5 Types of Heat Exchanger: Definition, Parts and Application [Complete Guide]
![Types of Heat Exchanger: Definition, Parts and Application [Complete Guide]](https://engineeringlearn.com/wp-content/uploads/2021/11/Heat-Exchanger-1024x539.jpg)
Introduction of Heat Exchanger
Types of Heat Exchanger: Definition, Parts and Application :-Heat exchangers are mainly used for transferring of heat from one fluid to another fluid with indirect contact between them. Heat exchangers design is essential for their high efficiency. Heat exchanger is a very essential industrial device therefore it is very important that we should know the parts of the heat exchanger. Heat exchanger has various parts which are assembled together for a efficient heat exchanger. There are various parts of heat exchanger having different advantage as well as disadvantage. Instead all of this we are going to discuss different parts of heat exchanger and their functions.
Types of Heat Exchangers
On the basis of design characteristics, heat exchangers are categorized in numerous categories. Most common types of heat exchanger are given below:
1. Tube and Shell Heat Exchanger: ( Types of Heat Exchanger )
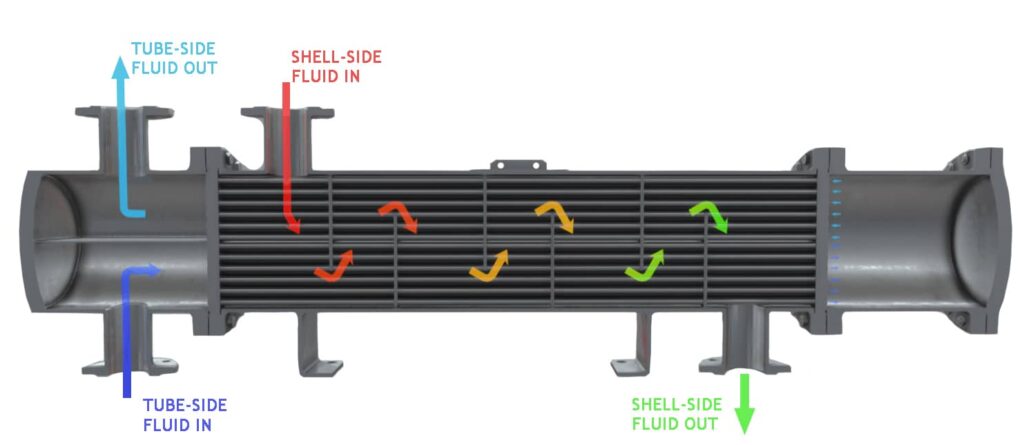
Shell and tube heat exchangers are the very common type of heat exchangers among all others. They are usually constructed from series or a parallel tube which is also known as tube bundle or a single tube which are enclosed under cylindrical pressure vessel which are sealed. Shell and tube exchangers are designed in such a way that one fluid flows within small tube provided in the heat exchanger while the other fluids flows at the outside in between them under sealed shell.
There are various of other parameters for the designing of shell and tube heat exchanger such as single or two phase heat transfer, finned tubes, crossflow arrangements or concurrent flow, counter current flow and multiple, single or two pass configurations. In some shell and tube heat exchangers have double pipe heat exchangers and helical coil heat exchangers.
Applications of Tube and Shell Heat Exchangers
- Power generation
- Oil cooling
- Marine applications
- Refrigeration
- Pharmaceuticals
- Metals and mining
- Pulp and paper industries
2. Plate Heat Exchanger: ( Types of Heat Exchanger )
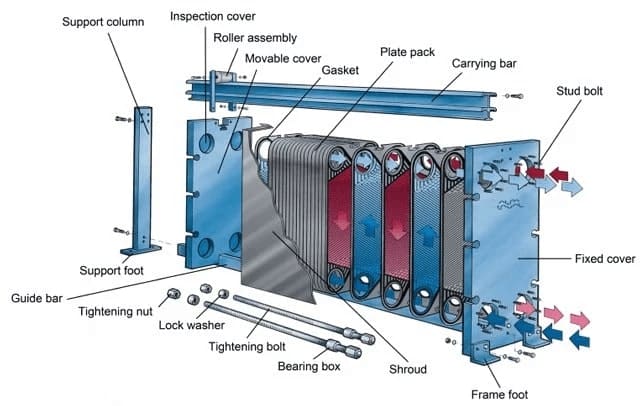
Plate heat exchangers are also known as plate type heat exchangers. Plate heat exchangers are made up of several corrugated, thin plates which are bundled with each other. Pair of plates make channel by which flow of fluid takes place and the pairs of plates are being attached and stacked with the help of brazing, bolting or welding in such a way that another passage is created within the pairs by which another fluid flow.
