14 Types of Punches (Tool): Applications, Precautions, Working Principle, Advantages & Disadvantages
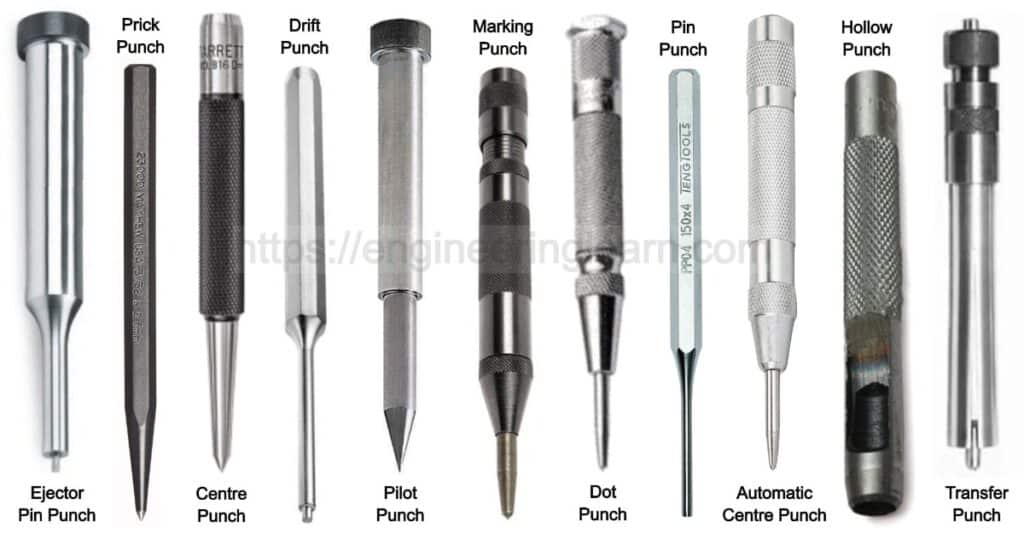
What is Punch Tool?
Types of Punches: Applications, Precautions, Working Principle, Advantages & Disadvantages :- Punches are known to be made up of hard metal rod using a pointy tip at one end and a dulled end at the other which are often used in conjunction with other tools like hammer or chisel in order to cut and shape the blocks of materials. There are various types of punches which have its application in drilling, drawing circles, punching holes, removing damaged rivets, bolts, or pins and many more. Punches are referred to as the typical devices which is used to make a hole with their points.
Classification of Punches
There are numerous types of indenting rods available which are discussed above and are used to Centre punch or drift punch, pin punch or prick punch, used to prep a drill hole to any other metal sheet surface. These types of tool has a place in every toolbox and workshop bench. So, now let’s have a look on the classification and uses of different types of punches.
A) According To The Shape
Punches are mostly classified according to the shape of their points. The most popularly used punch amongst these is the prick punch which is quite helpful for placing the reference marks on metal sheets. These types of punches are used to transfer the dimensions from a paper pattern directly on to the metal. In order to take the reference correctly you need to place the paper pattern directly on the metal that too in the orientation in which you need to obtain the results.
B) According To The Slider Movement
Punches are classified on the basis of the movement of slider. These are further divided into 3 types. Single action, double action and three action punch, whereas the most commonly used punch is a single action punch.
Types of Punches Tools
If you ought to visit a workshop then you will definitely find various types of punches for their specific functionalities and uses. This article will help you in learning a lot about types of punches, so let’s gets started to learn all about punches.
