Forging Press: Definition, Types, Uses, Advantages & Disadvantages [Complete Details]
![Forging Press: Definition, Types, Uses, Advantages & Disadvantages [Complete Details]](https://engineeringlearn.com/wp-content/uploads/2023/04/Forging-Press-1024x539.jpg)
Introduction
Forging Press: Definition, Types, Uses, Advantages & Disadvantages [Complete Details]: – A forging press uses an upward ram to apply consistent, controlled pressure to a die holding a work piece. It is a similar process to drop forging, however, it utilizes slow pressure rather than a series of blows. The slow movement of the ram planet further into the workpiece with the goal that the workpiece undergoes uniform plastic deformation.
Types of Forging Presses
The basic component of forging operations is the ability to produce a lot of force and focus it on a work piece. High-performance forging presses supply a huge amount of force that deforms and plasticizes metals to reach explicit tolerances and shapes utilizing an open or closed die. There are endless strategies that can produce the vital force and are differentiated by the mechanism they utilized. Hydraulic, screw, and upsetters, every one of which produces similar shapes and can forge alloys with moderate ductility that would shatter under the impact of a hammer.
1. Hydraulic Forging Presses
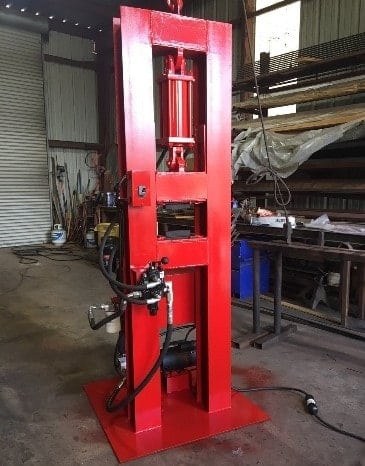
Hydraulic presses create their force through hydraulic pressure from a liquid utilizing Pascal’s law. The force of a small amount is applied to the fluid, which moves a bigger amount of fluid to create the force that further moves the ram to shape the work piece. They work quite slowly than other forging presses and have longer contact with the work piece. Open dies are the ordinary type utilized with a hydraulic die on forging. Dies for hydraulic fogging presses take a lot of abuse as a result of the expanded contact time, which brings down the die’s significant life.
2. Screw Forging Process
A screw press, similar to a hydraulic press, works slowly. A screw is turned by a motor that further pushes the ram down onto the work piece with a pressure that is steady and with a long stroke.
(i) Friction Drive Forging Presses
An upward-mounted drive wheel rotate continually in a friction drive forging press. To make the down-stroke of the ram, the wheels shift to empower one wheel to connect with the flywheel to accelerate the slam. At the point when the supplied energy is utilized, the flywheel, screw, and ram stop. At the stopping point, the drive wheels shift to permit the flywheel to reverse and move the ram to the top.
(ii) Gear Drive Forging Presses
A gear drive forging press has a gear drive and slipping clutch flywheel assembly where the drive gears and screw are shielded from over-burdening by the slipping clutch.
(iii) Direct Electric Drive Forging Presses
A reversible electric engine is incorporated into the screw and frame with a direct electric drive forging press. In comparison with friction drive forging presses, when the flywheel stops, it should be reversed. On account of direct electric drive forging presses, reversing is provided by the electric motor.
3. Mechanical Forging Presses
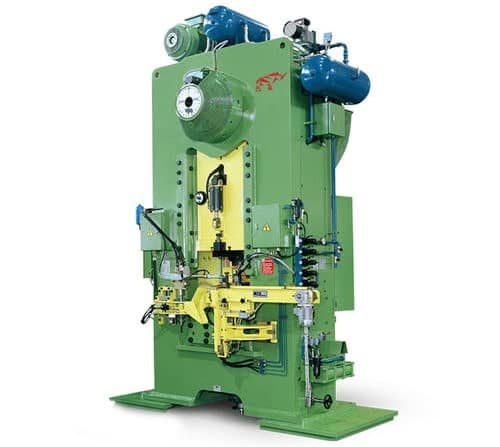
The motor and controller are driven by Mechanical forging presses. It also has a clutch and crankshaft which are equipped for applying a consistent stroke length to the ram. The speed of the slam is most prominent at the center of the stroke, with maximum force accomplished at the very bottom of the stroke. A lot of stress is put on the dies with little impact load in the mechanical forging process. Harder dies are utilized to forestall breakage and damage.
