Rotary Screw Compressor: Definition, Types, Working, Diagram, Applications, Advantages & Disadvantages
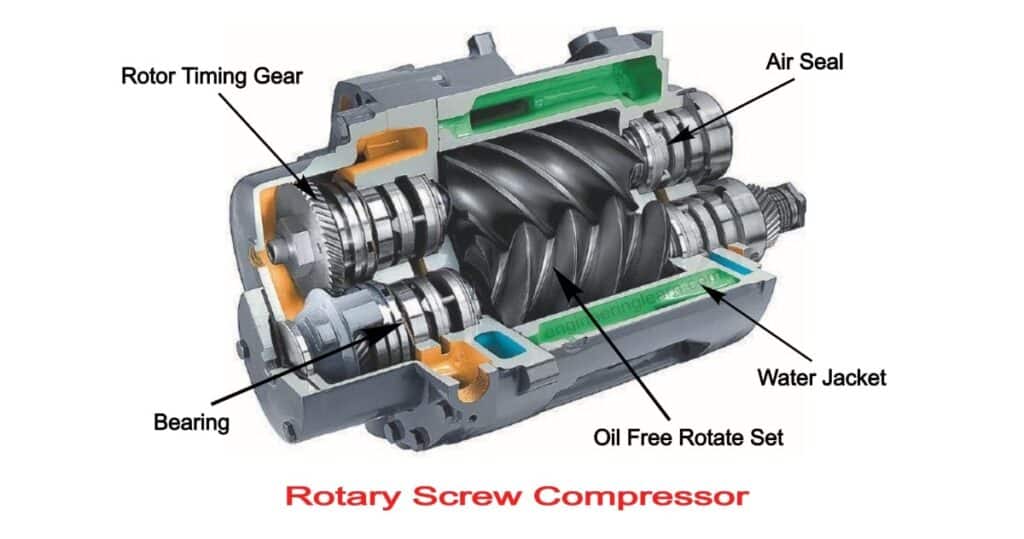
What is Rotary Screw Compressor?
Rotary Screw Compressor: Definition, Types, Working, Diagram, Application, Advantages & Disadvantages :- A screw compressor is a type of rotary compressor that uses the screw motion to compress fluids, generally air. The key benefit of employing this compressor is that it can constantly compress air with little variation in delivery pressure. It’s often used in low-pressure applications up to 8-10 bar. A certain amount of air or oil is trapped in a compression chamber, which is the area between the two-mating rotor, and the area it fills is mechanically reduced, resulting in a pressure rise prior to discharge. ( Types of Air Compressor )
Working of Rotary Screw Compressor
One of the shafts in a screw compressor is the driving shaft, while the other is the driven shaft. Timing gears connect the driving and driven shafts, allowing the speeds of both shafts to be matched. In most cases, an electric motor drives the driving shaft. An airtight shell surrounds the two shafts.
The working of a screw compressor mainly has three phases;
- Suction: – Air is sucked through the inlet opening as the rotors rotate, filling the space between the male lobe and the female flute. The air is transported beyond the suction port and sealed in the gap between the lobe and flute as the rotor continues to rotate.
- Compression: – The air trapped in the interlobe area is moved both axially as well as radially while the main rotor rotates. The air is compressed due to direct volume decrease as the lobes enmeshed, reducing the flute volume and causing compression.
- Delivery: – Compression stops at a defined point where the flute’s leading edge and the delivery port’s edge meet, and air is discharged into the delivery line until the flute volume is reduced to zero.
Construction of Rotary Screw Compressor
- It’s a positive displacement compressor that works by meshing two helically grooved rotors that are contained in a cylinder with inlet and discharge ports.
- The male rotor (driving rotor) has a sequence of lobes (typically four) running the length of the rotor that mesh with similarly shaped helical flutes (usually four to six) on the female (driven rotor) rotor, leaving only a small gap between them.
- As the entrapped fluid flows through the narrowing passageways formed by the lobes, it is gradually squeezed.
- The compressor’s inlet and exit flow are neither radial nor axial, but oblique. This is because of the angle of the meshing lobes and flutes with the longitudinal axis of the shaft carrying the rotors.
- The casing is ribbed for added robustness and is composed of high-grade cast iron.
- Rotors are made of regular carbon steel and must balance dynamically after cutting.
- Within the compressor, sleeve bearings serve as shaft seals.
Types of Rotary Screw Compressor
1. Twin Screw Type
The male rotor with lubes and female rotor with flutes, revolve in opposite directions while the volume between them and the housing getting reduced continuously, are the essential components of the twin-screw element. Each screw element has a set, built-in pressure ratio that is determined by its length, screw pitch, and discharge port shape. The build-in pressure ratio must be adjusted to the appropriate working pressure to achieve optimal efficiency.
There are no valves on a twin-screw compressor, and there are no mechanical forces that create unbalance. This implies it can operate at a high shaft speed while maintaining a high flow rate in a tiny package. The bearings must overcome an axial acting force that is dependent on the pressure difference between the inlet and outlet.
2. Oil Free Type
The original twin screw compressors had an asymmetric rotor shape and no cooling liquid in the compression chamber. Oil-free or dry screw compressors were the name for these. Asymmetric screw profiles in modern, high-speed, oil-free screw compressors result in greatly enhanced energy efficiency due to reduced internal leakage. The most common method of synchronizing the position of the counter-rotating rotors is to use external gears. There is no need for lubrication inside the compression chamber because the rotors do not come into contact with each other or the compressor housing. As a result, the compressed air is absolutely devoid of oil.
3. Liquid Injection Type
A liquid is injected into the compression chamber and frequently into the compressor bearings in liquid-injected screw compressors. Its goal is to cool and lubricate the compressor element’s moving parts, cool compressed air internally, and reduce return leakage to the inlet. Because of its outstanding lubricating and sealing properties, oil is the most commonly injected liquid nowadays, but other liquids, such as water or polymers, are also used. High-pressure ratio liquid-injected screw compressor elements can be constructed, with one compression stage typically sufficing for pressures up to 14 bar or even 17 bar, but at the penalty of reduced energy efficiency.
Application of Rotary Screw Compressor
- Capacity ranges from 200 to 20000 m3/hr.
- Pressure ratio: less than 3 bar in one stage, 12 to 14 bar in the next.
- Used for industrial refrigeration processes.
Advantages of Rotary Screw Compressor
- The screw compressor combines many of the advantages of both centrifugal and compressors, as well as some unique qualities. It uses high-pressure refrigerants like R-22 and ammonia since it is a positive displacement machine. It can handle a large volume because it is a high-speed rotary machine. As a result, it is particularly well suited to large-capacity low-temperature applications, such as food refrigeration.
- It doesn’t have the same surging issues as reciprocating compressors. Due to the usage of high-pressure refrigerants, it has tiny pipe diameters and positive pressures. It features great compression efficiency, continuous capacity control, unloaded beginning, and no balancing issues, just as centrifugal compressors. The compressor can also be used in large-capacity installations.
- Low maintenance
- Long life cycle
Disadvantages of Rotary Screw Compressor
- When unloaded, it can utilize 40 percent to 90 percent of its full load power.
- It’s not a good idea to use it for very small or extremely huge loads.
Image Source :- machinerylubrication