1. Prick Punch: ( Types of Punches )
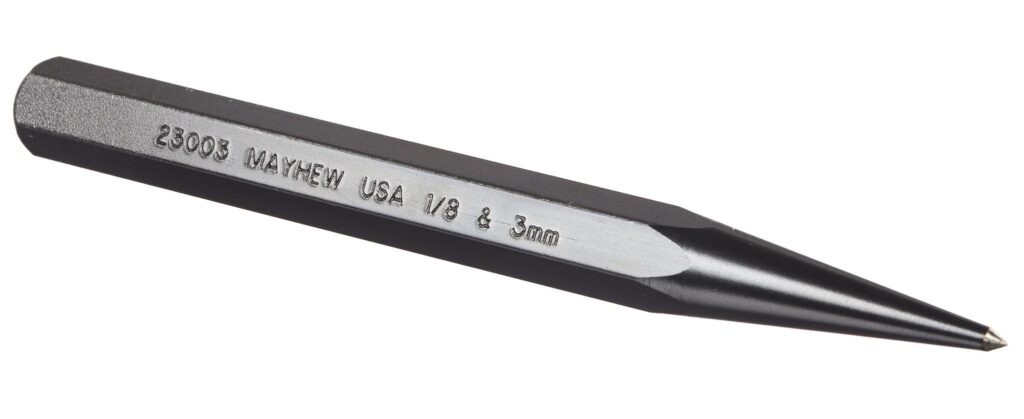
Prick punch is known as the most used and common type of punch in today’s professional world. Most of the people are found using this punch while transferring the dimensions from a paper pattern on to the metal and then to use them as a point of reference for cutting or fabricating purposes. Prick punches are found to be similar to centre punches which can have a narrow point and are also used for marking a design or layout.
Shifting the dimensions is mostly done during placing the paper pattern directly on the metal and in order to select its orientation properly and accurately. By hitting the punch lightly with a hammer, the pattern gets outlined on the metal which creates a slight indentations on the metal.
2. Centre Punch: ( Types of Punches )
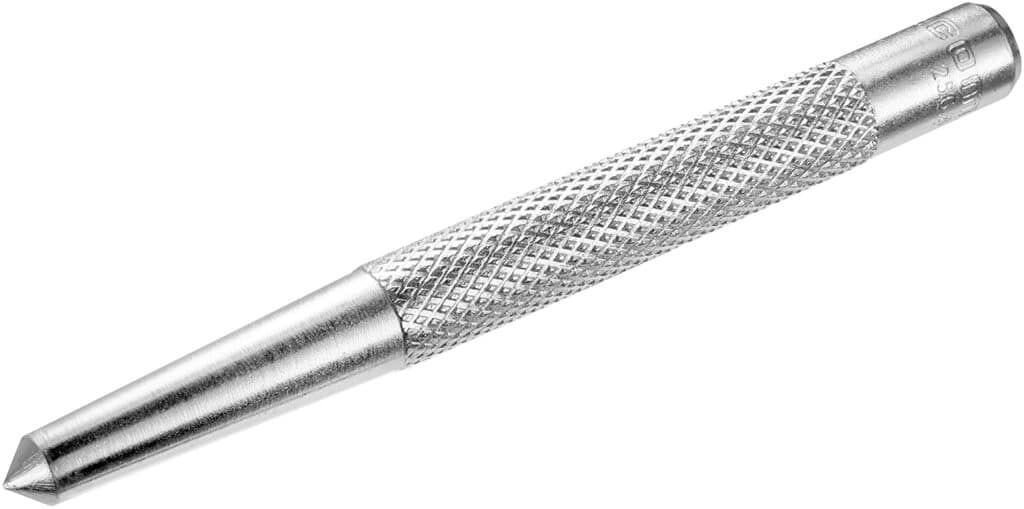
Prick punch are quite adequate when it comes to take the reference marks for metals, but there are some metal works which require a larger indentation. So, with a Centre punch, it can make indentation along with the reference marks in metal that seem to be quite large for drilling activities. The Centre punches are found to be heavier as compared to the prick punch and also have a point ground at an angle of 60 degrees.