The standard design of the plate is also found with variations like pillow plate heat exchangers or plate fin exchangers. In plate fin exchangers, multiple flow configurations are provided by using a spacer or fin in between the plates. In this case more than two fluids are able to pass by the device while the pillow plate heat exchangers exert pressure on plate which results in increasing the efficiency of heat transfer across the surface of plate. In this category there are some other types of exchangers available which are plate and shell, plate and frame and spiral plate heat exchangers.
Applications of Plate Heat Exchangers
- Geothermal applications
- Heat pump system
- Pressure interceptor
- Diesel engine cooling
- Heat recovery
3. Double Pipe Heat Exchanger: ( Types of Heat Exchanger )
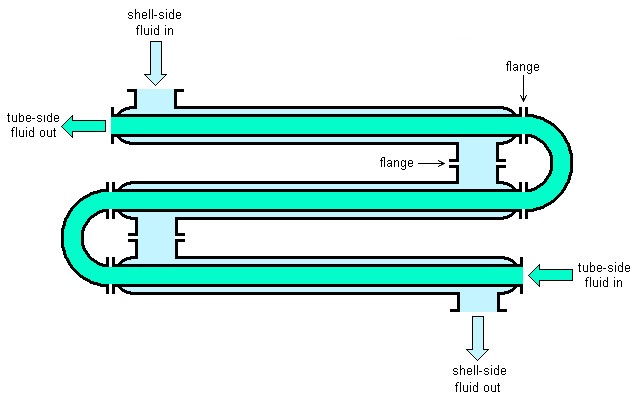
Double pipe heat exchangers are in the form of shell and tube type of heat exchanger. The design and configuration of the double pipe heat exchangers are very simple in which there are two or more cylindrical pipes or tubes (one small tube while the second one is the larger tube) which are concentric. In two concentric cylindrical tubes or pipe, fluid flow within one pipe while the other fluid flows in the larger tube around the smaller tube.
The double pipe heat exchangers have the design characteristics of indirect contact types and recuperative as stated earlier that fluids flow are separate and they flow within own channels along the process of heat transfer. In the design of double pipe heat exchangers, some flexibility is provided to them such as their design may have counter current flow or concurrent flow arrangements and they can be used in parallel, series, or series – parallel configurations in a system.
Applications of double Pipe Heat Exchangers
- Petroleum refining
- Refrigeration
- Sewage treatment
- Heating and cooling in engineering systems
- Compressors and boilers because they have very high pressure and temperature.
4. Boilers, Condensers and Evaporators: ( Types of Heat Exchanger )
Evaporators, condensers and boilers are heat exchangers which use the mechanism of two phase heat transfer. In case of a two phase heat exchanger the phase of one or more than one fluids are changed at the process of heat transfer which can be either changing from gas to liquid or a liquid to gas.
Applications of Boilers, Condensers and Evaporators
- Operation of steam engines and turbines
- Reciprocating pumps operations
- Thermal power stations
- Industrial process work
- Automotive
- Refrigeration
- Steam power turbine
- Pharmaceuticals
- Foods and beverages
- Resins and polymers
- Paper and pulp industry
Condensers are defined as those heat exchanging devices which are used to take vapor or gas (which is heated) and cool them to their condensation point which results in changing of vapor or gas into liquid form.
In case of boilers and evaporators, the process of heat transfer changes the fluids from liquid state to gaseous state.
5. Other Heat Exchanger Variants: ( Types of Heat Exchanger )
Heat exchangers are used for various of different applications in various of industries. Therefore, some heat exchangers variants are used which is suitable for particular type of specification and requirement of application such as fan cooled heat exchangers, air cooled heat exchangers and adiabatic wheel heat exchangers.
Parts of Heat Exchanger
Different heat exchanger parts are:
1. Heat Exchanger Tubes
Heat exchanger tubes are one of the very essential part of heat exchanger which is used for transferring the liquids. These tubes are generally seamless or welded but welded are highly economical in comparison with the seamless. The diameter of heat exchanger tubes are generally 1 inch, 0.75 inch and 0.625 inch but some heat exchanger tubes have smaller diameters but the cleaning of small diameter tubes are very problematic.
Large diameter heat exchanger tubes are used for achieving low pressure drop. Supplements like twisted tapes are provided with some tubes for enhancing the process of heat transferring at the time when we are dealing with laminar flow condition of the fluids. Generally all the heat exchanger tubes are bundled and are kept in a casing or a shell.
Heat exchanger tubes are generally made up of zirconium, nickel alloys, titanium and stainless steel and these materials are suitable for all types of heat exchanger applications of re-heaters, heaters, evaporators, coolers and condensers.
