Vertical Machining Center (VMC): Definition, Components, Uses, Working Principle, Advantages & Disadvantages
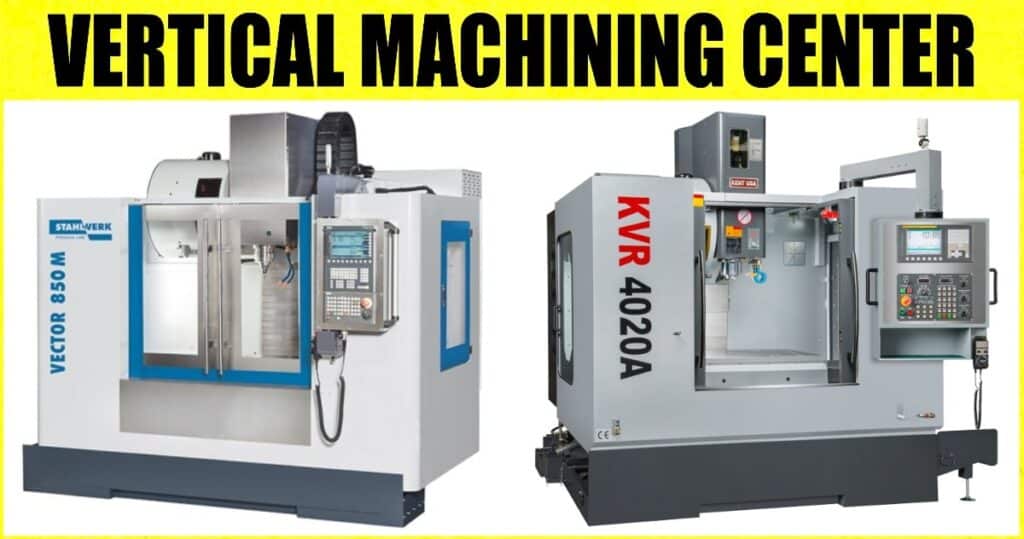
Introduction
Vertical Machining Center: Definition, Components, Uses, Working Principle, Advantages & Disadvantages: – The vertical machining center has existed for quite a while and stays a fundamental part of modern CNC innovation and development. For machining different industrial parts Vertical machining centers are quiet efficient. These machines are versatile and effective. They eliminate layers of material from a substrate to produce the ideal part with different features.
What is Vertical Machining Center?
Vertical machining technological advancement is conceivably perhaps one of the most useful devices in the machine shop. It has different tools in the changer and different options that improve and customized productivity. Vertical Machining centers offer a large number of potential tasks, however that versatility or adaptability accompanies the need to remain flexible and perform effective measurements consistently. It operates in a vertical direction utilizing a spindle that works at a steep angle.
The vertical mill’s computerized or electronic controls permit automation, selection/rotation of tools, repeatability, and contour control. These high-level(advanced) and present-day CNC machines have expanded the efficiency and productivity of the milling machines to the most significant level, bringing about the vertical milling center. These machining centers vary contingent upon their axes, function, and different choices accessible.
You can allude to or insinuate the vertical machine centers as an industrial workhorse since it can deliver parts with amazing precision and more limited lead times. Because of the robust designs of its components hence can deliver superior torque, horsepower, and machining speed. The degree of automation of vertical milling centers similarly allows them to cut various materials and diminish overall manufacturing costs.
Working Principle of Vertical Machining Center
The various machine tools and the parameters required for the parts are transformed into information codes that are by and large acceptable and readable by the numerical control device of the machine.
The processing program assists with handling the component’s CNC program automatically. The disks or punctured are the type of information carriers where most part of instruction codes are stored. tapes Further these carriers are shipped to the input device. You can peruse this information and further transfer it to the numerical control device. Similarly, you can use the computer and the machining center to send information directly to achieve the input and output of the component’s program.
The vertical machining center for the most part has three linear motion coordinates. Worktable is attached with a horizontal axis rotary table. This assists it to fabricate circular Workpieces without any problem.