While striking a Centre punch as excessive force, an unnecessary protrusion and dimples around the created markings can be found. Centre punches are also used in order to mark the indentation for a guiding drill bits and to also identify a location on a surface. Centre punches are observed to be highly pointed, in order to obtain large circular indentations. These are also used as a prepping tool. The drill bit is found locking it against the punch mark after which the hole is made without any constraint. These types of punches are equipped with a knurled rod, which is an easy grip- tool and stops your drill from wandering.
3. Drift Punch: ( Types of Punches )
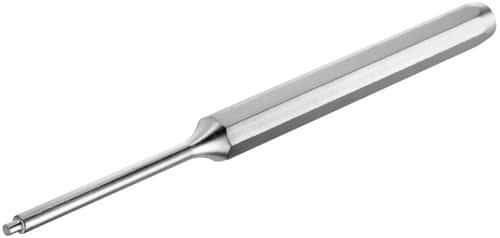
Drift punches are also referred to as drift pins and are mostly used to align bolt or rivet holes so that the fasteners can be inserted properly. In case there is a need to remove the damaged rivets, bolts, and pins which bound up in holes, then one must use a drive punch.
Drift Punch should be labelled as anti-drift tool as this member of the punch family is specifically designed to align the fastener holes. Using these once can gently hammer this punch into the holes unless and until it gets properly aligned and prepped for the fasteners, be it a rivet or a bolt. Once tapered, the body can also be used to widen the aligned holes.
Rather than the pointy ends, a drive punch usually comprises of a flat face. The width of this punch’s face is used to determine the type of punch whereas the sides of this punch are responsible for tapering down the face to some situations which would require you to use a punch with a straight shank. A punch with a straight shank is highly common and is known as a drift punch.
4. Pin Punch: ( Types of Punches )
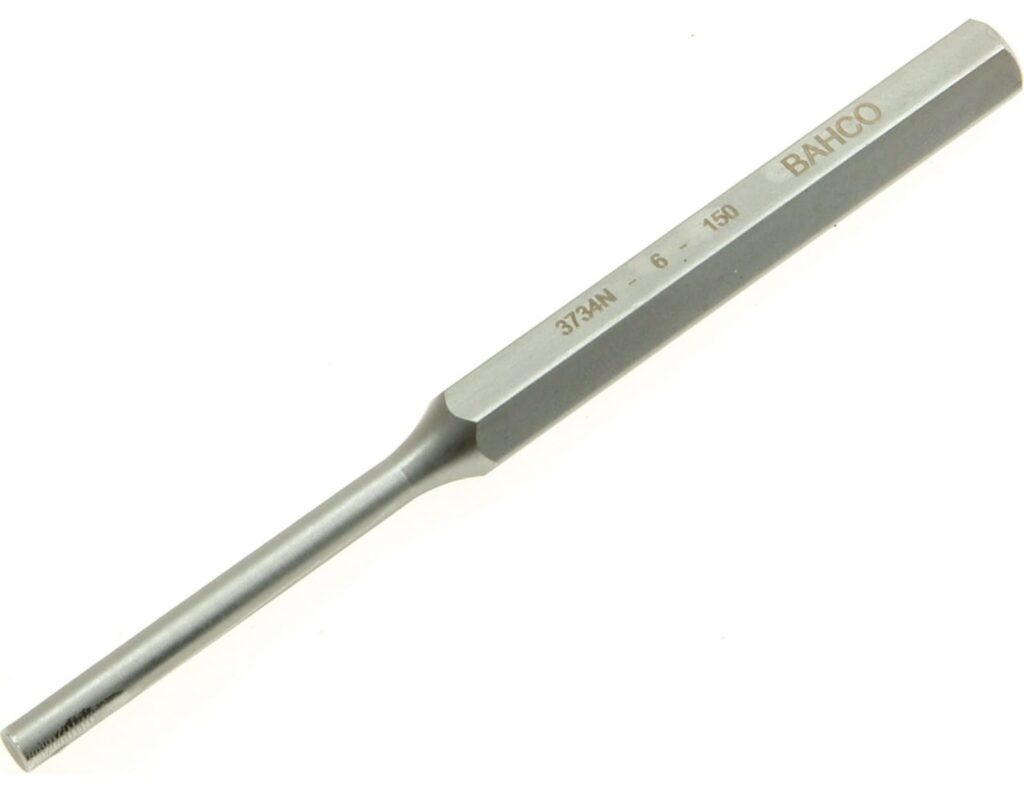
A pin punch is found having a straight shank which has various applications in removing bolt or pin. The foremost purpose of pin punch is to finish the removal of bolts or pins from a hole which is already loosened up by a drive punch.
