Rope Drive: Types, Application, Construction, Advantages & Disadvantages [Complete Guide]
![Rope Drive: Types, Application, Construction, Advantages & Disadvantages [Complete Guide]](https://engineeringlearn.com/wp-content/uploads/2021/12/Rope-Drive-1024x539.jpg)
Introduction
Rope Drive: Types, Application, Construction, Advantages & Disadvantages [Complete Guide] :- Rope drive is referred to as a simplified form of a belt drive, which is most commonly found having the application of power transmission mechanically. Rope drives are found performing multiple use of circular section ropes instead of the single flats or V-belts. The rope drives are the ones which are widely used where ever there seems to be a large amount of power that needs to be transmitted, from one pulley to another for any particular considerable distance.
It can be noted that the use of belts like flat belts is found to be limited for the purpose of transmission of any medium power considered from one pulley to any another wherever the two pulleys are found not exceeding the distance of minimum 8 m. If there is any large amount of power is found being then it can be transmitted by the flat belt which can result in an excessive belt cross-section.
The ropes which are used for the purpose of transmitting power are the ones which are usually made from the fibrous materials like hemp, manila and cotton.
Types of Rope Drive
The ropes drive is found using these two types of ropes:
- Wire ropes.
- Fibre ropes.
The fibre ropes are referred to as those ropes which are usually found being operated successfully when the pulleys are found being approximately 60 meters apart from each other, whereas the wire ropes are found being used at the time when the pulleys are separated by 150 meters.
1. Wire Rope
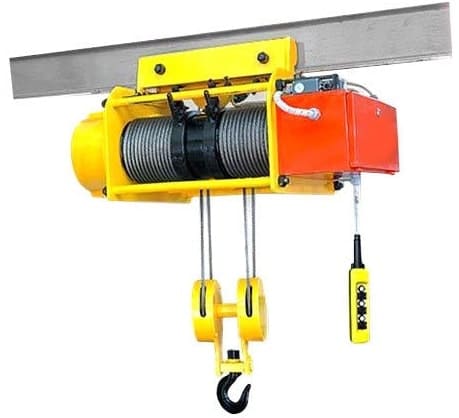
Wire rope is referred to as that rope which is found having several strands of metal wire twisted into a helix which forms a composite rope, in terms of the pattern which is commonly known to be the laid rope. Larger diameter of wire rope is found consisting of multiple strands of such laid ropes in a pattern which is commonly known as cable laid.
Commonly talking about the lifting as well as the rigging industries, wire rope is found being attached to a crane or hoist which is then fitted along with the swivels, shackles or hooks in order to attach to any load which moves it in a controlled matter. These types of ropes are very commonly used in order to lift or to lower the elevators in terms of the support for the suspension bridges or the towers.
Wire rope is commonly preferred for the purpose of lifting the devices for various types of requirements. The unique shapes of such type of rope is found consisting of multiple steel wires that is usually found forming individual strands which are easily laid in a helical pattern around a core. This structure is responsible for providing strength, flexibility, as well as the ability to handle bending stresses in such ropes.
In the technical world the wire rope is referred to as that which is found having a larger diameter as compared to any other with some smaller gauges that are known to be the designated cable or cords. Wrought iron wires are termed as those which were used in the ancient era, but today steel is known as the main material which is used for the wire ropes.
Material of Wire Rope
Wire ropes are usually referred to be made from various types of cold-drawn wires which is responsible for increasing the strength as well as the durability of the wire rope. The best thing to observe in wire rope is that, its size decreases, the strength of the wire rope increases which means that it has an inverse relation. There seem to be numerous materials which are found being used for the wire ropes to let it increase its strength using the materials like iron, cast steel, strong cast steel, steel, as well as alloy steel.
For some of these purposes, a wire rope is found being made up of copper, bronze, aluminium alloys, and stainless steel. The wire ropes are most commonly found being developed which starts with the mining hoist applications in the early 1830s. The wire ropes are found being used dynamically for the purpose of either lifting or hoisting in cranes and elevators, and for the transmission purposes of the mechanical power too.
