ESW Welding: Definition, Working, Uses, Construction, Components, Applications, Advantages & Disadvantages
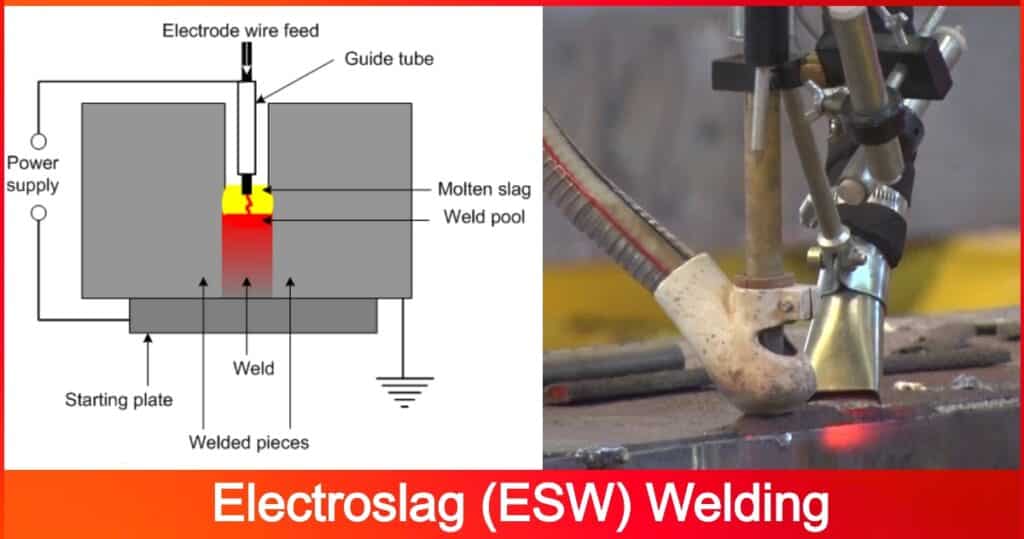
Introduction
ESW Welding: Definition, Working, Uses, Construction, Components, Applications, Advantages & Disadvantages: – ESW welding is a non-traditional welding process in which a molten metal pool is created. This technique is a combination of both arc welding and resistance welding on the grounds that at the beginning, heat is generated by laying out an arc between the electrode and base metal. This heat prompts melt flux and creates a molten metal pool between the electrode and base metal. Now the current flow moves through this molten metal pool and heat is developed because of electric resistance. Because of this reason, this is called a combination of arc welding and resistance welding.
What is Welding?
Welding is a material joining process in which at least two parts are combined at their contacting surfaces by a suitable application of heat as well as pressure. Many welding processes are achieved by heat alone, with no pressure applied; others by a combination of heat and pressure; regardless of all that others by pressure alone, with no external heat supplied. In some welding processes, a filler material is added to work with the combination. The collection of parts that are joined by welding is known as a weldment. Welding is generally associated with metal parts, however, the process is additionally utilized for joining plastics.
What is ESW Welding?
Electro slag welding (ESW) is a highly useful, a single-pass welding process for thick (more prominent than 25 mm up to around 300 mm) materials in a vertical or near vertical position. (ESW) is like electro-gas welding, yet the primary contrast is the arc starts in an alternate area. An electric arc is initially struck by wire that is taken care of into the ideal weld location and afterward, flux is added. Extra flux is added until the molten slag, reaching at the tip of the electrode, smothers the roundabout segment(arc).
The wire is then constantly taken care of through a consumable guide tube into the surfaces of the metal work pieces and the filler metal is then liquefied utilizing the electrical opposition of the liquid slag to cause coalescence. The wire and cylinder then climb along the work piece while a copper holding shoe that was put into the place prior to starting is utilized to keep the weld between the plates that are being welded.
ESW welding is utilized primarily to join low-carbon steel plates and additionally segments that are extremely thick. It can likewise be utilized on structural steel assuming specific insurances are observed, and for large cross-section aluminum bus bars.
What is ESW Welding Gap?