A Pin punch can entirely drive rivets and pins from a hole until they are taken out, which cannot be done by the drive punches. The removal of bolts or pins from holes can only be performed by the drive and pin punches. Pin punches are quite used in order to drive a pin into a mating bore.
A pin punch can be used when a small metal shaft is trapped in a hole. If any rusty chain gets trapped with its linkages, the pin punch knocks that little shaft free. There is also a heavier version of this tool which is a variant called a drive punch and is used to force out damaged fasteners and rivets, and to also disassembly short projects
5. Transfer Punch: ( Types of Punches )
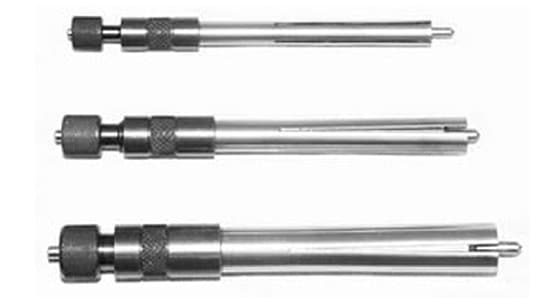
Transfer punches can be known to have a set shank diameter which is specifically designed in order to transfer the geometry of several tapped holes by fitting the bore with close tolerances and by also marking the Centre of the hole on any other surface.
For making drill-locating holes in a template can be easily done by the help of a transfer punch. The dimension of a transfer punch is normally kept around 4-inches which is sufficient to transfer the location of holes via pattern or a template on the metal. The transfer punch has a point which initially tapers and then subsequently runs straight for a lesser distance. This pointy tip of a transfer punch is somehow quite similar to the prick punch.
As soon as you have determined the right punch which is suitable for your site than you must find out that working with those punches feels so amazing. Punches are commonly known to be the indentation tools. Once you strike the blunt head of this narrow shaft with the help of a hammer, the opposing end of the tool is found creating an indented mark in a metal work piece.
6. Ejector Pin Punch: ( Types of Punches )
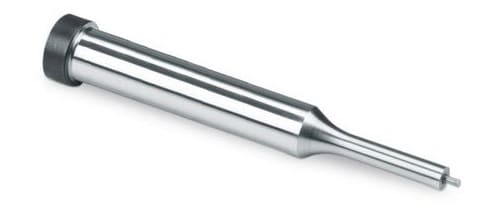
Ejector punches are those mechanical devices which are designed to knock-the out material or to eject the parts after pressing or stamping operation. A punch is certainly built from an equally rigid metal which is shaped like a pen.
7. Marking Punch: ( Types of Punches )
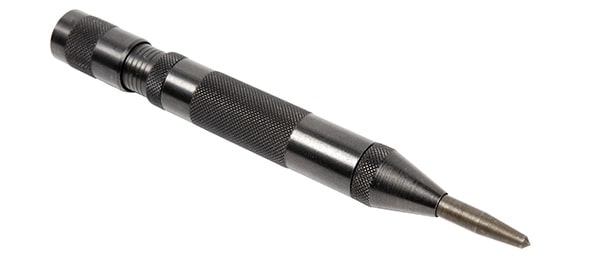
Marking punches are referred to as those punches which are used to emboss or create a specific texture on the surface of a material or work piece.
