Broaching Machine: Definition, Types, Methods, Operations, Advantages & Limitations
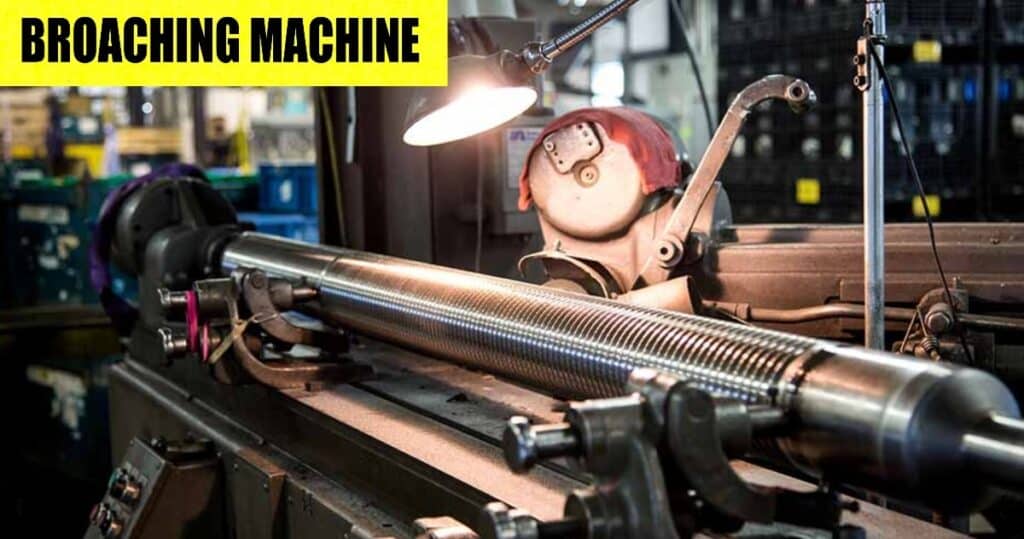
Introduction
Broaching Machine: Definition, Types, Methods, Operations, Advantages & Limitations: – Broaching is a strategy of removing metal by pushing or pulling a pulling device called a broach which cuts in a fixed path. In broaching, the multi-cutting tool moves while the workpiece stays static, or the workpiece moves while the instrument is static. Now and again, there might be relative rotation between the tool and the workpiece. The broaching tool can be internal through the focal point of the workpiece or outer across the outer layer of the workpiece.
What is Broaching Machine?
In Broaching machine, the tool of the machine is pulled or pushed through the surfaces to be done. With the assistance of broaching, finishing is done on flat or contoured and either internal or outer surfaces. Broaching is restricted to the evacuation of around 6mm of stock or less.
The term broaching may have derived from an old Roman word braccus which implies an object having projecting teeth. The operation itself dates just to the 1850s while broaching tools when called “drifts” were hammered in metalworker shops through the work or pushed with an arbor press.
What is Broaching Machine Operations?
Broaching is applied for machining different internal and external surfaces, for round or irregular shaped holes from 6 to 100mm in diameter, and for external flat and shaped surfaces.
Specific kinds of surfaces, for example, spline holes, are machined at present exclusively by broaching because of the exceptional difficulties in machining such surfaces by different strategies.
A few operations are done in one pass, however, some operations are sorted out for repeated cuts to the design of the broach.
The teeth of a gear or spline might be broached all together or each or a couple at a time. A relatively simple broach can be made to cut one or a couple of tooth spaces. After one pass, the gear blank is indexed and a greater amount of its teeth are cut. Progressive passes are made until all the teeth are finished.
Types of Broaching Machine
Broaching machines are the most simple of all machine tools. Broaching machines comprise a broaching tool, a work-holding fixture, a drive mechanism, and a suitable supporting frame. Albeit the components are not many, a few varieties in design are conceivable.
There are two principal kinds of broaching machines: – horizontal and vertical.
Notwithstanding these standard types, there are unique and constantly operating machines. Both horizontal and vertical sorts of the machine have at least one ram relying upon production demand.
Dual-ram models are organized so that when one slams in on the cutting stroke, the other is on the return stroke; the return stroke is performed rapidly to acquire time, which is utilized to unload and load the machine.
Broaching machines regularly push or pull the broach through, or past a workpiece that is held in a fixture. On certain machines, notwithstanding, the workpiece is moved beyond a broach that is fixed in its situation. Most broaching machines are hydraulically operated to get a smooth, uniform cutting action.