In ESW welding, Flux melts or liquefies wires and guide tubes. Later, the liquid metal sinks through the slag to the metal pool underneath and solidifies. Since the slag is less thick than liquid steel, it floats to the top and shields the metal from exposure to air. With the continued expansion of weld wire, the molten steel fills the gap, solidifies, and melds the two parts. The weld terminated when it reaches the highest point of the run-out cooling shoes over the rail running surface. Pointless weld reinforcements are eliminated right away, while the weld is hot.
A DC current of 750-1000 An is applied from a DC generator with a flat volt-ampere. Load voltages by and large range from 30 to 55 V, so the minimum open circuit voltage of the power source ought to be 60 V. The speed range of ESW welding is 17 to 150 mm/s.
What is the Principle of Electroslag Welding?
It works on the normal rule of heat generation because of arc and electric resistance. In the beginning, the arc is produced between the welding electrode and base metal which tends to melt filler metal. This filler metal will fill the cavity to some degree. Presently the current passes through this extended surface and heat generate because of electric resistance. This heat further will in general melt filler metal which is constantly taken care of by the roller. The filler wire is fed through the roller persistently. This wire took care of the tube which direct its flow. This filler wire melts and fills the weld and the strong joint is created.
Why is ESW Welding Used?
It is very efficient to weld small metallic pieces utilizing traditional welding techniques. With regards to welding materials that are thicker than 30mm, ESW welding can be a suitable replacement. This process of welding can be utilized to weld materials ranging from 30mm to 300mm. ESW welding is a solitary pass welding process, subsequently, welding thick materials are exceptionally helpful.
Construction of the ESW Welding Process?
- The construction of ESW welding isn’t very complex.
- The base plate goes about as a positive electrode and the filler wire goes about as a negative electrode.
- Two workpieces to be joined are kept on the base plate.
- The filler wire is embedded in the cavity from the top and is perpendicular to the base plate.
Components of ESW Welding Equipment
1. DC Power Supply
A DC power supply is utilized on account of ESW welding. The potential difference ranges from 40V-50V which is mainly created by the power source. Current relies on the thickness of the work-piece to be welded, for the most part, the current supply is 600A or more.
2. Filler Wire
A filler wire is utilized as another electrode, it is utilized to create an arc while coming in contact with the flux. There is a continuous supply of filler wire utilized in the ESW welding process.
The filler wire is directed to the right position utilizing a consumable guide tube. The carbon rate in the filler wire is not exactly that of base metal this forestalls cracking of the weld because of the high carbon percentage.
3. Base Plate
The base plate goes about as one of the electrodes utilized in ESW welding. The Power supply from one terminal is further connected to the base plate. It is otherwise called the starter plate. It additionally supports the entire setup of ESW welding.
4. Workpieces
Work-pieces are the metals to be welded together, the two work-pieces are held upward in an ESW welding arrangement. The welding activities occur in an upward direction.
5. Flux and Slag
Flux might be supposed to be the main filler material utilized in ESW welding. Flux is included in the form of powder and afterward is melted in view of the arc produced.
The fact that floats over the flux make slag the waste material. The flux utilized in ESW welding should have the accompanying properties.
- It should change electrical energy to heat energy in its molten state.
- It should protect the weld from atmospheric gases.
- It must conduct the electricity simultaneously and should offer sufficient resistance to generate heat.
What is the Working of Electroslag Welding?
Electroslag welding works on the guideline of joining two metals together with heat generation between them because of arc and electric resistance. The arc is first created by applying an expected difference between the base and the electrode. This arc melts the filler and fills the cavity. Then the filler is melted because of the resistance offered by the slag. Presently the electrode wire and filler melt to shape a filet weld in the upward direction between the work-pieces.
Step-by-step Working:
- At first, the flux is fed inside the cavity then the power supply is started.
- At the point when the filler wire touches the base plate through the flux, there is the generation of arc because of a short circuit between the filler electrode and the base plate.
- This arc produces heat that is adequate to melt the flux. This is the principle of arc welding utilized in ESW welding.
