Plate Rolling Machine – Definition, Types, Parts, Working Principle & Advantages [Complete Details]
![Plate Rolling Machine - Definition, Types, Parts, Working Principle & Advantages [Complete Details]](https://engineeringlearn.com/wp-content/uploads/2021/12/Plate-Rolling-Machine-1024x539.jpg)
Definition of Plate Rolling Machine
Plate Rolling Machine – Definition, Types, Parts, Working Principle & Advantages :- The plate rolling machine is a type of metal forming machine which utilizes work rollers to produce sheet metal round processing and forming. The plate rolling machine is also known by plate bending roller. This machine is a type of machine tool which is employed for creating continuous point metal sheet bending. The plate rolling machine holds special importance in the sheet metal industry. This piece of machinery can be used to produce cylindrical parts, conical parts, and other parts having different arc shapes.
Significance of Plate Rolling Machine
The process of plate rollers is carried out by means of machines known as plate rollers, which basically consist of three parallel steel rollers, arranged similar to the vertices of an isosceles triangle. The sheet metal when passes between the lower and upper rollers change its shape and undergo a curvature, known as the radius of curvature. This so-called radius depends on the mutual position of the three steel rollers. The rollers need to be moved away if we want to have a wide radius. On the other hand, if a smaller radius is required then they must be approached.
Working Principle of Plate Rolling Machine
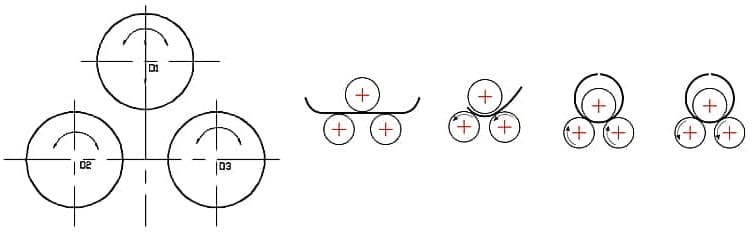
- The upper roller of the symmetrical plate rolling machine performs vertical movement at the centre of two lower rollers by the use of hydraulic oil in the cylinders acting upon the piston. Through the assistance of the final reduction gear of the main reducer drives the two lower roller gearing and creates a rotary motion that aims to provide the torque necessary for the rolling of plates in the machine.
- The now flattened plastic sheet of metal is consecutively passed between the three work rollers, which are two lower rollers and one upper roller of the rolling machine. A continuous bending operation is produced by the means of the upper rollers press and the lower roller’s rotary motion.
- While the inner layer performs compression deformation, the middle remains the same and the outer layer stretches for deformation. This entire process results in permanent plastic deformation of the sheet metal workpiece. The metal sheet workpiece, at last, is rolled into the cylinder, cone etc according to the requirements.
- This plate rolling machine is perfectly suitable for producing large roll bending machines having a thickness of 50mm or more.
- The bottom part of the lower roller in the plate rolling machine is accompanied by a row of fixed steel rollers in order to shorten the span of the two rollers, therefore improving the amount of precision of the final workpiece and the overall performance and efficiency of the machine.
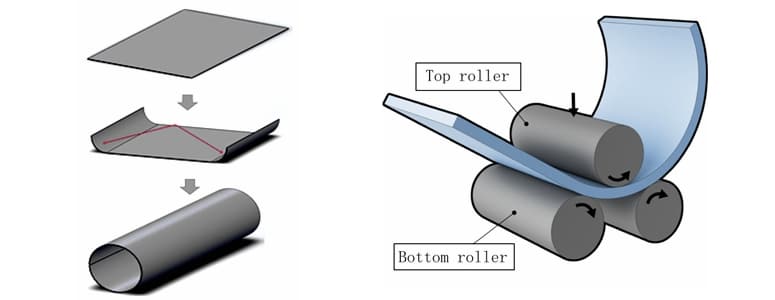
Classification of Plate Rolling Machine
There are different types of bending machines available based on their different fields of utilization. Based on the number of rollers present plate rolling machines are further divided into three-roller and four-roller. The three-roller bending machine is then further classified into a symmetrical three-roller bending machine, a horizontal downward-adjusting three-roller bending machine, an arc downward adjusting plate bending machine, an upper roller universal three-roller bending machine, and a hydraulic bending machine.
Based on the transmission point of the plate rolling machine they are classified as mechanical type and hydraulic type bending machines. The upper roll universal type machine is the most obsolete version whereas the horizontal down adjustment type machine is comparatively more advanced. Among all the Arc Down Adjustment type machine is the most recent of all.
1. Mechanical
The mechanical three-roller type bending machine is classified as symmetrical and asymmetrical
a) Mechanical three-roller symmetry
The structure of this machine is a three-roller symmetrical type structure. The upper roller of this machine moves vertically at the center at a symmetrical position of the two lower rollers. This configuration is obtained by the assistance of transmission of the screw nut and the worm. The rotational motion transmitted in the machine through the output gear of the reducer meshing with the lower roller gear provides the required amount of torque for the rolled metal plastic sheet. The biggest disadvantage that the mechanical bending machine suffers from is the need of pre bending of the end of the sheet metal plate (with the help of other equipment).
b) Mechanical three-roll asymmetrical
The structure of this machine is a three-roll asymmetrical type in which the upper roller functions as the main drive, and the lower roller moves vertically in order to clamp the plate firmly and mesh with the upper roller gear through the lower roller gear.
