Types of Bricks: Composition, Properties & Manufacturing Process [Complete Guide]
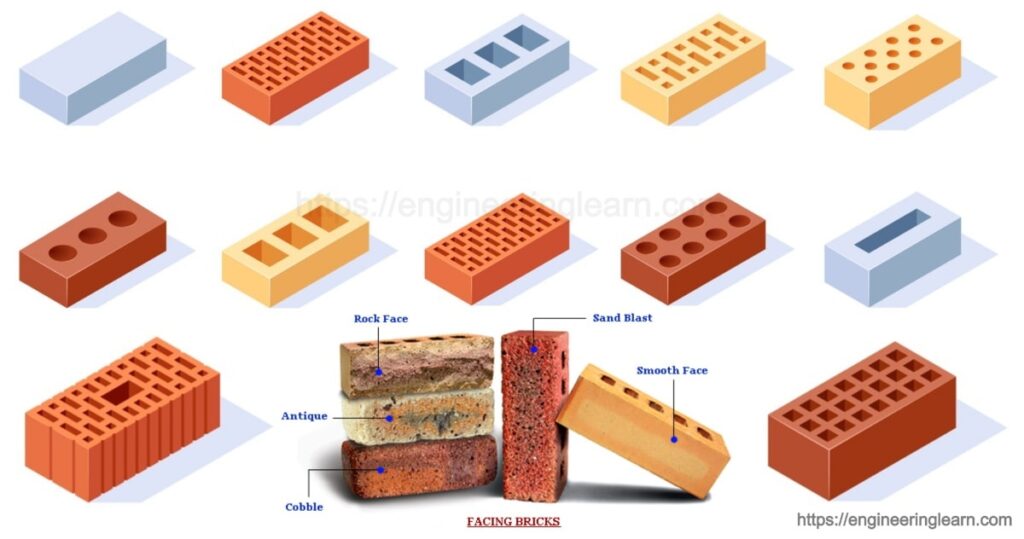
What is Bricks?
Types of Bricks: Composition, Properties, Manufacturing Process & Applications :- Brick is one of the oldest and popular building material used till now a days because of being cheap, durable and easy to handle and work with. Bricks are light in weight therefore bricks replace stones. It is rectangular in shape and can be conveniently handled with one hand. Bricks are obtained by molding clay and then by drying and burning these blocks.
Composition of Bricks
1. Alumina: (Types of Bricks)
It is one of the major constituent of every clay. A brick should contain alumina in between 20 to 30 %. Alumina in brick earth provides plasticity so that it can be molded easily. If alumina is in huge quantity, raw bricks may leads to shrink and warp during drying and burning.
2. Silica: (Types of Bricks)
A good brick earth should contain about 50 to 60 % of silica. Silica provides the bulk to brick earth, uniform Shape and size of brick is maintained by Silica. It exists in clay in free or combined form. Silica is helpful for the prevention of cracking, shrinking and warping of raw bricks. Excess of silica mat leads to destruction of the cohesion between particles and bricks become brittle.
3. Lime: (Types of Bricks)
A small quantity of lime is desirable to reduce the shrinkage in brick and brick will be denser but excess of lime deform the shape of brick. If lime is present in form of lumps after burning the brick unsoundness will takes place.
4. Oxides of Iron: (Types of Bricks)
Small quantity of oxide of iron of 5 to 6% imparts reddish brown color. It also helps in using lime and silica. Excess of iron can lead the bricks to dark blue or blackish.
5. Magnesia: (Types of Bricks)
Less than 1% of magnesia is provided in brick and it imparts yellow tint to brick and decreases shrinkage. Excess magnesia leads to decay of brick.
Properties and Tests of Bricks
- The brick should have uniform color, homogeneous, compact and sharp edges.
- The weight of one brick should be in the range of 3 to 3.5kg and the bulk density of brick work is 1800 kg/ m³.
