Pneumatic Control System: Definition, Components, Working Principle, Advantages & Disadvantages
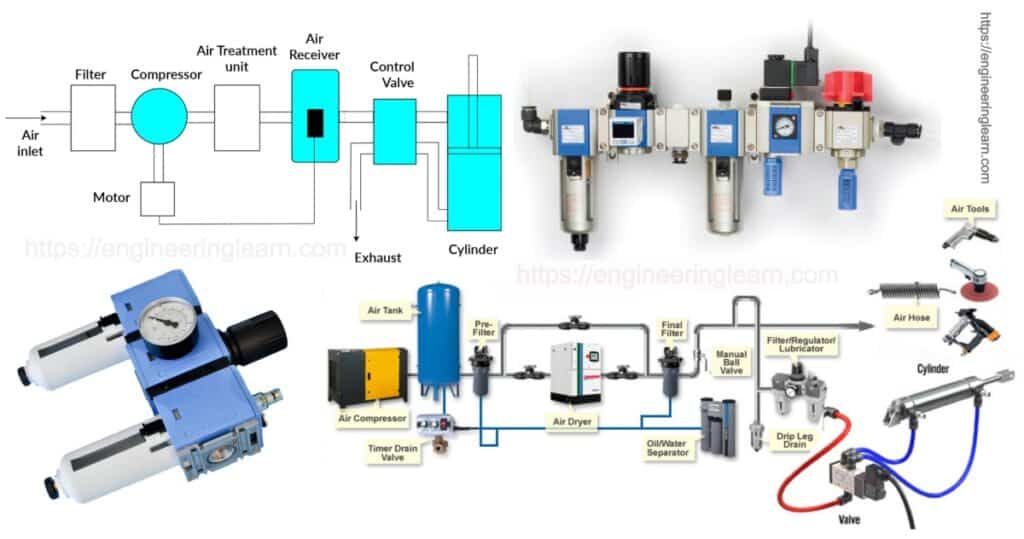
Introduction
Pneumatic Control System: Definition, Components, Working Principle, Advantages & Disadvantages :- The pneumatic control system is the same as hydraulic system in many ways. Also many components are same in both the systems. The basic difference between these two systems is that pneumatic system works on air or gases whereas the hydraulic system works on oil or liquid. To get output work in a pneumatic system we use compressed air.
Pneumatic System Components
1. Air filter
The air used in this system directly come from the atmosphere. The function of air filter is to purify the air. It removes dust particles and contaminants from the air.
2. Air compressor
The function of air compressor is to compress the air. It decreases the volume of the air and increases the pressure of the air.
3. Electric motor
It supply power to the compressor in the form of mechanical energy. Or we can say that, the electric motor converts electrical energy into mechanical energy which drives the compressor.
4. Air coolers
It is same as the condenser. When the air is compressed by the compressor, its pressure increases and temperature also increases. To reduce the temperature air coolers are used.
5. Receiver tanks
The function of receiver tank is to store the cool compressed air coming from the air coolers.
6. Filter Regulator Lubricator (F.R.L)
F.R.L means Filter Regulator Lubricator. The function of this component is to filter foreign particles/dust particles from the air and give out clean air. Next it works to provide a fixed pressure to the air and lastly it lubricates the air so that the pneumatic system can properly function.
7. Control valve
The function of a control valve is to regulate the direction of flow of air, air pressure etc.
8. Air actuator
The most important part of a pneumatic system is the air actuator. Its function is to use the energy of the compressed air(also called pressure energy) and convert it into mechanical energy. Thus we get the final output or work from the air actuator.
Pneumatic System Working Principle
- Firstly the air is directly taken from the atmosphere and sent to the air filters. The air is purified and cleaned in the air filter for further use. Air filters are crucial because if the air is directly used from the atmosphere than it can damage the compressor which is a very important component of our pneumatic system.
- Next the air is transferred to the air compressor. The air compressor is driven by the mechanical energy generated by the electric motor. The air compressor can be rotary or reciprocating. The compressor increases the pressure of the air and reduces its volume.
- As the pressure of the air is increased, its temperature also increases. This happens because the kinetic energy of air molecules increases after compression. Hence in the next step air is sent to the air coolers which cool down the air and decreases its temperature. However the pressure of compressed air remains the same even after cooling.
- The cool and compressed air is then sent and stored in the receiver tanks. Now this air can be used further as per our requirements.
- The air stored in receiver tanks is then sent to the FRL. The air is lubricated and dried in the FRL. This process is important to be done because the upcoming parts of the pneumatic system are delicate. In case the FRL is not used and the air is sent directly from the receiver tanks then it is possible that some air might be warm and wet. This will have serious impact on the other parts. Hence the FRL is very important in the pneumatic control system in order to ensure its long life and efficiency.
- From the FRL the treated air goes to the control valve. The control valve regulates the direction of flow according to the requirements.
Advantages of Pneumatic System
- The fluid used in pneumatic control system is air which is easy to collect and easy to exhaust. Therefore this system becomes very cheap becauseĀ the used air can beĀ returned back to the atmosphere
- In pneumatics there is no requirement of return tubing. In Hydraulics we need one pipe or tube for carrying the fluid to the place of work namely the load and another pipe or tube to bring it back. This is not necessary for pneumatics as the gas that is used here is air ( which is mostly the case) which can be directly exhausted it to the atmosphere. This way pneumatics helps saving half the tubing cost which is quite a lot.
- Another reason why pneumatics generally turns out to be cheaper than electric actuation or hydraulic actuation is that in pneumatics the cost of the air and handling equipment is actually shared among the applications.
- Another important advantage of Pneumatic Systems is that while electric systems are prone to fire because of electric spark, hydraulic systems uses oil which is inflammable (as it comes from petroleum derivatives); pneumatic systems are intrinsically safe and therefore often preferred in places like explosive environments, natural gas plants etc. This advantage of pneumatic control systems makes them useful at places where there is a hazard of explosion.
- Maintenance of Pneumatic systems is easier. For example, if in a hydraulic system there is an oil leakage (which is often a major maintenance headache) then it will result into economic loss as well as environmental degradation. Whereas in pneumatics if there is a leakage of air then it is only going to cause a loss of pressure and therefore some loss of energy. Hence pneumatic system maintenance need not be so stringent so maintenance cost is low.
Disadvantages of Pneumatic Systems
- Firstly these systems are slower in performance compared to hydraulic.
- Also they have low power handling ratings.
- In terms of sophistication of control they are inferior to electric control.