1. Horizontal Broaching Machine
Nearly all horizontal machines are of the pull type. They might be utilized for either internal or external broaching, albeit internal work is the most widely recognized. It comprises a bed or a base somewhat more than two times the length of the broaching stroke, a broach pilot, and the drive mechanism for pulling the broach.
Horizontal broaching machines are utilized principally for broaching keyways, splines, slots, round holes, and other internal shapes. They have the limitation of taking more floor space than the vertical machines.
2. Vertical Broaching Machine
Vertical broaching machines are utilized in numerous operations since they are convenient to pass work starting from one machine and then onto the next. Of the three models accessible, pull down, pull up, and push down, the pull-up type is more popular. Vertical broaching machines require an operator platform or a pit and are more prudent of floor space than the horizontal type.
Modern vertical broaches are presented with both hydraulic and elector-mechanical drives. Be that as it may, water-powered drives are the most widely recognized on the grounds that they cost less.
3. External Broaching Machine
These are also called surface broaching machines. These machines are utilized to deal with the outer surfaces of the workpiece. Eternal broaching machines are additionally utilized for Contour broaching. Contour broaching includes the readiness of concave or convex surfaces or some other shape with incredibly close resistances.
4. Surface Broaching Machine
A surface broaching machine eliminates access material from the external layer of a workpiece. The cutting tool passes the workpiece to create flat surfaces. The unique feature or component of a surface broaching machine is that the cutting tool is attached to a ram that is constrained along past the workpiece. The ram can move horizontally or in a vertical direction depending upon the design of the machine. It is feasible for a surface broaching machine to have two rams; this is depicted as duplex broaching.
5. Continuous Broaching Machine
For large-scale Broaching of small parts, the highly useful continuous broaching method is utilized on rotating or even horizontal continuous broaching machines.
In the rotatory continuous broaching machines, the workpiece is stacked on the table which rotates determinedly. During the operation, the broach is fixed.
In the horizontal continuous broaching machines the workpiece travel as they are conveyed by a perpetual chain. The workpiece are loaded into work-holding fixtures mounted on the constantly moving chain. During the operation, the broach is fixed as previously.
6. Turn Broaching Machine
Turn broaching machines are utilized for circular, linear, and spiral cutting where surfaces need a high completion. The tool has various inserts to eliminate material by rotating the crankshaft between centers. The components of a turn broaching machine are quite capable of getting done or roughing. The sort of machine determines the tool.
Roughing inserts and their segments rely upon the requirements of the stock evacuation rate. The finishing segment has flexible cartridges, which are ideal for producing tight resistances.
7. Rotary Broaching Machine
Rotatory broaching is unlike different types of broaching and is known as wobble broaching. It is an accurate technique for producing polygonal shapes internally or remotely. In rotatory broaching, the cutting tool is put at a 1° angle to the centerline of the workpiece, which makes the broach cut with an etching or scalloping effect.
Rotatory broaching can be completed with a lathe or factory utilizing a horizontal or vertical shaft machine where the spindle is permitted to spin freely. The shapes that can be created utilizing rotatory broaching include hexagons, squares, serrations, keyways, involute, spline, spike stuff, numbers, and letters.
The rotatory broaching tool holder permits the broaching process to work and cuts each part of the form at a time. The broach is taken care of into the part and cuts the full structure in one pass. The broach bit is designed with a back taper to prevent it from pushing into the workpiece while taking care of the broach into the pilot hole.
What is Internal Broaching?
The two sorts of internal broaching are rotatory and vertical; they are designed to increase the size of a hole in the workpiece. All internal broaching requires the creation of a starter hole alluded to as blank prepping. Vertical broaching can be pushed or pulled. Rotatory broaching is utilized when making an asymmetrical hole in a solitary pass is essential.
Internal broaches are located on their shrank and held set up by a set screw clamp with a whistle notch.
Different Types of Broaching
(i) Shell Broaching
Shell broaches are located or semi-finishing, roughing and finishing. Any part of a shell broach can be supplanted or sharpened.
(ii) Keyway Broaching
A keyway broach cuts an opening in the bore of the workpiece and is supported by a fixture, alluded to as a horn, which locates where the keyway is to be cut.
(iii) Round Hole Broaching
Round hole broaching is the least difficult of internal broaches. A circular opening has a progression of teeth that encircle the tool with teeth designed to cut the external edge.
(iv) Gun Barrel Broaching
A gun barrel broach is extremely lengthy and equipped for moving the full length of the barrel. It has exceptionally fine teeth since barrel grooves are exactly moment at a couple of thousandths of an inch deep.