- The dimension of brick should be as per standard
- Standard Size (Modular size): 19cm x 9cm x 9cm
- Modular size with mortar: 20cm x 10cm x 10cm
- Conventional size: 23cm x 11.4cm x 7.6cm
- Brick should not break when it is dropped over a flat surface from height of 1m.
- As per IS 1077 brick is classified as per its strength and minimum strength of brick should not be less than 3.5 MPa when placed in compression testing machine.
- There should be no any sign of scratch over the brick surface when it is scratched by finger nail.
- The brick should produce clear ringing sound when stuck with each other.
- There should be no any patches or stain over the surface of brick after soaking it in water for 24hrs.
- Broken brick should show a bright homogeneous and compact structure which is free from voids.
- The 1st class brick should not absorb more than 20% water by weight when it is immersed in water tank for 24hrs.
- This is valid up to 12.5 MPa strength. For higher strength, it should not be greater than 15%.
Manufacturing Process of Bricks
1. Preparation of clay
The preparation of clay involves following operations-
- Unsoiling: Top Layer of 20cm depth of soil is removed.
- Digging: Clay dug out from ground and spread on ground about 60cm to 120cm heaps.
- Cleaning: Stones, pebbles, vegetable matters are removed and converted into powder form.
- Weathering: Soil is exposed to weather (approximately 6 months), soil become soft, allowable, ripen.
- Blending: Clay is loosen up and ingredients which are needed to be added in it are spread at top. Turning of soil is done to properly mix the ingredients.
- Tempering: Water is added in clay and whole mass is kneaded and it is done in pug mill.
2. Moulding
Desired shape and size is given to the brick with the help of moulds. In moulding a frog is made over the surface of brick of depth 10mm to 20mm, it helps in providing proper adhesion between layers by acting as a key, also helps in printing the name of the trader.
There Are Two Types Of Moulding: –
A) Hand Moulding
- Moulds are rectangular boxes made up of wood or steel, which are open from top and bottom. Steel moulds are more durable and is used for manufacturing bricks on large scale
It is further divided into two types: –
- Ground moulding: Ground is made level and fine sand is sprinkled over it, mould immersed in water and placed on ground to fill the clay. Extra clay is removed with the help of wooden or metal strike after the mould is completely filled.
- Table moulding: Process of moulding is similar to ground moulding done on a table of size 2m x 1m.
B) Machine Moulding
- This method is economical when huge quantity of bricks are to be manufactured.
- It is also divided into two types: –
- Plastic clay moulding: They contain rectangular openings of size equal to brick and clay is placed in machine and when it comes out through opening it is cut into strips by wire fixed.
- Dry clay moulding: In this method of moulding, clay is converted in powdered form an then water is added and plastic paste is formed. Then paste is placed in machine mould and hard well shaped brick is formed.
3. Drying
The brick is exposed to atmosphere after moulding for gradual drying. Moisture content is reduced upto 2% by drying.
4. Burning
It is most important process of manufacturing of brick. It imparts hardness, strength to the bricks. Burning of bricks can be undertaken in clamps or in kilns.
- Clamps are temporary structure and they are used when manufacturing is done at small scale
- Kilns are permanent structure and are used when manufacturing of bricks are done at large scale.
CLAMP : –
- It is of trapezoidal in shape in plan with longer length raised at an angle of 15 degree.
- A wall of brick is constructed in shorter side of clamp and layers of 70cm to 80cm thick, fuel is laid on the floor of the clamp.
- In one layer 4 to 5 course of bricks are laid on their edges and for circulation of air, small spaces between them.
- Then another level of fuel is provided and over it next level of bricks are placed and total height is about 3m to 4m.
- After constructing clamp it is plastered with mud to prevent the removal of heat.
- Period of burning of bricks in clamp is one to two month and same for cooling also.
Advantages:
- Bricks burnt in clamps are tougher and stronger due to gradual burning and cooling.
- It is cheap and economical.
- Skilled labour and supervision for its construction is not required.
Disadvantages:
- Bricks are not of required shape.