4. Pneumatic Forging Process
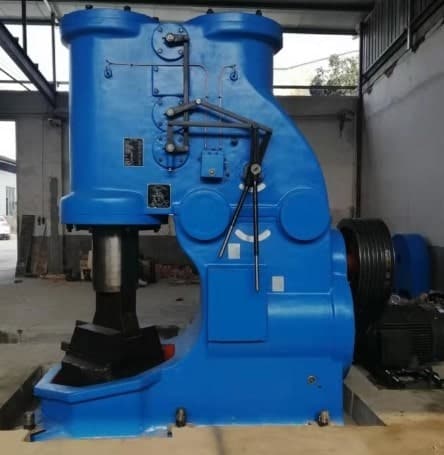
The force of a pneumatic press comes from compressed or compacted air or gas, which is constrained into a cylinder connected to a ram. The pressure from the cylinder forces the downward movement of the ram only when the cylinder is filled precisely. When the air or gas is delivered through a break valve then only slam will be discharged.
5. Servo Forging Process
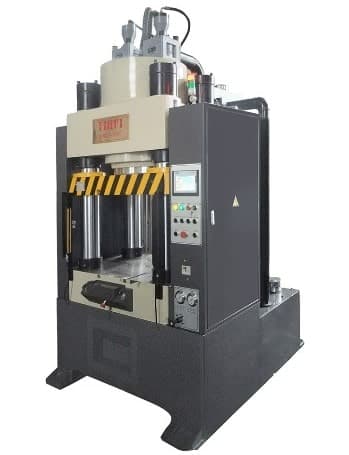
A servo motor or engine that drives an eccentric gear makes slider movement and is basically driven by a servo forging press. The main thrust created or conveyed by the motor is changed into direct development by screws, turning bars, and elbow poles to drive the slider. The stroke, speed, and pressure of the slider are constrained by complex charge. Servo engine forging presses have a primary drive, actuator, and auxiliary mechanism. Servo forging press transmission system transfer energy from servo engine to the actuator that further drives the slider to do the reciprocating movement and the forging process is completed.
6. Upset Forging and Up setters
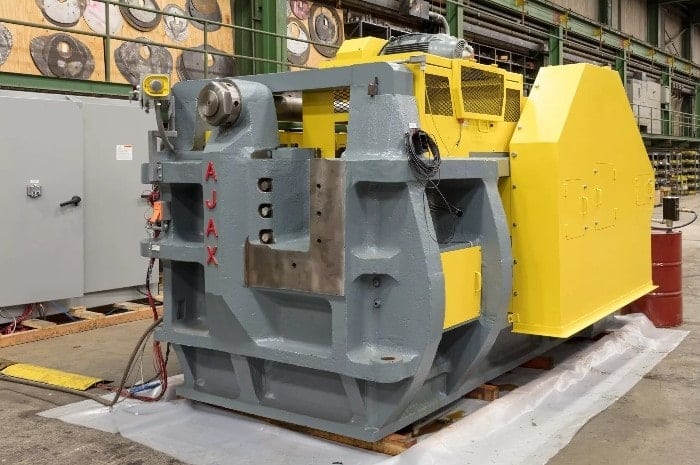
Horizontal forging which utilizes upset forging and up setters and afterwards the machine that moves horizontally utilizing a ram against the work piece. The workpiece is held set up between bite die halves while pressure is applied toward its axis by a heading tool that spreads, or upsets, the end of the workpiece by metal displacement. There is a prerequisite or requirement of two grippers and cavity dies with one being fixed or constant while the other one is fastened or secured to the die slide which is moving and if we talk about the header slide, a puncher is additionally joined.
The movable die slides to the fixed die to grip and hold the workpiece during the upset forging process. The punch or ram pushes forward and forces the workpiece into the die cavities. The movable die is in an open position to release the forging only when the ram punch retracts. The process may be rehashed on different occasions before it is completed.
The metal with holding its integrity and optimizes its grain flow properties only when the workpiece for upset production is preheated. The unbroken grain flow produces metal parts with unrivaled rigidity and strength. Upset forging is alluded to as free forming since the workpiece is decreased in height and structure. It is many times utilized as an immediate process as a feature of a multiple step forging process.
What are Metals Used in Forging Presses?
1. Steel
The heating process makes the steel more ductile and pliant for molding under pressure. A billet of steel can be for all time formed without cracking as a result of its plasticity.
2. Titanium
Titanium has excellent weight-to-strength and strength-to-thickness proportions and corrosion resistance.
3. Aluminum
Aluminum is ideal for forging since it is lightweight and durable.
4. Stainless Steel
Stainless steel is corrosion-resistant, has fantastic strength, and can be forged into different shapes. Stainless steel requires more pressure because of its solidarity.
