Types of Conveyor System: Definition, Application, Working, Uses and Design
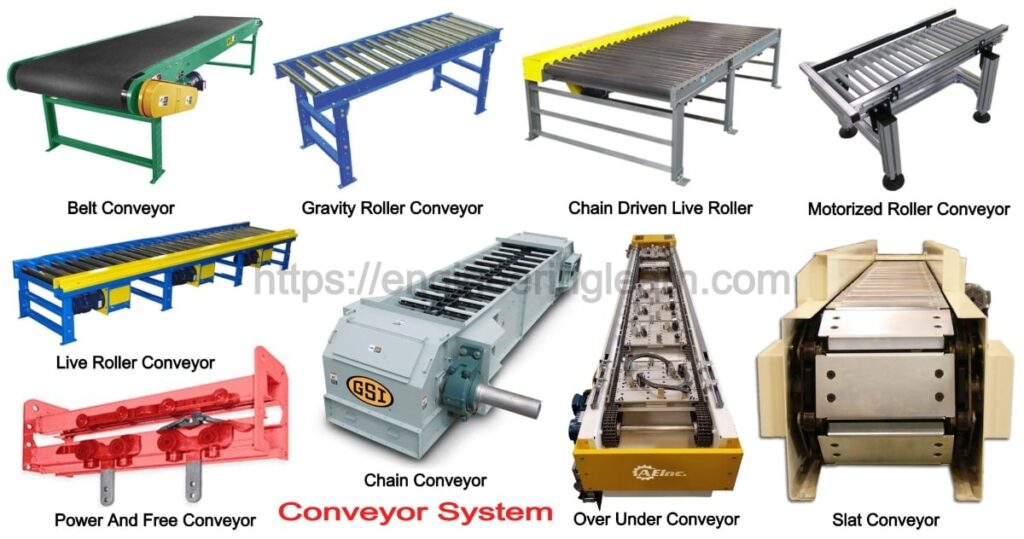
What is Conveyor System?
Types of Conveyor System: Definition, Application, Working, Uses and Design :- A conveyor system is referred to as a common piece of mechanical handling equipment which is used to move the materials from one place to another. Conveyors are mostly useful in the application of transportation of the heavy and bulky materials. The conveyor system is the one which allows quick and efficient transport for a wide variety of materials, which is found making them quite popular in the material handling and packaging industries.
The conveyors are found having various different designs and uses. Common types of conveyors are belt, roller, motorized roller and overhead conveyors. These are categorize as floor style which are mounted on the floor and overhead. Uses of such conveyors are mentioned below. Scroll down to know more about conveyors in detail.
Uses of Conveyor
The uses of conveyors are in various industries about which the detail is mentioned below.
- Conveyors systems are used for moving the products from one place to other place.
- Conveyors are used to carry the products which are too heavy and cannot be lifted by the labour.
- These systems can be used in order to move a product while the operators are working on it.
- In huge industries these conveyors are used to avoid injury to workers from repetitive movement or in order to prevent damage from the products which can be caused by the movement.
- The conveyor system is used in order to deliver the products to a robot for processing or in order to receive the products from a robot which are already for the further steps.
- These systems are also used in storage and buffering of resources.
- The conveyor system can also be used to store products between within the processes or at the final step during the processing.
- The conveyor system can be used to create a buffer or accumulation bank which is a flexible storage system and can be used it wherever the quantity of products in storage can be lower or higher as per the requirement to balance the process flow.
- These can be used to either sequence or re-sequence the products within processes. There are system like Power and free systems which can provide this.
- Conveyors are one of the most flexible types of industrial equipment which is mostly installed with an aim to improve the productivity, efficiency and safety in the industry. These are also used in order to transport bulk materials too. For instance, gravel or iron ore.
How to Select Right Type of Conveyor?
Introduction
First of all there should be some basic product information. It is quite helpful in understanding the productive role that the system will be performing. Based on these factors one can select the various types whichever are available and then see which ones can do the job perfectly and provide the best results.
Next thing which can be the constraint is the availability of space in the production environment which can be at a real priority. Although the conveyors can add a lot of productivity, they can also get in the way of other operations, therefore one must carefully check the space which is being occupied as this gives the input for thinking whether to use it at a floor level or in an overhead style.
Floor or Overhead
Conveyors are categorized as floor style or overhead style as this is an important decision point. Overhead styles are referred to as those which can take various different forms which are found to share the benefits that the system itself is mounted on the part on which it is moving. So, they can use a production space which is not at all occupied with all the other equipment. This can be used to enable the overhead plant space in order to become productive, like using it for a buffer or storage bank. In case more space is available, floor style systems may found to be more suitable which include belt conveyors, gravity roller, skate wheel and slat conveyors.
There are some processes which need accurate positioning of the part for instance, robot loading or unloading. The system which is equipped with tooling, pallets or carriers is used to accommodate this. A simple belt or roller conveyor by itself cannot maintain the part in an accurate location. The speed which is required, investment available can drive the choices. Simpler, faster and more affordable systems are found to be great. Whereas other solutions are found to need more sophisticated automated conveyor lines.
