Centrifugal Compressor: Definition, Types, Working Principle, Components, Applications, Advantages & Disadvantages
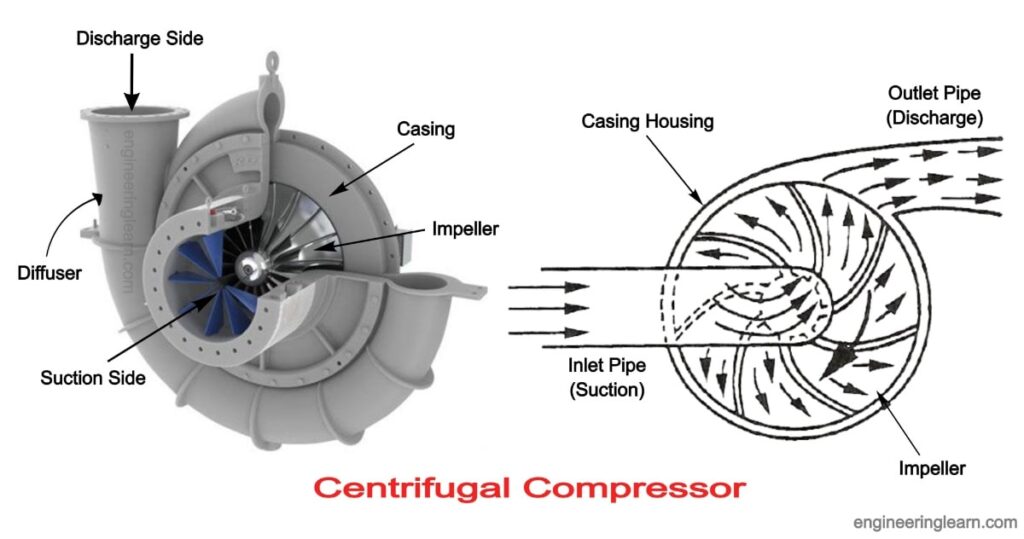
What is Centrifugal Compressor?
Centrifugal Compressor: Definition, Types, Working Principle, Components, Applications, Advantages & Disadvantages :- A centrifugal compressor is basically a radial flow rotodynamic fluid machine that primarily uses air as the working fluid and increases the total internal energy of the fluid inside by using mechanical energy (transferred to the machine from an outside source), typically in the form of increased static pressure head. ( Types of Air Compressor )
Significance of Centrifugal Compressor
During the times of World War II, almost all the gas turbine units were using centrifugal compressors. This is because attention was focused on making simple and lightweight turbojet units as lower weight of power-plants was of significant importance. Post war, however, axial compressors have been manufactured and developed to such an extent where they have significantly higher isentropic efficiency.
Even though today centrifugal compressors are not as popular as back in those days, renewed interest has developed in the centrifugal stage used in conjunction with single or multiple axial stages, especially for small turbofan and turboprop aircraft engines.
Characteristic Features of Centrifugal Compressor
- It occupies much smaller space than an axial flow compressor of equivalent specifications.
- It provides much better resistance to damages from foreign objects.
- Due to having comparatively short length of passage, loss of performance due to buildup deposits on blade surfaces is lesser than the axial flow compressors.
- Compared to an axial flow compressor, it can work reasonably well in contaminated environments.
- It carries the ability to function over a wide range of mass flow rates at a particular rotational speed.
- Its efficiency is, under the most favorable circumstances, lesser than that of axial compressors designed for similar work by 3% or 4 %.
- However, the axial flow compressor efficiency drop sat very low mass flow rate.
- Blading is relatively smaller and thus the advantage appears to lie in the hands of the centrifugal compressor due to its relative simplicity and cost.
Working of Centrifugal Compressor
- After the start-up, gas or air is introduced from the air tank or any other source into the centrifugal compressor.
- After entering the compressor, the air strikes the impeller, which contains multiple radial blades rotating with the rotation of the impeller.
- As the air strikes the impeller blades, the air pushes to the centre of the impeller by centrifugal force.
- The impeller blades, after striking of air provide kinetic energy to the air which increases the velocity of the air.
- The air enters into the diffuser area after passing through the impeller. This diffuser contains multiple stationary vanes. As soon as the air enters the diffuser area, its speed or velocity of flow of the air starts to decrease.
- Now, according to Bernoulli’s principle, the velocity square is inversely proportional to pressure. The diffuser converts this increased velocity of the air into pressure energy before the air is drawn into the centre of impeller. This increase in the impeller’s pressure under most conditions will be roughly equal to the increase in diffuser pressure.
