes.
6. Flange Coupling: ( Types of Coupling )
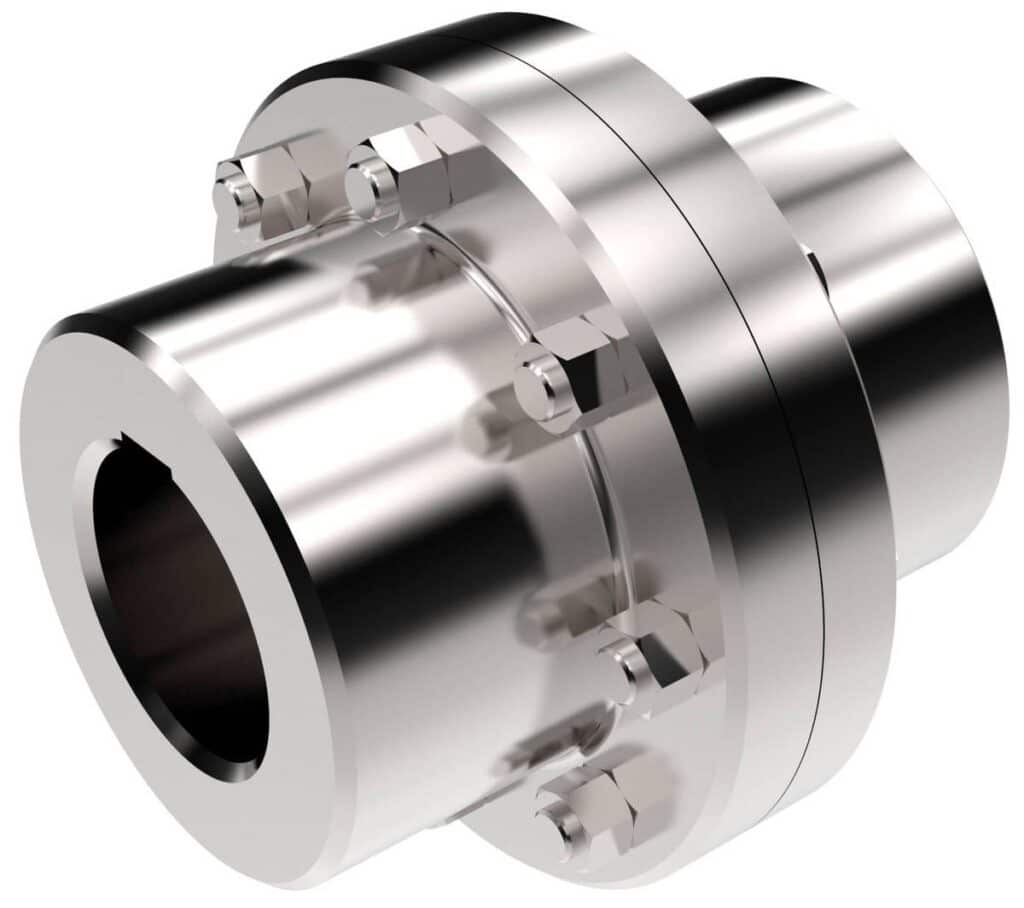
Flange coupling is referred to as that coupling which consists of usually two cast iron flanges that is found being fixed at the end of each shaft mandatorily. The two flanges are together bolted along with the other bolts in order to complete the drive. A flange coupling is the one which brings two tubes together in a combined sealed manner.
One of the flanges is found having a projected portion part whereas the other flange has a similar recess. Each of the flange is found having the ends which are bought together in order to make the correct alignment without causing any resistance in the material that is found being passed through them.
It helps to bring the shaft into the same line in order to maintain the correct alignment. The two flanges are found being coupled together by using the nuts as well as bolts. These couplings are the ones which are typically found being used in order to pressurize the piping systems. Also, these couplings are employed in the heavy loads hence, it is very beneficial on the large shafting.
3 Different Types of Flange Coupling
- Unprotected flange coupling.
- Protected flange coupling.
- Marine flange coupling.
7. Gear Coupling: ( Types of Coupling )
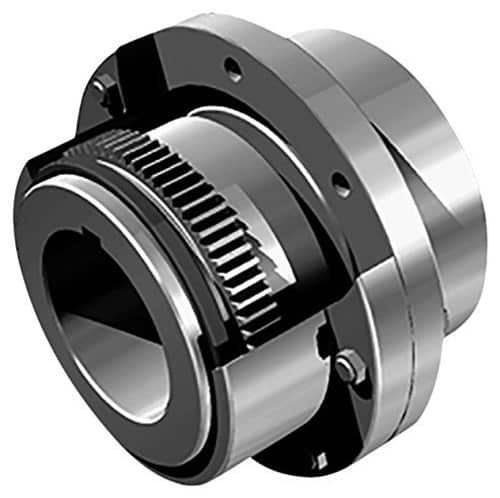
The gear coupling is referred to as a modified version of the flange coupling which can transmit high torque due to the larger size of the teeth. In these types of shaft coupling, the flanges as well as the hub are found being assembled separately together instead of any single part as a flange coupling.
