Surface Grinding Machine: Types, Parts & Working Procedure
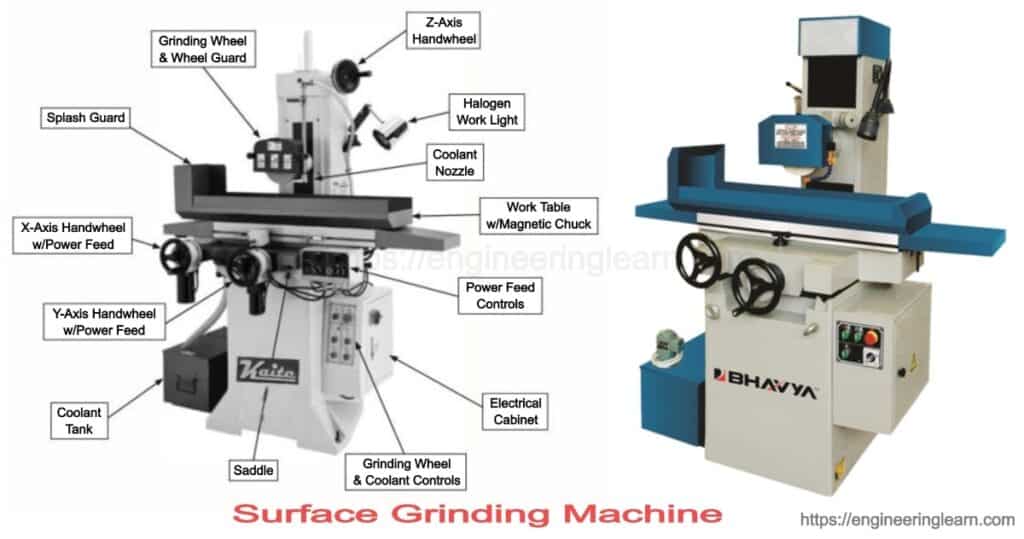
What is Surface Grinder?
Surface Grinding Machine: Types, Parts & Working Process :- A surface grinder consists of an abrasive wheel, a chuck (a workplace holding device) and a rotary table. The surface grinder is generally used for finishing the work-piece or the object. The main use of the surface grinder is in the finishing process. The surface grinder cut the iron in fragments not larger than the following dimensions- 18″ long by 6″ tall by 8″ wide. The table of the grinder is additionally irresistible, to the effect that helps the possession of the magnetic substance. The surface grinder opens up new possibilities because it could allow you to harden the things you make and machine them to a much closer tolerance.
A surface grinder is an outstanding cut-off the instrument for reducing toughened shafting. The material used in surface grinding is 0.25 to 0.50 mm. Surface grinding is best if used for flat cutting. Flat surface cutting is most commonly used surface cutting. The surface grinder is one of the best grinders to be used for this purpose. Grinding is the process of finishing the work piece or the object or we can say it makes the work piece in perfect shape.
Types of Surface Grinding Machine
1. Horizontal-Spindle Surface Grinder
The boundary of the wheel is in contact with the work piece producing the flat surface. The horizontal spindle surface grinder is one of the best type grinders to be used for flat cutting surfaces.
2. Vertical-Spindle Surface Grinder
It is a grinder to be used to allocating the finishing touch to the workplace. It has also been used for flat cutting surfaces.
3. Disc Grinders and Double-Disc Grinder
Disc grinders are similar to surface grinding. Disc grinders are made available for both the upright position as well as the horizontal spindle categories. Double disc grinder work on both the sides of the work piece or the object. Disc grinders can achieve especially fine tolerance.
4. Grinding Wheel for Surface Grinder
Aluminum oxide, silicon carbide, diamond, and cubic boron nitride are four commonly used abrasive materials for the surface of the grinding wheel. The material, aluminum oxide is one of the best to be used. As is the case with any grinding operation, the terms and conditions of the wheel are incredibly important.
Parts of Surface Grinding Machine
- Base
- Hand Traversing Wheel
- Cross Slide Hand wheel
- Work Table
- Column
- Wheel Head
- Vertical Feed Hand Wheel
- Wheel Guard
- Abrasive Wheel
- Coolant
1. Base
The base holds the complete assembly and soaks up all the vibrations.
2. Hand Traversing Wheel
The hand traversing wheel is employed to regulate the worktable in a longitudinal direction. It helps to move the worktable in forward and backward direction.
3. Cross Slide Hand wheel
The cross slide hand wheel is employed to regulate the worktable in up and down direction. This operation helps the work piece is to be placed precisely with respect to the grinding wheel.
4. Work Table
Work table is the space where the work piece is to be gripped correctly.
5. Column
An upright column which has wheel head, wheel guard and abrasive wheel installed over it.
6. Wheel Head
Wheel head is basically a section which has to be set in up and down motion so that the grinding wheel can contact the work piece.
7. Vertical Feed Hand Wheel
The vertical feed hand wheel is employed to supply the feed to the wheel head in a upright route which also points to the depth of cut from the outside of the work piece.
8. Wheel Guard
The wheel guard functions as envelope on the grinding wheel to minimize the accidents.
9. Abrasive Wheel
The function of an abrasive wheel is to get rid of the matter from the surface of the work piece. It is covered with abrasives in order to achieve high precision.
10. Coolant
The function of the coolant is to reduce the temperature of the work region so that heat cannot be dissolute into the work piece and grinding wheel. The most common coolant used is water.
Working Procedure of Surface Grinding Machine
The process of surface grinder follows the most common of the grinding operations. It turns out to be a closing procedure that utilizes a spinning sharp wheel so that you can smooth the surface of the metallic or non-metallic material to provide them with a more sophisticated glance by eliminating the oxide coating as well as contaminants on top of the work piece. This action will also achieve the desired surface area for operational objectives. The surface grinder is made up of the abrasive wheel, a job-carrying apparatus is referred to as a chuck, as well as a reciprocating rotational table. The chuck stands the raw materials in the place at the same time it is currently being used to work on.
It can accomplish this in just one of two different ways: ferromagnetic chunks are being held in position by the magnetic chuck, at the same time as the non-ferromagnetic as well as the non-metallic fragments are being held in position by the emptiness or mechanical process. A machine vies placed on the magnetic chuck can be used to hold a non-ferromagnetic work piece if only a magnetic chuck is available. Factors to be taken into account in surface grinding remain the substance of the grinding disk and the substance of the work is currently being used to work on.
Typical workplace material includes cast iron and mild steel, aluminum, stainless steel, brass, and some other plastics. Once milling at elevated temperatures, the raw material has a tendency to turn weak while at the same time is even more susceptible to decay. The grinding disc is not confined to a cylindrical form and is able to come up with a multitude of possibilities. That will be useful for moving various geometries in accordance with the objects.
Read More :-