5. Brass
Brass can be molded into a structure from a couple of ounces to several tons.
6. Magnesium
Magnesium has a low thickness with strength and stiffness that is more prominent than steel or aluminum, yet it costs more and is hard to forge.
7. Copper
Copper bars are heated preceding the forging process. Subsequent to heating, the bars are pressed into the ideal shape. Forged copper has incredible electrical and thermal conductivity.
Advantages of Forging Presses
The Process of a forging press is faster and more affordable than different techniques. Below are some advantages of the Forging Presses: –
A. Strength-to-Weight Ratio
During the process of forging, the grain structure of the piece becomes compacted, which creates diminished stress on the corners and filets growing the strength of the piece.
B. Post Forging Treatments
With the shortfall of voids and porosity, pieces can be machined in the wake of forging without a loss of dimensional exactness or quality.
C. Reduced Defects
Forging diminishes metallurgical deformities, for example, porosity and alloy segregation, which lessens the time for machining the completed piece and a positive response to heat treatment.
D. Cost Savings
The saving factors for forging incorporate raw material utilization, diminished machining time, and recovery die material.
E. Higher Productivity
Forging presses have a broad variety of weights from two or three hundred to a couple thousand with working strokes per minute. Parts are completed in a solitary squeeze, which can be slowed by complex designs.
F. Die Life Span
The quantity of cycles for a die varies relying upon the kinds of materials being shaped, the strength of the material, the requirement for close tolerances, sharp corners, and intricate designs.
G. Produces Complex Designs
Dies in press forging have less draft, which prepares them to produce complex and confounded shapes with amazing layered precision. Forging can create profound bulges, up to different times the thickness of the material.
H. Mechanical Properties
Anisotropic are the parts which are created from forging presses. There are some different properties in navigate and axial on account of grain structure. Press forging works on the versatility of completed pieces making them more ductile.
I. Process Control
The speed, travel distance, and pressure of a press forging die are thus controlled for accuracy and capability.
J. Forging Press Metals
Most metals can be press forged however a few metals are more versatile in the process. The scope of metals incorporates carbon steel, tempered steel, apparatus steel, aluminum, titanium, metal, and copper. Since each metal has its individual strength, and weight, the sort of metal chosen for a process relies upon the necessities of the individual who will utilize the completed piece.
K. Consistency
The parts are made by a controlled and monitored production process, which makes consistency of part and structure as well as varieties which are minimal in machinability and the evacuation of transfer distortion.
Disadvantages of Forging Presses
There are downsides, constraints, and weaknesses to the process.
A. Cost
Cost is one of the factors in regard to press forging. The equipment for the process is extremely large and must be solid to have the option to create the necessary force. Tools and dies for the process must be specially made utilizing a select number of metals.
B. Dies
Forging press dies are costly and hard to make for complicated parts. A unique sort of steel is used to make the dies, which must be heat-treated and have exceptional finishing.
C. Complex Parts
Highly complicated parts and designs can’t be produced utilizing press forging. However parts with complex exterior designs can be manufactured utilizing the process, and parts that have internal cavities and intricacies can’t be forged.
D. Amount of Force
Heaps of Pressure are critical to form a section in a forging press, which requires large and costly equipment.
E. Metals
Press forging is limited by the sorts of metals that can be forged. Cast iron, chromium, and tungsten can’t be press forged on the grounds that they are excessively weak.
F. Size
Just parts of a specific size can be produced by press forging, which eliminates any large designs.
G. Residual Stress
Residual stress happens in metals that must be heated prior to being pressed. In the event that the parts are not cooled as expected, residual stress happens.
H. Defects
However press forging wipes out shrinkage, but there are still distortions that can occur in the outcome of the product, similar to laps, funneling, and die failure.
I. Time Consumption
Press forging gradually applies pressure to the workpiece. The die needs to keep in contact for a lengthy timeframe. The length of this part of the cycle slows down production.
J. Scale Pits
Scale pit happens when the surface which is to be forged has not been cleaned as expected and is common while forging is done in an open environment.
Conclusion
There are a few strategies for creating a force for a forging press, which incorporates mechanical, hydraulic, servo, and pneumatic. The process of a forging press is quicker and more affordable than other production methods. No matter what the wide utilization of press forging is, there are downsides, constraints, and weaknesses to the process. Forging presses are an essential part of the manufacturing processes of a few industries, which incorporate auto, aviation, horticultural gear, oilfield parts, instruments and equipment, and military weapons.
Image Source: – nord-lock, thomasnet, jwrandall, directindustry, anyanghammer, made-in-china, ajaxerie