During its construction, each joint is found having a 1:1 gear internal ratio along with an external gear pair. And gear coupling is found being limited to an angular misalignments of around 0.01-0.02 inch in parallel as well as in 2 degrees angular.
Gear couplings as well as universal joints are the ones which are found using for similar applications. These are those couplings which are mostly used in the heavy-duty applications where the torque transmission is found being required to be the highest.
8. Flexible Coupling: ( Types of Coupling )
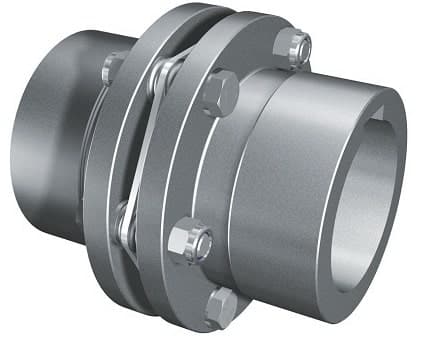
Flexible couplings are the ones which are found being used in order to connect two shafts which have both lateral as well as angular misalignment. For example bushed pin-type coupling, Universal coupling, Oldham coupling, Gear coupling, Bellow coupling, Jaw couplings, Diaphragm couplings etc.
9. Universal Coupling: ( Types of Coupling )
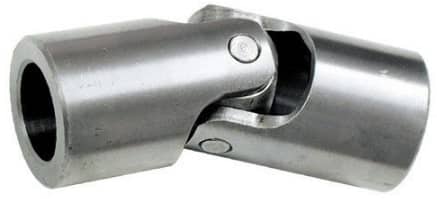
The universal coupling is also known as Hooke’s coupling which is used whenever there are0 two shafts axis that are found intersecting at any intersecting small angle. The inclination of both the shafts is found to be quite constant, whereas practically, this gets changed once the motion gets transferred from one shaft to another.
A universal joint is widely used in the transmission of the power. Universal coupling is referred to as that coupling which is found transmitting the gearbox to the differential of the any type of automobile. In such type of cases, mostly both the universal joints are found being used on each end. One of them is used at the end of the propeller shaft to the gearbox and other one on the differential of the other end.
Universal coupling is found being used for the purpose of transmitting the power in order to different the spindles of the multiple drilling machines as well as any other milling machines.
10. Diaphragm Coupling: ( Types of Coupling )
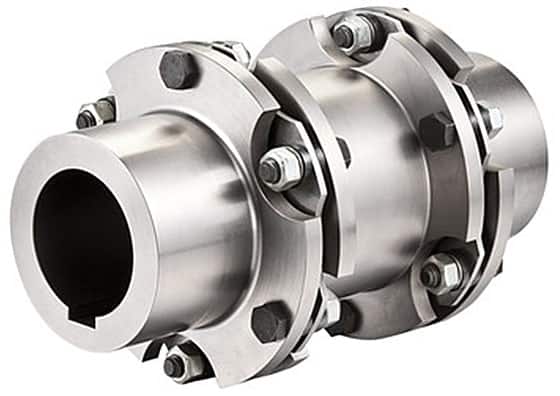
Diaphragm couplings is referred to as one of the most non-lubricated coupling which is used in higher-performance turbo-machinery, transmitting torque as well as the serving misalignment within the equipment shafts.
This type of coupling is found transmitting the torque from outside to inside diameter, and then from inside diameter to outside diameter.
Diaphragm couplings are the ones which uses a single or a series of plates for the types of flexible members. Diaphragm coupling is the one which is found allowing angular, axial or parallel misalignment. This couplings are found being used where the higher torque as well as higher speed seems to be required.