8. Pilot Punch: ( Types of Punches )
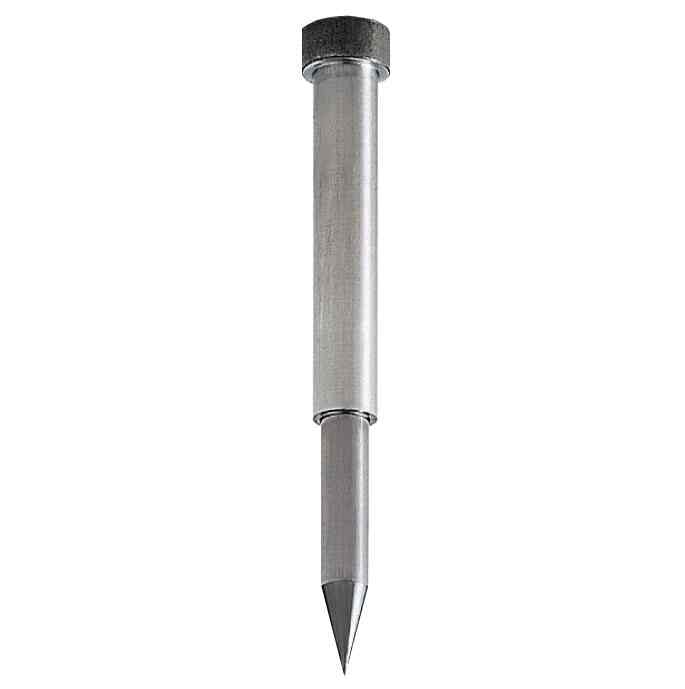
Pilot punches are found having an inner pin which is used for aligning the punch into an existing hole or also for allowing the outer point to cut out a larger hole. These punches are quite similar to solid or regular punches which have a solid flat point with no voids or internal bores.
9. Straight Punch: ( Types of Punches )
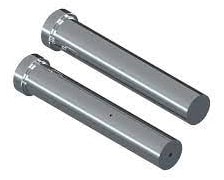
Straight punches are referred to as those mechanical devices which are used to cut through the metal sheets or other sheet materials like leather or plastic. These types of punches are quite simple and easier to use and can be found at various leather and plastic industries.
10. Letter Punch: ( Types of Punches )

This type of mechanical device is usually formed from a short rod of steel which is of the varying shape, depending upon the requirement of work.
A letter punch is also referred to as letter stamp in common language and is most commonly used in our day to day life as well as in various industries. The working of a letter punch is mainly done by embossing the letters or numbers into the work piece. The most common thing about this type of punch is that they are mostly the reversed images, which tend to give results in an immediately readable format.
11. Hollow Punch: ( Types of Punches )
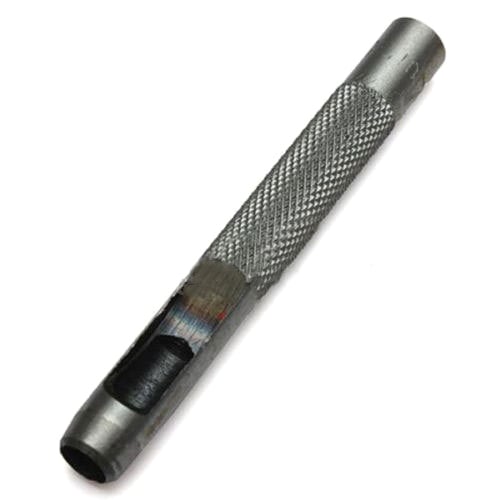
Hollow punch is referred to as a mechanical device which is made from the hardened carbon steel. These instruments are designed to puncture a surface like metal sheet or leather for creating a hole. The working end can differ in shape or size in order to protect the work surface from being damaged.
These types of punches are found working in screw mounting plates, drain valves, locks and keys and many more.