The main aim of the wire rope is to transmit force in the mechanisms, like a Bowden cable or the control surfaces of an airplane which is found to be connected to the levers as well as pedals of the cockpit.
Clamp For Wire Rope
A wire rope clip is referred to as a u-bolt clamp or a u-bolt clip which is used in order to clamp the loose end of a length of wire rope as soon as it has been looped back in order to form an eye. These fittings consist of a u-bolt which has a saddle that are secured by two nuts.
Commonly, the wire rope assemblies are known to be the ones which are found having a need to at least two or three wire rope clips to let secure the ends properly along with the length of the rope.
Construction of Wire Rope
Wire ropes are usually found being made from different grades of the steel wire having the tensile strength which can range from 1200 to 2400 MPa. The wires are initially found giving special heat treatment after which the cold is drawn for higher strength as well as durability of the rope. Steel wire ropes are found being manufactured by the specialized machines.
Construction of Wire Rope Drive
The core of the wire is found being made up of hemp, jute, asbestos, or soft steel wire. The core needs to be continuously saturated along with the lubricant for a better life of the core as well as the entire rope.
Asbestos or the soft wire cores are the ones which are usually used whenever the ropes are found being subjected to radiant heat like the cranes which are found working near the furnaces. Whereas, a wire core is found reducing the flexibility of the rope, and such ropes are the ones which are used only wherever they are subjected to high compressions, in case of wounding of multiple layers on a rope drum.
Advantages of Wire Rope
The advantages of a wire rope are that they are most commonly found to be more resistant to wear as they are found having better crushing resistance along with higher strength as compared to a round strand wire rope of equal diameter as well as classification. Whereas, a swaged wire rope is referred to as the one which might have less bending fatigue resistance.
The wire ropes are found having following advantages as compared to the fibre ropes:
- High flexibility and Wear resistance.
- Better crushing resistance.
- Higher strength as compared to round strand.
- Less resistance of the bending fatigue.
- Reduction of mechanical stress on the rope as well as the sheave
- Less damages
- Significant Cost Reduction.
Procedure For Designing A Wire Rope
The procedure for designing a wire rope is as follows:
- First, there is a need to select an appropriate type of rope for the given application.
- You must design load by assuming a safety factor within 2 to 2.5 times the safety factor.
- Determine the diameter of the wire rope (D) by equalizing the tensile strength of the rope for the design load.
- Determine the diameter of the wire and the area of the rope.
- Locate the stresses or loads in the rope.
- Determine the effective stress or load during normal functioning.
- Find its real safety factor and compare it with the safety factor.
- If safety factor is within the permitted range then only the design can be stated as protected.
Classification of Wire Rope
According to the direction of twist of any particular individual wire and strands which are found being related to each other, the wire ropes can thus be classified as follows:
1. Cross or Regular Laying Ropes
Cross or Regular Laying Ropes are referred to as those types of ropes wherein the direction of twisting of wires inside the strides is found being opposite as compared to the direction of the twist of the stand. These types of ropes are the ones which are found being most commonly used.
2. Parallel or Lang Lay Ropes
Parallel or lang lay ropes are referred to as those ropes which are found in the direction of rotation of the strands in the strands and is found similar to the strands in the rope. These ropes are found having a better bearing surface whereas these are easily split and are thus twisted when loaded. These ropes are known to be more flexible and effective as compared to any other type. Since these ropes are found having the tendency to rotate, they are most commonly used in the lifts and are waved by the guide methods and also as per the ropes.
3. Composite or Reverse Laid Ropes
Composite or reverse laid ropes are referred to as those types of ropes wherein the wires in two adjacent strands are found being rotated in the opposite directions.
The direction of the laying of ropes can either be right-handed or left-handed which depends upon the strands formed either right-handedly or left-handedly helix. But the right-handed ropes are most commonly used.