2. Hydraulic
The biggest benefit of hydraulic three-roller symmetrical plate rolling/bending machine is that the upper roller of this rolling machine can be very easily vertically elevated and lowered down.The vertical lifting hydraulic transmission of this rolling machine is obtained by the utilization of hydraulic oil in the hydraulic cylinders functioning on the piston rod. The lower roller inside the machine is driven in rotational motion, and the output gear meshes through the machine’s reducer. To provide the necessary torque required for the coil, an idler is present under the lower roller, which can be manually adjusted.
The upper roller of this machine is shaped quite similar to the design of a drum, which enhances the straightness of the product being made and is suitable for manufacturing of ultra-long tanks with various large cross-sectional shapes. As this rolling machine is an upward-adjusting symmetrical three-roller plate rolling machine, it can effortlessly roll and form metal sheets into circular, arc-shaped, and conical work-pieces as required according to demands within a certain range. One of the two lower rollers present in this model is the driving rollers and the other roller is the driven roller.
Parts of Plate Rolling Machine
1. Rollers
i) Top Roller
The upper roller present in this device is mainly composed of the main oil cylinder, bearings, and upper roll. The upper roll is an important part of this plate rolling machine. It is usually constructed out of 42CrMo and tempered after a thorough session of rough machining. Its quenching and tempering hardness range somewhere around HB 230 ~ 290.
ii) Bottom Roller
The bottom roller of this device is made of the lower roll, bearing seat, gear, sliding bearing, etc. It is perfectly suitable for operating at0 normal temperature conditions and uses with low-speed heavy-duty sites. The lower roller is constructed of high-quality carbon steel. They are thoroughly processed by rough machining and rounds of quenching and tempering process. Quenching and tempering hardness ranges around HB230 ~ 290.
iii) Supporting Roller
The supporting roller device comprises of a supporting roller, a wedge mechanism, and an adjustable hand wheel. The roller is manufactured out of 45# steel and has been quenched and tempered. There is a group of support rollers present in the machine. The user can easily adjust them up and down according to a load of rolled plates of required specifications. The support roller here is used for supporting the middle part of the lower roller in order to improve the rigidity of the lower roller.
This is done in order to improve the forming accuracy of the workpiece. In the metal sheet rolling process, work rollers are affected by the extreme operating conditions of the workpiece. These operating conditions include huge forces, high bending moments, thermal stresses, and wear. The manufacturer therefore must consider the strength, stiffness, and wear resistance of the material being used to manufacture when making the rollers.
2. Machine Frame
The frame of this mechanical device is composed of the machine body, the sliding plate, and the shaft sleeve. The frame is then welded and annealed later. This machine frame is utilized to in order to install the main hydraulic cylinders and assists in driving the upper roller parts to move horizontally.
3. Base
The construction of the rolling machine base includes a box welded structure, which is then quenched and stress relieved. This box is then utilized for the installation of various components of this machine. The frame, reducer, motor and other components and devices are installed on it, and then formed into a whole machine.
4. Main Drive System
The main drive device of this plate rolling machine basically consists of one main motor, brake, gear, reducer, bearing, etc. The system of this machine in order to provide power can rotate forward as well as reverse. The torque inside this machine is transmitted to the lower rollers through the assistance of the main reducer. The output gear and the lower roller gear together make the lower roller rotate. The motion of the lower roller relies on the friction between the drive and the plate to feed and complete the rolling work.
5. Movement Device
The movement device of a plate rolling machine is powered by an electric motor. This movement is then controlled through the assistance of the reducer, gear, worm, screw rod, and nut mechanism to in order to drive the movement of rollers. The horizontal moving device of this mechanical device is powered by the horizontal moving motor, whose function is to drive the frame and all the upper roller parts to move horizontally throughout the worm drive mechanism as well as the screw drive mechanism in order to realize the pre-bending procedure of the workpiece.
6. Turning Device
The overturning device of this plate rolling machine includes a sliding block, an oil cylinder, etc. The turning device is installed on one side of the overturning frame which is used for all the overturning operations and recovering. The major function of the turning device in a plate rolling machine is to ease out the product being taken out of the machine along the axial direction of the roller.
7. Balancing Device
The balancing device of this machine is composed of a beam, a support plate, and a rod. It is utilized for pressing the ends of the upper roller in order to maintain the balance of the upper roller after the overturning frame is completely overturned, such that it facilitates the unloading of the workpiece.
Advantages of Plate Rolling Machine
- Efficient
- Small size
- Light weight
- Simple structure
- Easy to manufacture and install
- Removable
Image Source :- shenchong