2. Heat exchanger Font and Rear Headers
From front header the fluid enters in the heat exchanger and the rear header is exit before the entrance of fluid from front header for passing it through tubes for various times. Front header is also known as stationary header.
a) Types of Front Header
Front header are of various types such as A type, B type, C type, D type, N type, Y type. They are generally fixed type and on the basis of flow pressures, repair and ease of cleaning their application varies. Generally B type of front header is cheaper than A type front header and type B are used for high pressure but A type front header can repair easily. C type and D type front header are used for pressures which is more than 100 bar. N type front header are accessed without creating any disturbance to the system and Y type front header are cheapest and can be directly installed to the pipeline.
b) Types of Rear Header
There are two main rear headers floating and fixed. For standard types of services fixed types are preferred which have N type, L type and M type and they are used when high mechanical stress are not developed. Fixed rear head with bellow are used when thermal expansion is expected to occur. Fixed rear head is used when pressure does not exceed 35 bar, the shell do not require cleaning and the fluid is not dangerous.
For overcoming the problem of thermal expansion as well as facilitate cleaning of bundle by its removal a U tube rear header are used.
When thermal expansion is must to provide then a S type header are used and it is a floating type. It is essential to reach out both the side of exchanger for cleaning it. Type T header are also a floating header which is simple for extracting the bundle as well as cheap in comparison with type S. Type T provide thermal expansion unrestrictedly.
3. Air Cooling System of Heat Exchanger
Air cooling system of a heat exchanger has chillers, condensers and fin fans. Fin fans are design in such a way that they can blow over hot tubes for keeping them cool very efficiently. Condenser is used for cooling the object till the changing of phase from gaseous to liquid. Chillers use water as a coolant for cooling and lowering the temperature of water which results in cooling the device.
4. Transfer Line Exchangers
Transfer line exchangers are used to cool down hot gases quickly. Transfer line exchanger’s design is based on the pattern of heat exchanger tubing but for efficient work they require special design. With the help of welded or flange junction transfer line exchangers join radiating coil outlets. They need internal insulation especially for those regions which is exposed to the hot gases and these gases are not cooled with water.
5. Heat Exchanger Baffles
On the side of shell baffles are mounted for supplying high heat transfer rate by increasing the flow turbulence. Baffles help in supporting the tube as well as they decrease the vibration problem.
Baffles Arrangements
Baffles are generally installed with several of arrangements like most common single segmental, double segmental. Baffle pitch are the centre to centre distance between the baffles. Baffles are also used for vary cross flow velocity. Generally baffle pitch are less than shell’s inside diameter or can be lesser than 20 percent of diameter. Baffle window or baffle cut size is considered with baffle pitch. Baffle window size are fully dependent on the type of baffle but generally taken as 45 percent for single segmental type and 25 percent for double segmental type.
Types of Baffles
There are various type of baffle based on uses, cost and size.
- Single segmental baffles
- Double segmental baffles
- Longitudinal flow baffles: These are used when there are two pass shells. Generally there are two baffle which serves as longitudinal baffle: Rod baffle and orifice baffle. In these baffles turbulence are generated by the flow of fluid through the baffle.
- Impingement baffle: These valves are used to maintain the bundle at the time of high entry velocity.
- Detuning baffles or de-resonating baffle which is used for decreasing the vibration of tube.
- Blanking baffles or support baffles
6. Heat Exchanger Shell
In heat exchanger shell one fluid flows inside the shell and the other fluid flows inside the tubes. Heat exchanger shells are large pressure vessel and pipe bundles are placed inside the heat exchanger shell. Heat exchanger shells are the most expensive part of heat exchanger.
Generally low pressure fluid flow in the heat exchanger shell while the high pressure fluid flow in the tubes. The relief valves or rupture discs are used by the heat exchanger shell to maintain for high pressures. The shell diameter is dependent on the tube bundle’s diameter. Generally standard pipes are used for heat exchanger shell of diameter less than 24 inches and for shell diameter more than 24 inches rolled plate are used. Generally the diameter of shell is in between 6 inches to 120 inches.
7. Heat Exchanger Tie Rods
Heat exchanger tie rods are very essential part of heat exchanger. Tie rods are secured by the tube sheet at one end and by last baffle at the other end.
8. Heat Exchanger Tube Sheet
Heat exchanger tube sheets are used for supporting and isolating the tubes. Heat exchanger tube sheets are connected with tube sheet with applying roller expansion or by hydraulic pressure. The tube sheet is generally covered with the clad which resist the corrosion and act as a insulator.
9. Nozzles
Nozzles are provided for both tube side and the fluids shell side, two for outlet and two for the inlet.
10. Spacer
Spacers are used for keeping the baffles at their position and for avoiding the vibration and they are fixed on the tie rod.
11. Pass Partition Plate
These plate are placed at the head which guide the path to fluid in more than one pass heat exchangers.
12. Expansion Joint
Whenever high temperature variation is provided to the heat exchanger then expansion joints are very essential. Expansion joint can prevent the contraction and expansion of heat exchanger which can prevent shell cracking.
Image Source :- thermofin