2. Fibre Rope
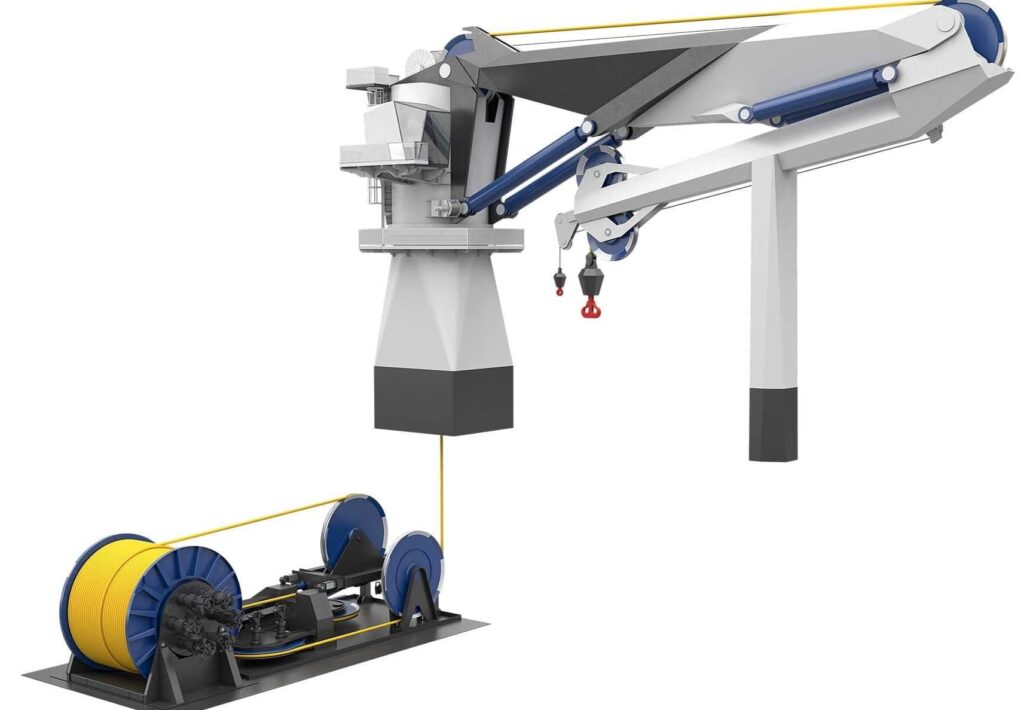
Fibre ropes are referred to as those ropes which are found being made from fibres of varying length that is also found being dependent on their source. These are the ones which are found being known to be made up of the twisted up rope from the yarns, wherein the twist is responsible for binding the fibres firmly together so that it can hold the friction whenever the yarn is subjected to undergo any kind of strain.
Ropes for transmission power are usually found being made up of fibrous materials like cannabis, manila, cotton etc. Since hemp and manila fibres are found to be rough, the ropes are found being made up of these fibres which are not very flexible and have poor mechanical properties too. The hemp rope is found having less strength as compared to the Manila ropes.
Once the hemp along with the manila ropes are observed to be bent over the sheave, the fibres might undergo some sliding that in result tends to cause the rope to rub internally. So, in order to reduce this defect, the rope fibres are found being lubricated with a tar, elongated, or graphite. Lubrication is also responsible for making the rope moisture-proof.
Application of Rope Drive
Rope drive is found having various applications which can be used for several purposes like hunting, pulling, carrying purposes, lifting purposes, as well as climbing activities in the ancient era.
Power transmission over long distances is found to be the main application of a rope drive. Rope drives are usually found being used in order to drive the systems that are usually found to be more than 8 meters in distance along with using a distance power transmission system. Metal ropes are the ones which are found being used for all the distances beyond 60 meters. These types of ropes are found to be seen commonly in the elevators as well as the cranes.
Advantages of Fibre Rope Drive
The fibre rope drives are found having various advantages which are hereby mentioned:
- Smooth, steady, and quiet.
- Gets affected by the external conditions.
- Shafts needs to be aligned.
- High mechanical efficiency.
Advantages of Rope Drive
- Appreciable power transmission.
- Used for long-distance power transitions.
- Strong and flexible ropes.
- Smooth and noise resistant.
- Runs in any direction.
- Low-cost and economical.
- Precise alignment of the shaft is not needed.
Disadvantage of Rope Drive
- Failure of rope does not have any sign, so it often gets unnoticed.
- Wire rope gets corroded.
Image Source :- codecogs, wirestrander, kongsberg