- After the arc is produced and the flux is melted the weld progresses in the upward direction.
- More flux is added from the top, now the heat generation happens because of the resistance offered by the molten flux and the process seems to be like resistance welding.
- This helps in fusing the walls of the work-piece and the consumable wire. Thus a weld is formed between the two work-pieces.
- The weld formed is because of the molten filler wire, molten flux as well as fusing of the walls of the work-piece.
Applications of ESW Welding
- In the first application, Fabrication of high-pressure vessels, and framing of weighty mechanical and water-driven presses.
- It is utilized in heavy industries and ventures where plate thickness depends on 80 mm to be joined.
- Welding of thick-walled large diameter pipes is done by the ESW welding process.
- Welding of storage tanks is finished by ESW welding.
- Developing large and thick parts of ships is utilized in ESW welding.
- Utilization of ESW Welding of construction, hardware, ships, pressure vessel, and projecting. Applicable to long butt weld.
- Welding of construction, apparatus, ships, pressure vessel, and projecting.
Advantages of ESW Welding
Below are some advantages of ESW welding: –
A) Material Thickness
One of the significant benefits of ESW welding is that it tends to be utilized to weld thick work-pieces together. This is beyond the realm of possibilities utilizing conventional welding techniques. Work-pieces ranging from 30mm to 300mm can be welded utilizing ESW welding. It tends to be utilized in heavy manufacturing industries where the strength of the weld is the key concern.
B) Minimum Cold Cracking
Cold cracking is a phenomenon in light of which cracks are developed on the welds because of sudden cooling of the welded areas. On account of ESW welding, the welds don’t cool out of anywhere, preventing or forestalling then cold cracking on the welded areas.
C) High Deposition Rate
The deposition or testimony rate in a welding process can be named as the mass of metal deposited in the cavity with respect to time. It is by and large calculated in gm/min. On account of ESW welding, the deposition rate is around 330gm/min which is significantly more than traditional welding techniques.
D) Minimum Slag
Slag is the waste product produced during the process involved with welding. Slag may weaken the welding regions. ESW welding advances low slag deposition than traditional welding techniques.
E) High Productivity
Productivity and efficiency is a significant perspectives while working in any manufacturing industry. The process of ESW welding can be made self-automatic which might help in faster welding of the work-piece.
Disadvantages of ESW Welding
Below are some disadvantages of ESW welding: –
A) High Heat Generation
Heat generation in ESW welding is exceptionally high. This requires an additional cooling system to assimilate heat from the heat-affected zones. High heat generation additionally brings about thermal cracking of the welded areas. This may likewise diminish the toughness of the weld.
B) Large Grain Size
The grain size of the welds is huge on account of ESW welding. This outcome in less compact welds. This is one of the significant limitations of ESW welding.
C) Restricted Position
The ESW welding process happens just in the upward direction. Horizontal welding is beyond the realm of possibilities as the molten metal pool is large and won’t spread uniformly.
D) Unsuitable for Cylindrical Objects
ESW welding is certainly not a reasonable process for welding cylindrical objects. This is because of the curved surface area of the cylinders. The molten flux will flow away from the work-piece because of the curved surface bringing about the improper and weak weld.
E) High Cost
The overall expense of the equipment and the cost of running both are high for ESW welding when compared to traditional welding techniques. The filler wire and flux requirement are a lot higher than other welding processes.
Conclusion
Heavy plates require Single pass welding than multi-pass welding strategies. In the mid-1950s, Russian scientists declared the single-pass vertical weld by the principle of electrically conductive slag. Electroslag welding is presently not to be considered as simply one option to splice thick plates in a steel fabrication shop. It can economically weld stiffener, progression, and base plates to the flanges of steel shapes, and attach diaphragms to the inside walls of box columns.
Modern technological advances in ESW, embodied in ESW-NG, plays likewise extended part to the building site of a significant elevated structure and extension development. ESW-NG is winning over be the most practical decision at numerous associations, for the dependable creation of thick welds in steel extensions and structures.
Image Source: – substech, weldingtech