12. Dot Punch: ( Types of Punches )
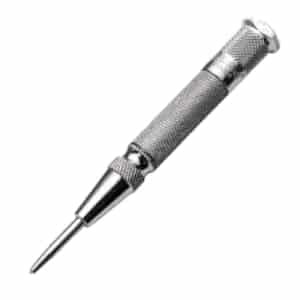
Dot punch can be termed as a lighter version of a centre punch which is used for the similar type of work, but is used wherever the required intensity for the indentation is less. This type of punches are given priority as they are found to be more accurate as compared to the centre punch.
A ball peen hammer is used to hit the head of the punch which delivers enough force directly to the point of the punch in order to put a small indentation into the surface of any material. It must be made clear that both the dot and Centre punch are found having similar type of applications.
13. Automatic Centre Punch: ( Types of Punches )
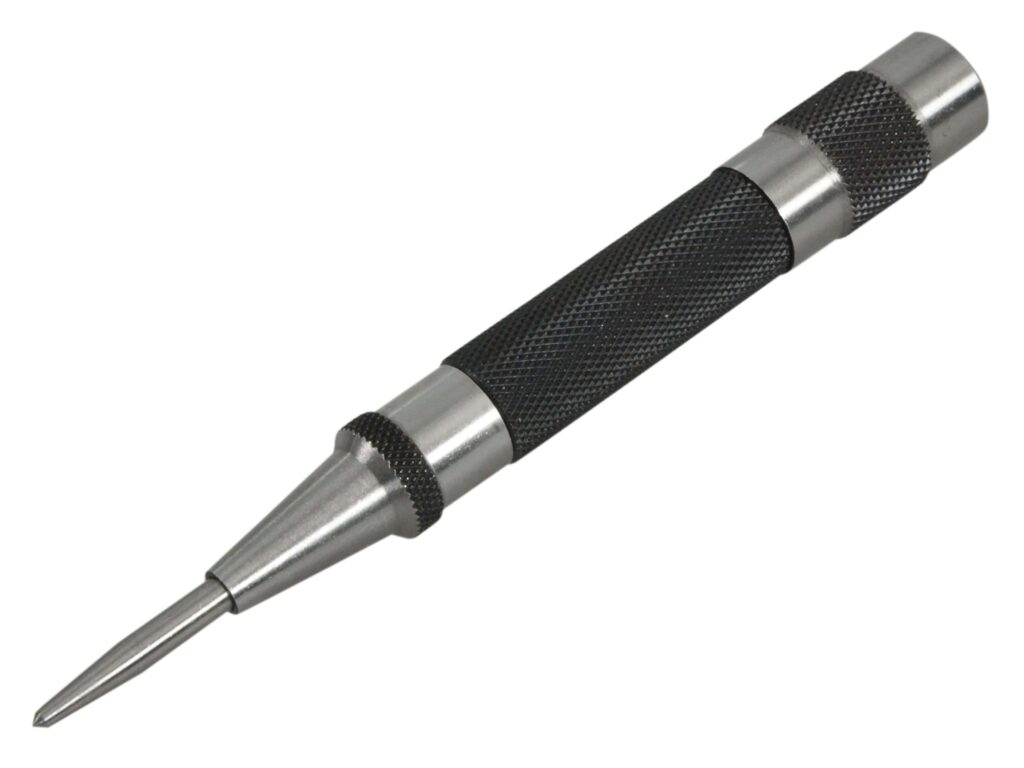
An automatic center punch is referred to as a hand tool which is used in the production of a hole in a work piece. The type of material can be any, but mostly it is the metal sheet. This instrument is found performing the same function as that of an ordinary Centre punch that too without the need of a hammer.
It works in the following way:
Once it is pressed against the work piece the energy gets stored in the spring and gets released eventually, when it has an impulse that drives the punch in order to produce the hole. The impulse which is provided to the point of the punch is continuous which allows uniform impressions to be made.
