Monel (Metal) – History, Uses, Properties, Grades, Applications, Purpose, Advantages & Disadvantages
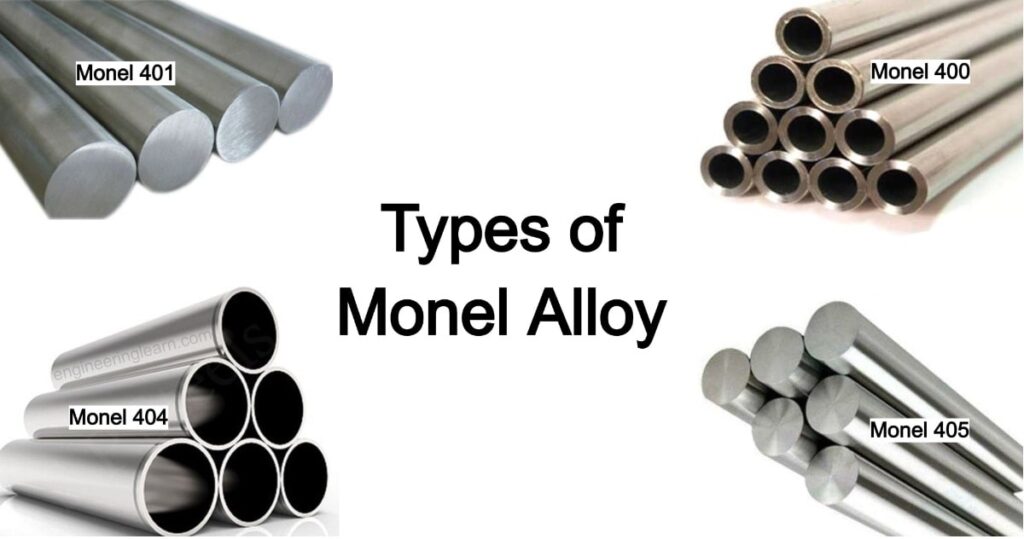
Introduction
Monel (Metal) – History, Uses, Properties, Grades, Applications, Purpose, Advantages & Disadvantages: – Monel is a family of nickel and copper alloys having trace quantities of iron, manganese, carbon, and silicon. Because it contains less than 60% copper, Monel is not a cupronickel alloy. Monel alloys, which are stronger than pure nickel, are resistant to corrosion by a wide range of hostile chemicals, including quickly moving saltwater.
Monel is a brand name for a class of nickel alloys largely made of nickel and copper, with traces of iron, manganese, carbon, and silicon. Monel alloys, stronger than pure nickel, are noted for their corrosion resistance in various hostile situations. In 1901, Robert Crooks Stanley invented the substance.
The microstructure of Monel, known as Superalloy, has a face-cantered cubic lattice structure. The ASME Boiler and Pressure Vessel Code have certified Monel alloy 400 as a building material.
History of Monel Alloys
Monel alloys are nickel-based alloys with a copper content ranging from 29 to 33 percent. Invented by metallurgist Robert Crooks Stanley and patented by the International Nickel Company in 1905. The metal was named Monel after the then-director of International Nickel. Unsurprisingly, Stanley rose to the position of Director of International Nickel.
Monel was utilized as a roofing material on Pennsylvania Station in New York before 1908. Monel was used for countertops, sinks, appliances, and roof flashing in the 1920s and afterward. While Monel was one of the most popular metals on the market throughout the 1940s, it was mainly displaced by more adaptable stainless-steel beginning in the 1950s.
What is the Purpose of Monel?
Monel is widely utilized in the maritime and chemical processing industries because of its ease of fabrication through hot and cold working, machining, and welding. However, because the material is expensive, it should only be utilized when cheaper options are unavailable. Monel piping is often more than three times the price of carbon steel pipe.
Valve and pump shafts; electrical and electronic components; crude petroleum stills, boiler feedwater heaters, marine fixtures, and fasteners; gasoline and water tanks; fuel tanks; springs; chemical processing equipment; process vessels and piping; heat exchangers; metal instruments; deaerating heaters; musical instruments; refrigerators; film processing; kitchen sinks; roofing; and eyeglass frames are examples of typical Monel applications. Monel is available in pipe, fittings, plate, strip, round bar, and flat bar forms.
Monel Alloy Properties
Monel is a solid-solution, single-phase binary alloy with good mechanical characteristics at subzero temperatures. Monel alloy 400 has a specific gravity of 8.80, a melting temperature range of 1300-1350 °C, and a Poisson ratio of 0.32. The mechanical characteristics of Monel Alloy 400 at room temperature are shown in the table below.
Machinability: Since Monel works hard during machining, machinability is extremely challenging. Techniques used to machine iron may also be used to machine Monel.
Welding: Monel welding techniques include gas-arc welding, gas-metal-arc welding, metal-arc welding, and submerged-arc welding.
Forging: Monel may be forged, but only under strictly regulated conditions.
Hot-working: temperatures for Monel alloy typically vary from 648-1176°C (1200-2150°F). The right temperature must be determined before beginning hot operations.