- Burning in clamp is very slow process
- Quality of brick is not uniform.
KILNS : –
- It is of large oven type structure used to burn bricks.
- Capacity of kiln is much higher than clamps; average of 25000 bricks per day can be prepared.
- Quality of brick achieved is 90%.
- It is of two types:
1. Intermittent Kilns: (These are non continuous kiln)
A) Intermittent up draught kilns
It is rectangular in shape with thick outside wall, doors are at end for loading and unloading. A temporary roof is provided in kiln to protect it from rain and is removed after kiln is fired. Flames or hot gases are provided by flues. Bricks prepared in intermittent up drought are good in quality than clamp brick but burning is not uniform. Brick supply is also not continuous leads to wastage of fuel.
B) Intermittent down draught kilns
It can be rectangular or circular in shape; their walls are permanent with tight closed roof. A chimney is connected to the floor of kiln. Working is same as in up draught but the difference is that in this kiln gases are carried by chimney connected to floor level. Bricks are evenly burnt and its function is better than up draught kiln. It is suitable for structural clay tiles because heat can be controlled.
2. Continuous Kiln: (They are continuous in operation)
A) Bull’s trench kiln
It may be circular, rectangular or oval in plan. It is constructed fully under ground or partially in ground. Dampers are provided to separate kiln in suitable points. It is most widely used in India. Flues formed from the arrangement of bricks. Fuel in flues is burnt through holes provided in flue with the arrangement to prevent the escape of heat. Generally two chimneys are provided and hot gases leaving from chimney warn the brick in next point. One day is required to burn.
B) Hoffman’s kiln
They are constructed over ground and circular in shape in plan provided with numbers of chambers. Permanent roof is provided to avoid adverse effect of monsoon but initial cost is high. Quality of bricks are good and heat regulation is possible.
C) Tunnel kiln
It is constructed in form of tunnel. Raw bricks kept in trolley at one end to other end. They are economical when manufacturing is done at huge level. Uniform bricks of good quality are produced because temperature is controlled.
Types of Bricks and their Application
1. Types of bricks on the basis of burning
A) Unburnt or Sundried brick
They are dried with the heat received by sun after moulding. They are used at cheap and temporary structure and cannot be used where heavy rainfall occur.
B) Burnt brick
They are burnt in clamp or kiln and are classified in following categories:
- First class brick: They are table moulded and have standard shape and smooth surface and sharp edges. They are used in superior works of permanent structure.
- Second class brick: They are ground moulded and kiln burnt brick. Surface is slightly rough and edges are slightly irregular. They are used where plaster coating are provided over brick work.
- Third class brick: They are moulded in ground and burnt in clamp. They are not hard and their surfaces are rough with distorted edges. They are used at place which is of less important, temporary structures and where rainfall is less.
- Fourth class brick: They are over burnt brick, irregular shape and dark colour. They are used in foundation, floors, roads because they are over burnt so sometime they show strength higher than first class brick.
2. Types of bricks on the basis of Special Purpose
They are formed to meet the ornamental decoration of the structure.
A) Bull Nosed brick
They have round edge at one side and used where sharp edge is not required.
B) Perforated brick
In this brick huge number of perforates are provided along its thickness. They are easily burnt and light in weight. They are used for non load bearing walls, partition walls.
C) Hollow brick
One or more cavities are provided in this brick. They are also light weighted and used where insulation is required against heat.
D) Circular brick
Both the faces of brick are curved of particular radius to meet the required demand. Used for wells and towers.
3. Grading of bricks based on IS 1077: 1992 code specification
- According to IS code, Bricks with compressive strength not less than 140kg/cm2 –Grade A-A class.
- Bricks having compressive strength more than 105kg/cm2 – First class bricks – Grade A.
- Bricks having compressive strength not less than 70kg/cm2 –Second class bricks – Grade B.
- Bricks with compressive strength should not less than the average value in any case 35 kg/ cm2 – class III bricks – Grade C.
Image Source :- freepik,