14. Bell Punch: ( Types of Punches )
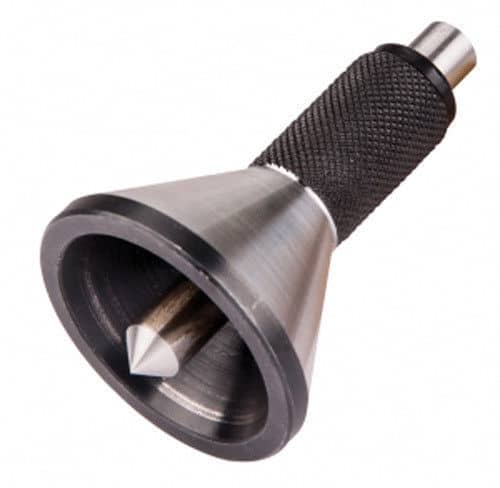
A bell punch is a mechanical device which is used for punching purposes and is known to have accurate self-Centre on a round bar material. These instruments are found in varying sizes wherein the maximum diameter of a bell punch is found to be 35mm. A bell punch is completely machined in steel in order to create punch without being failed. Using this instrument is quite simple and easy by placing the sheet which needs to be punched, after which the hardened punch gets centralized.
Working Principle of Punching
- Punching works on the principal of converting the rotary motion into linear.
- The main motor is responsible for providing the power to drive the flywheel.
- With the help of a clutch and a connecting rod, the flywheel is responsible for driving the crankshaft or the eccentric gear.
- It converts the circular motion into the linear motion where there is a need for a transfer point within the slider and the connecting rods.
- There are two different types of designs which converts the circular motion into linear motion one, i.e. is the spherical type and a pin or cylindrical type.
- While operating, the drive mechanism powers the rams upwards and downwards which opens and closes the upper & lower die. A strip of metal sheet passes between the die shoes.
- Once the punch moves down and applies pressure on the metal sheet and cuts a hole, the detached portion gets away from the opening of the die.
Application of Punching
Here are some of the applications of punching about which everyone needs to know. So let’s dive in to learn more:
- Punching is mostly used in various industries but specifically used in the metal-working industry.
- Punching is used in order to manufacture different types of products in industries for making the hole in the work piece used in automobiles, aerospace, manufacturing industry, defence equipment, etc.
- Punching is also used in the food and restaurant industry in order to cut chapati, puri, papad from the atta sheet.
- Punching is also used in our day to day life to punch the papers.
Advantages of Punching
Stable and Highly Accurate
Punching instruments and its parts like crankshaft, gear, ram are made in high temperature in order to harden them and provide stability and high wear and tear resistance. This results in making them highly stable and also helps them in working accurately.
Reliable and Safe Operation
Punching machines come with two types of brakes one is the normal and the other is an emergency brake which is designed to stop the machine in any emergency situation. Once the technology is advanced, these machines will come with higher advanced sensors in order to provide safe operations and reliability to the user.
High Productivity, Reduce Labor Work, and Automatic Production
Punching machines are referred to as highly productive machine which reduces the manual labor and results in reducing the cost as well as increasing the efficiency on the other hand. As the technology gets advanced the machinery is expected to be fully automated which might not require any manual labor
Disadvantages of Punching
- Punching machines which are used in factories are quite huge and require high initial investment.
- As these machines work at a very high level, it is found to produce tremendous noise.
- The parts of such punching machines are found to be complex which becomes tedious to repair and might also require an expert even for a minor fault.
- Huge punching machines cannot be operated to fulfil the small-scale production process.
Precautions While Working on a Punching Machine
Here are some of the precautions which must be taken while working on a punching machine, especially in the industries to avoid huge losses:
- Ensure proper lubrication level in all the parts.
- Ensure the proper installation of mold.
- Check the air pressure in the compressor.
- Check the switch button
- Let the machine run empty for a while in order to check the working of the parts like brake clutch etc.
- Immediately treat the abnormal heat, abnormal vibration or abnormal sound (if observed).
- Make sure that the direction of rotation of flywheel is same as that of a rotary mark.