Monel Alloy Grades
Commercially, there are five varieties of Monel: ISO 6208 (plate, sheet, and strip), ISO 9725 (forgings), ISO 9723 (bars), ISO 9724 (wire), and DIN 17751 (wire) (pipes and tubes). These are the Monel grades:
Alloy 400 or Monel 400
Monel 401, 404, and 405, as well as Monel K-500
Monel Grade/Trade Name | ASTM/AISI Alloy Type | UNS No. | %Ni | %Cu | %Fe | %Mn | %Al | %Ti | %Si |
Monel 400 | B 127/ B 164 | N04400 | Min. 63 | 28-34 | Max 2.5 | Max 2.0 | Max 0.5 | ||
Monel 401 | N04401 | Min. 63 | 28-34 | Max 2.5 | Max 2.0 | Max 0.5 | |||
Monel 404 | N04404 | 52-57 | Remaining | Max 0.5 | Max 0.1 | Max 0.05 | Max 0.1 | ||
Monel 405 | B 164 | N04405 | Min. 63 | 28-34 | Max 2.5 | Max 2.0 | Max 0.5 | ||
Monel K500 | B 865 | N05500 | Min. 63 | 27-33 | Max 2.0 | Max 1.5 | 2.3-3.15 | 0.35-0.85 | Max 0.5 |
Compositions of Monel Grades
A) Monel 400
The following standards apply to Monel 400: BS 3075, 3076 NA 13, DTD 204B, and ASTM B164. It has high strength, great corrosion resistance, good flexibility, and thermal conductivity and is also known as alloy 400. Monel 400 is commonly used in heat exchangers, valves, maritime engineering, and chemical and hydrocarbon processing.
B) Monel 401
Monel 401 is a metal frequently utilized in specialized electric and electronic applications. The alloy offers good weldability and brazing qualities when welded with a gas-tungsten-arc process. Resistance welding is an excellent way to connect materials. Monel 401 is covered under the UNS N04401 standard.
C) Monel 404
Monel 404’s composition is precisely tuned to offer a very low Curie temperature, low permeability, and good brazing qualities. Monel 404 can be worked using standard welding and forging procedures; however, it cannot be hot worked. Cold working can be done for a superior finish. Monel 404 is widely used in transistor capsules and ceramic-to-metal seals and is covered by standards UNS N04404 and ASTM F96.
D) Monel 405
Also known as UNS N04405, Monel 405 is mostly used for automatic screw machine stock and is covered by ASME SB-164, ASTM B-164, Federal QQ-N-281, SAE AMS 4674 & 7234, Military MIL-N-894, BS3072NA18, BS3073NA18, QQ-N-286, DIN 17750, ISO 6208, BS3075NA18, BS3076 It is a free-machining alloy 400 grade. The sulfur content is raised to 0.025-0.060 percent, resulting in nickel-copper sulfides that improve machinability.
E) Monel K-500
Adding aluminum and titanium to the nickel-copper basis results in Monel K500, which has increased strength, hardness, and superior corrosion resistance. However, alloy K-500 has a higher propensity for stress-corrosion cracking in specific situations when age-hardened. Monel K500 is ideal for the shafts of centrifugal pumps used in maritime applications. Instruments, oil-well tools, electronic components, marine propellers, pump shafts, rotary impellers, doctor blades, scrapers, and oil-well drill collars are typical uses for alloy K-500.
Uses of Monel
1. Applications in Aerospace
In the 1960s, Monel metal gained widespread application in aircraft construction, particularly in the frames and skins of experimental rocket planes like the North American X-15, to withstand the intense heat created by aerodynamic friction during extremely fast flight.
2. Production and Refining of Petroleum
Monel is utilized in alkylation units that directly interact with intense hydrofluoric acid. Monel is extremely resistant to hydrofluoric acid at all concentrations, including the boiling point. It is possibly the most durable of all regularly used technical alloys. Under reducing circumstances, the alloy is also resistant to several types of sulfuric and hydrochloric acids.
3. Applications in the Sea
Because of its corrosion resistance, Monel is suited for use in pipe systems, pump shafts, seawater valves, trolling wire, and strainer baskets. Some alloys are fully non-magnetic and are used for anchor cable onboard minesweepers and magnetic field measuring equipment housings.
4. Instruments of Music
Monel is used for valve pistons and rotors in high-end musical instruments such as trumpets, tubas, and French horns. Roto Sound pioneered the use of Monel for electric bass strings in 1962, and a wide range of musicians utilized these strings.
Advantages of Monel
- The primary benefits that Monel provides are as follows:
- high corrosiveness acid and alkali resistance
- Alkali resistance.
- excellent flexibility (easy to shape and form)
- welding, brazing, and soldering simplicity
- high mechanical strength is available in a variety of shapes such as sheets, plates, rods, bars, pipes, and tubes
- appealing look and finishes
- the capacity to withstand both high and cold temperatures
Disadvantages of Monel
- Even though Monel has many advantages, it is not a perfect metal. It has drawbacks such as:
- Machinability issues
- Exposure to pitting corrosion in a saltwater climate.
- In the presence of Monel, galvanic corrosion can occur.