The overhead conveyors are referred to as one type of motorized roller conveyors which are also often used together with warehouse robots along with the autonomous mobile robots. Warehouse robots are found to pick up and drop off the loads from your existing conveyors which provide a flexible way of link all your conveyor styles together for the maximum productivity and space utilization.
9 Different Types of Conveyor System
The material which is below has a brief summary of each one of the more common conveyor types that are available.
1. Belt Conveyor: ( Types of Conveyor )
These conveyors are also termed as Conveyor belts by most of the people and is actually referred to as the belting material wherein a belt system is one of the simplest conveyor type and moves parts from one place to the other place by reducing the human efforts. The speed of such conveyor systems can be varied with a variable speed drive. But on the other side it is suggested not to use the belt systems as a working surface. These instruments cannot be used to present the parts of any robot or buffer or the sequence parts. Whereas their simplicity is used to make them one of the most common conveyor types available amongst all the other types.
These conveyors belong to the floor mounted category. The belt conveyors are usually found moving the belt across a supporting steel plate in order to get slided whenever the belt moves. This style is referred to as a slider bed style wherein the belt can be supported on the top of the closely spaced rollers. These conveyor belt types are also referred to as roller belt style or roller conveyor belt and are also found to be simple and affordable parts of the conveyor system.
2. Gravity Roller Conveyor: ( Types of Conveyor )
Gravity roller conveyor is also one of the simplest type of conveyor system and is also quite affordable. A series of rollers are mounted on a side frame which provides the rolling surface. Whenever mounted on a decline angle the parts are found moving by their own selves. Whereas using gravity conveyors for parts of different size and weight can be more difficult as the user will need to control the speed and angle so that the part which are running into each other may not cause any damage. Comparing it with the carrying parts from one end to another, a gravity roller table is often a great starting point which is a very simple productivity improvement.
3. Chain Conveyor: ( Types of Conveyor )
Floor mounted chain conveyors are one of the best conveyor systems for heavy items. These are the systems which are especially used for items which are found having an uneven lower surface. The conveyor chain is used for providing two or three contact points on the bottom of the load. As much as the chain is moved, it is found carrying the products forward. These systems are used to carry pallets and large industrial containers. The products are sometimes mounted on a fixture as well after which the fixture is carried along the chains. This is a very popular application in the auto plants. These systems are found to be quite heavy duty and generally moves at a quite slow speed.
4. Live Roller Conveyor Or Chain Driven Live Roller (CDLR): ( Types of Conveyor )
Various numbers of time people are found using the acronym CDLR in the industries. In case anyone is found combining the rollers from a gravity conveyor along with the chains of any chain driven system then the rollers can be linked. To construct a live roller conveyor or chain driven live roller system, there is a need to add a motor and a gearbox and it’s done.
These are the members of the floor conveyor and are found having heavy duty material handling systems. These are the mechanical instruments which are used to transport the pallets, seats, tires, containers etc. In case these are fixed with a loose plastic sleeve over the rollers then these can be termed as accumulated or buffer products. The rollers are found to continue moving although the product on the top does not move. The chains are found to be linked along with one roller to the next on the other side.
5. Motorized Roller Conveyor: ( Types of Conveyor )
Motorized roller conveyors are referred to as those conveyors which are found having motor inside the rollers and these are not just the normal motors, these are the modern motors with higher capacity and higher speeds of around 200 feet per minute or even more. These types of conveyors use mostly one or more number of motors which are driven roller per zone in order to create a series of zones along with the conveyor.
The motorized roller gets connected to the other rollers in the same manner by plastic or reinforced belts. The photo eyes present are responsible for turning the motors on and off, and the parts are found moving to the next zone wherever the space is available. This is the way by which the parts never touch each other and thus the damages are avoided. This is also termed as zero pressure accumulation which is a quite valuable benefit. One additional benefit is that you can convert a gravity conveyor into a motorized roller system as well.
6. Slat Conveyor: ( Types of Conveyor )
A slat conveyor is referred to as that conveyor which is simply a two-strand chain system along with slats which are connected to the chain and a guiding system for the slats. This is responsible for creating a smooth surface in which the tooling details or fixtures are found to be mounted. These are the conveyors which are used to hold parts in any specific position.
At time the fixtures can also found to be the part in order to rotate at an angle of either 90 degrees or 180 degrees which is similar to that required in various airplanes. So, the user can use the slat conveyors as a working surface for the assembly operations where positioning of the part is also required to be accurate . Therefore, it is popular to perform the loading as well as the unloading operations at one or more ends, particularly of a slat conveyor. The user must try to work on the surface while it moves along.
Considering the overhead family of conveyor types, the simplest types are referred to as the hand pushed beam trolley systems as there is a use of enclosed track or I-beam section as a track. These are the types of conveyors which are found to be extremely versatile, easy to set up and affordable as well. Mostly these are the systems which are mounted above the workplace along with the roof-supported or floor supported steel structures.