Principle of a Centrifugal Compressor
When fluid or air passes through the rotating impeller of the compressor, it experiences a certain force or work performed by centrifugal forces. This work input increases the pressure and velocity or speed of the air flow through the impeller. The flowing air loses its velocity as soon as it enters the diffuser section. This diffuser is however, a fixed or static component which serves the purpose of the air flow when it exist the impeller. Due to this loss in velocity, an additional increase of pressure is attained. The impeller and the diffuser exclusively supply about 65% and 35% of the total pressure each generated by the compressor.
Components of Centrifugal Compressor
A centrifugal compressor generally made up of four main components – impeller, inlet, collector and diffuser .
1. Impellers
The impellers are mounted on a steel shaft inside the compressor and this assembly is known as compressor rotor. The function of rotor is to provide velocity to the gas through blades that are attached to a rotating disc. Depending upon the desired output, these blades can be either forward-leaning, radial or backward-leaning. Since backward-leaning blades provide the widest range of efficiency, most of the multistage compressors use them.
2. Casing and Inlet
All the components of the compressor are generally protected or guarded by a casing or housing. A case consists of multiple numbers of bearings which provide radial and axial support to the rotor. It also contain multiple nozzles along with all the inlets and discharge flow connections in order to introduce and extract flow from the compressor. This protective case is generally manufactured out of cast iron or steel. Casing is of two types:
- Horizontally split
- Vertically split
3. Collector
At the last stage impeller, the gas is then collected and delivered to the discharge flange. The part employed to gather the gas discharged through the diffuser is called as collector. The collector also contains certain valves and other instrumentation which serve the purpose of controlling the compressor.
4. Diffuser
The impeller removes the gas at high velocity into a diffuser passage, which are small space between adjacent diaphragms that normally changes the flow of gas flow 180° in order to guide it towards the next impeller. The diffuser is usually made up of two walls which create a radial channel. Due to this arrangement, the velocity of the gas decreases and its dynamic pressure is then converted into static pressure. The diffuser passages.
Types of Centrifugal Compressor
There are two types of centrifugal compressors;
1. Single Stage Compressor
Single-stage compressors consist of only one single impeller which is used for moving the air or any other gases up to a 3:1 compression ratio either for pressure or vacuum duty. Single-stage compressors have either a beam design or an overhung impeller type arrangement in which the impeller is situated at the non-driving end of the shaft. The principle benefit that single-stage compressors have over multistage compressors is that they offer higher efficiency and the gas delivered at the end is entirely oil and surge-free.
2. Multi Stage Compressor
Instead of one, multistage compressors consist of two to ten impellers which can be arranged in a variety of flow path configurations according to desired outputs requirements. The temperature and the compression ratio are assumed to be constant throughout each and every stage. These compressors can be arranged in a variety of configurations such as straight-through, compound, and double flow configurations. Multistage compressors are also available in beam-type designs. However their impellers are located between the radial bearings of compressor.
Applications of Centrifugal Compressor
1. Food Industry
Since can provide oil free compressed air, food processing industry depends very much on this type of compressor as oil free compressed air are necessary for some sensitive petitions.
2. Gas Turbines
Gas turbines may either use both axial and centrifugal compressor to get the necessary compression for certain requirements. Centrifugal compressors are typically used in gas turbines like :-
- Turbo shaft
- Turboprop
- Micro turbines and
- Auxiliary power units
3. Compressed Gas or Air
Compressed gas or air to obtain or produce compressed air, a centrifugal compressor is one of the most simple and efficient piece of equipment and are the best choice when constant and excessive air or gas is required.
4. Refrigeration and Air Control
Since they support a wide variety of refrigerants and thermodynamics and are also able to supply compression in water chiller cycles, they have high demands for utilization in refrigerators and air conditioners.
5. Oil Refiners, Petrochemical and Chemical Plants
Generally a horizontally split casing centrifugal compressor is used for the above purposes and most of these are multistage compressors. These types of compressors are usually operated by huge steam engines and gas turbines.
Advantages of Centrifugal Compressor
- They are relatively agile and easy to manufacturer as compared to other compressors.
- Since they do not require any special type of foundation, centrifugal compressors are highly energy efficient and reliable.
- They consist of only a few rubbing parts and are completely oil free.
- They generate higher pressure ratio per stage compared to the axial flow compressor.
Disadvantages of Centrifugal Compressor
- They can only produce a limited amount of pressure and are cannot be relied upon for very high compression.
- Due to their operation on higher speeds, they require a steady and sturdy mounting.
- Stalling and choking are some of the frequently occurring problems.
Image Source :- petrolessons, globalspec