(v) Internal Gear Broaching
An internal gear broach nibbles at the internal surface of the workpiece to produce a gear profile.
(vi) Cut and Recut Broaching
A cut-and-recut broach have a breathing area behind it that keeps the walls from springing back. The front of the tools cuts the spline and is followed by a second cutting tool that recuts the cut section.
(vii) Concentric Broaching
A concentric broach is a full-structure finishing tool that has round and spline teeth to shave the diameter and spline structure.
(viii) Square Broaching
Square broaches are utilized to broaden, shape, and finish irregular shapes. Their purpose is to change a circular opening into a square utilizing a rotating broach holder that points to the propose with the end goal that only one corner is being cut at a time.
Different Broaching Methods
Following are the classification of broaching methods:
A) Pull Broaching
The role of pull broaching is that it is held fixed and the broach is pulled through the work. Normally, broaches are extremely lengthy and are held in a special head. The Pull broaching technique is utilized for internal broaching however it is additionally utilized for some surface broaching.
B) Surface Broaching
In surface broaching either the work or the broaching or tool device moves get across the other. This strategy has turned into a significant method for surface finishing. Numerous irregular or complicated shapes can be broached by surface broaching, however, the tools should be specially designed for each work.
C) Push Broaching
The role of push broaching is fixed and the broach is further pushed through the work process. Hand and hydraulic arbor presses are generally utilized for push broaching. This technique is utilized for measuring openings and cutting keyways.
D) Continuous Broaching
In continuous broaching the work is moved persistently and the broach held stationary. The movement of work might be either straight horizontal or roundabout. The continuous broaching method for the most part utilized for broaching various comparative works simultaneously.
Advantages of a Broaching Machine
- High production effectiveness and low processing cycle can diminish the processing cost of a solitary product in large-scale production.
- Broaching machines can complete parts processing tasks that require combined processing of gear hobbing machines, gear shaping machines, and milling machines in a brief time frame.
- Broaching machine is additionally utilized for the high-accuracy machining of difficult-to-cut materials, for example, turbine disks utilized in the manufacture of generators and airplane motors.
- The workpieces processed by broaching have a higher surface completion, higher dimensional precision, and smaller tolerances.
- The broach has a calibration part, whose function is to align the size and trim the amount of light.
- The cutting speed of broaching is, for the most part, low and the cutting thickness of each cutting tooth is small, so the cutting process is moderately steady, what’s more, the adverse effect of a pseudo-chip edge can be stayed away from.
- The structure of the broaching machine is simple, the broaching operation is also simple, and the skill requirements for laborers are low. There is just a single principal development in broaching, or at least, the linear movement of the broach.
- The feed movement is acknowledged by the way that the last tooth of the broach is higher than the past one.
- The height of the tooth is known as the tooth lift, so the broaching machine. The structure is simple and straight forward and the operation is helpful.
- The broach has a longer service life.
- The cutting speed during broaching is low, every tooth only needs a small incision in one activity, the tool wears gradually, and the sharpening once can handle barely any dry workpieces, and one broach can be reground at most times, so the broach has a long service life.
Limitations of Broaching Machine
There are likewise a few impediments to utilizing broaching machines:
- As the structure of the broaching tool is more complicated than that of the general hole machining device, the manufacturing of the broach tool is more troublesome and the expense is higher, so broaching machine is normally suitable for large-scale manufacturing.
- In single-piece and small-batch production, with the exception of some processing applications that require high accuracy or unique shapes, the expense of producing with a broaching machine isn’t savvy.
- The surface to be broached can’t have an obstruction. Broaching can’t be utilized to eliminate a lot of stock.
- Parts to be broached should be fit for being rigidly supported and should have the option to endure the force that is set up during cutting.
- Broaching is just reasonable for low chip load or light cutting.
- A separate broach is required at whatever point the geometry of the workpiece changes.
Conclusion
Each type of broaching is unique and designed to satisfy the needs of a specific application. There are areas where broaching is the most ideal tool to make it happen, for example, cutting parallel and multiple surfaces, fast cutting, automated cutting, exceptionally large production runs, and intense hard materials. A few sorts of metal shaping operations can be replaced by the execution of broaching to save time and utilize fewer tools. Any type of metal alloy can be replaced, however, it works best on soft metals like aluminum, copper alloys, certain forms of plastic, wood, and mid-range kinds of steel.
Content Source: – iqsdirectory, Chengchun
Image Source: – millerbroach