Beam trolley is the system which is especially known for conducting painting and finishing operations. The overall mechanism remains above the part and is not covered at all by the spray. Beam trolley animation is also responsible for moving the parts along with the I-beam or the track system.
7. Motorized Overhead Conveyor: ( Types of Conveyor )
These are referred to as one of the most common types of conveyor systems and are also termed as monorails which is an overhead conveyor with the trolleys connected together using a chain. The chain is mostly enclosed or is opened below an I-beam. These are the style of material handling systems which are installed in nearly every high volume production facility.
This chain is driven along with a motor, a gearbox and the parts which are to be moved are suspended from the trolleys which are attached to the chain. These types of conveyor systems are found having various different attachments of these types. For all the complex parts, there is a fixture or carrier which is suspended from various trolleys in order to locate the part in position. The chain is always found running, or alternatively the system can index due to which this parts moves from one assembly station to the other at an undetermined time interval.
8. Power And Free Conveyor: ( Types of Conveyor )
Power and free conveyor are referred to as those conveyors which also belong from the overhead family. These conveyor systems are like a regular motorized overhead system, except that it is found having two tracks. The first track has the chain which moves continuously whereas in the other track, the trolleys are found moving along with the chain by using pusher mechanisms also termed as pusher dogs. These are the systems which are mounted at regular intervals on the chain.
Whenever the two trolleys are pressed against each other, the pusher dog gets slide over the top. Similarly, there is a stop blade which is used with a pneumatic cylinder in order to replicate this geometry which allows the trolley to start or stop the virtual movement anywhere in the entire system. This versatility is responsible for making the power and free conveyors one of the most productive style of the overhead systems. These systems can be started, stopped, buffered and re-sequenced by the usage of switches.
9. Over Under Conveyor: ( Types of Conveyor )
An over under conveyor is referred to that conveyor system which is similar to the overhead configurations, except one factor which is that the track is on the ground and the load is above the track. These types of conveyors are usually found useful in the paint finishing applications in order to avoid dust or oil dripping onto parts. These types of conveyors are widely used in the automotive final assembly operations.
Electrical Controls of Conveyors
Similar to the wide range of conveyors which are used for any application, there are the electrical control systems. The simplest conveyor system is found not having any electrical control. These types of systems are the ones which include gravity roller and the hand push overhead style beam trolley. Motorized systems are the ones which can use simple start-stop switches for their applications.
Advanced Controls
The Programmable logic controllers (PLCs) are found to be installed for the larger systems as they are found controlling the conveyors and also other process equipment. These are the systems which are often fitted with a variable frequency drive in order to adjust the speed of the AC motors. The DC electric motors in 24V are the systems which have their own specialized motor controllers. This is responsible for enabling the inputs from the sensors and processing the outputs and network connectivity through the ethernet.
How to Design A Conveyor?
The amount of time which is spent in designing a conveyor application can range from few minutes to few weeks or months. Usually the more is the length of the conveyor, the more time is taken in the designing stages. So here are three categories of simple, intermediate and advanced conveyor projects. Let’s have a look on these to understand their designing.
1. Simple Conveyors
Most of the simple conveyors are found having rollers, belts or simply just the hand push overhead applications which are found to be less than 20 feet in terms of length. The primary use of such conveyors is to move the product from one point to another point in a straight line only. The design process of such conveyors is quite simple and mostly involves selecting the best conveyor for the job. Use a belt, roller or motorized roller conveyor in case you want to lift it up from the floor. This type is also quite simple in terms of installation and can be as easy as assembling the legs on a roller conveyor or MDR conveyor
2. Intermediate Conveyors
These are the types of conveyors which are mainly preferred by the team leaders, manufacturing engineers or hands-on business owners who are having a good understanding of their process requirements. The design process of this type of conveyor system is found having a couple of more steps that include a more detailed understanding of the product which is being carried. For instance, if any conveyor system passes via robot cell or a paint booth for the intermediate systems various users do the majority of the design work, and often do the installation as well.
In case you are planning an overhead style system then you need to follow each and every step of the designing part in order to install the motorized overhead conveyors. The best part which attracts the customers for intermediate conveyor systems is that the customer need not to pay for any project engineering cost which means that the bill of material for all the conveyor components specifies each and everything which would be needed to install and get your system running. Working on the installation part is not that difficult, any person from a technical background can install the machinery. There are companies which provide with the installation service also, wherein the technicians work with high accuracy.
3. Complex Conveyors
These are the types of conveyors which are considered to be substantial conveyor system in terms of design and specialist conveyor engineering skills are required to operate and install such types of conveyors. The projects are found making movement from the intermediate category to the complex category as the entire length of the system and the number of conveyor path alternatives are found to increase. The parts which are used are switches, bypasses, buffers, cross-overs, lifting stations and various other conveyors. Highly complex conveyor technology like power and free conveyors are found to fall in this type of category. Installing these types of systems is always done by an experienced contractors as typically either any technically expert person or a specialist conveyor installer who can help in the installation in an easy manner.
Image Source :- aeinc, hurontechnology, grainsystems