11. Oldham Coupling: ( Types of Coupling )
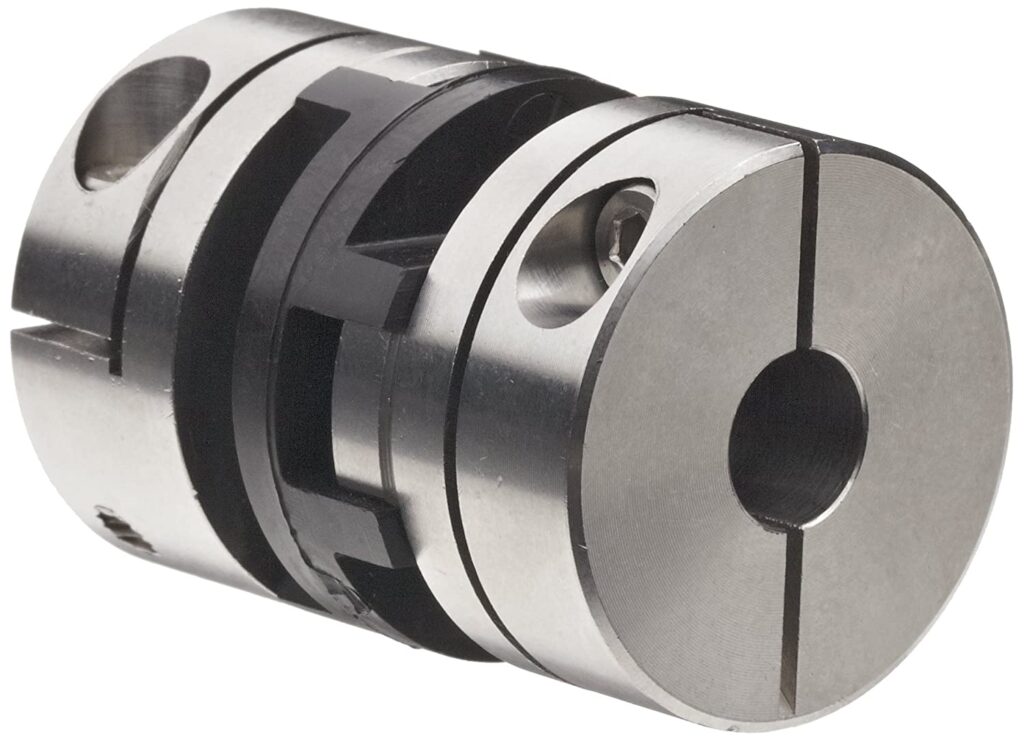
Oldham coupling is referred to those couplings which are used wherever there two shafts are found being used and are found having a lateral misalignment. The middle part is found to be fixed by the use of pins which are found being fitted to the flanges as well as the floating parts. There are two different components of speed which are found having the result in the lateral misalignment of the shaft that is found being adjusted as they rotate.
12. Bellow Coupling: ( Types of Coupling )
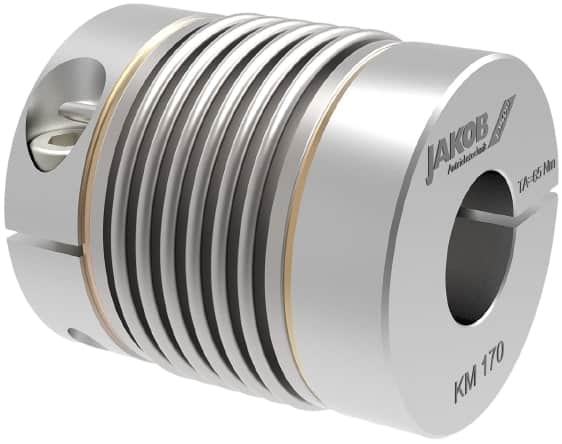
Bellows couplings are referred to as the ones which are found being one of the most flexible coupling along with the twin coupling ends which are known as hubs. These couplings are found having an excellent torsional rigidity in order to accurately transmit the velocity, angular position, and the torque. These are the couplings which are usually made up of stainless steel and are thus used wherever the high precision positioning is found being required.
Advantages of Jaw Coupling
- Able to handle angular misalignment as well as reactionary loads due to misalignment.
- High torque.
- High chemical resistance as well as dampening capability.
13. Fluid Coupling: ( Types of Coupling )
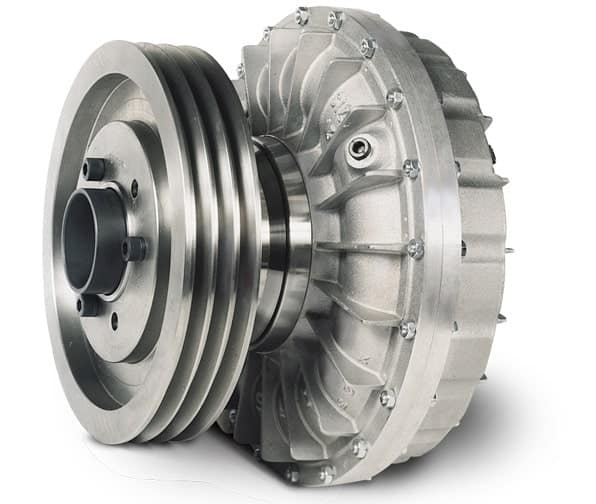
A fluid coupling is referred to as a hydraulic coupling which seems to be a hydrodynamic device that is used in order to transmit the rotating mechanical power through the acceleration as well as the deceleration of the hydraulic fluid. It is found consisting of an impeller which is found on the driving shaft as an input along with a runner on the driving shaft as an output. The impeller is found acting as a pump wherein the runner acts as a turbine.
In the impeller which is found near its axis, the tangential component is one amongst the absolute velocity which seems to lower. On its near periphery the tangential component is found to be of the absolute velocity which seems to be quite higher and therefore while the impeller accelerates the fluid velocity founds to be increasing.
An much as there is the increase in velocity, the kinetic energy also increases. The fluid also emerges at a higher velocity from the impeller, which strikes the runner blades, transfers its energy, and leaves the runner at low velocity.
Advantages of Coupling
There are various advantages of couplings about which almost everyone should know.
- Designs are usually very less complicated.
- High absorptions due to mounting errors within the axes of the driving side.
- Power transmission.
- Absorbs vibration.
- No heat transfer from the motor on the drive side.
Image Source :- jakobantriebstechnik, kpower, couplingfluid, lenze-selection