Components of Vertical Machining Center
The vertical machining center comprises many important components.The components include the following:
1. Rotating Spindle
The Rotating spindle is typically perpendicular/vertical to the working table. For holding a tool or workpiece, rotating spindle is utilized.It is basically a rotating shaft with a unit. For the most part, the spindle shaft goes about as a positioned, support, and rotational drive for Workpieces.
2. Tool Changer
The tool changer increases the efficiency of the vertical machine center by permitting the automatic selection of devices for various tasks ranging from rough cutting to fine-hole boring.
3. Work Table
The table is flat on which you put the workpiece directly or utilize a few fixtures, for example, hard clamping vises or milled aluminum parts. The table has an X-axis which includes the left motion and right motion, while the Y-axis has a motion to the back and front. These axes and the Z-axis permit you to add limitless features to workpieces across the planes of motion.
4. Rotating Tables
Adding additional axes to the vertical mills can significantly enhance efficiency by changing a basic 3-axis processing machine into a 4-axis or 5-axis machine equipped with producing complex components with various surfaces like turbine blades.
5. Enclosures / Full Covers
These covers help to reduce the splatters brought about by the milling operations. Moreover, it safeguards the mechanical engineers and the environment from the machining operation.
6. Coolant System
By using recalculating coolant systems we ensure that part and cutter tools are well lubricated. This coolant system frequently uses water and soluble oil among different fluids.
7. Screw / Chip Conveyor
Chip conveyors or augers can assist with moving chips from the workspace to facilitate productivity and eliminate downtime from manually shoveling waste chips.
8. Quick Loading Loaders
loading systems assists to increase the productivity of the vertical machining centers while diminishing downtime.
Parts and Uses of Vertical Machining Center
Vertical machining centers have a few parts and products for various industries and utilization. Aviation, fabricating industry, hardware developers, and clinical are some of the sectors that uses vertical machining centers because of their high precision or exactness, high accuracy, and volume production applications.
1. Parts with Unusual Shapes
Some Structures have irregular shapes like baskets or base.By far most of these machined parts require multi-point mixed processing of point, line, and face. Vertical machine centers with automatic machining ability to machine these complicated parts that are most of the time hard to make using customary systems.
2. Complex Parts with Plenty of Curves
If we talk about aviation and transportation, some parts like propellers, cams, and impellers with complex curves are standard. Traditional or Conventional machine tools make these parts with curved parts, and box/casting with closed internal cavities challenging to make with the ideal machining accuracy.
In any case, multi-axis vertical machine centers coordinated with CNC machine technology help to produce curved parts with accuracy and precision in an effective way and also time utilized is minimal.
3. Box-Type Part
Box-type parts are common in cars and planes. The engine block, spindle box, gear pump shell, diesel engine block are some of its parts. Also, the vertical machine centers have high precision, proficiency, rigidity, and automatic tool changer. Given the process sequence is all around programmed and you use proper fixes and tools, the difficult issues of box-type parts machining can be resolved.
Advantages of Vertical Machining Center
A) Increased Productivity
One of the greatest benefits of vertical machining centers is that they are significantly more productive than horizontal machining centers. This is on the grounds that vertical machining centers can perform different operations at the same time, like milling, drilling, and tapping.
B) Increased Rigidity
One more benefit of vertical machining centers is that they are substantially more rigid than horizontal machining centers. This is on the grounds that vertical machining centers have a heavier base and more robust construction. Also, vertical machining centers commonly have larger work envelopes as compared to horizontal machining centers, and that infers they can accommodate bigger parts.
C) Increased Accuracy
If we talk about vertical machining centers they are considerably more precise and accurate than horizontal machining centers which is one of its positive aspects in comparison to horizontal machining centers. This is on the grounds that vertical machining centers have a fixed spindle, and that implies that the cutting tool doesn’t move during operation. This reduces vibration and chatter, prompting superior surface completion and increased accuracy.
D) Better Chip Evacuation
In comparison with horizontal machining centers, vertical machining centers have better chip evacuation. This is on the grounds that the chips produced by vertical machining centers fall straight into a chip tray, while the chips produced by horizontal machining centers will more often than not become involved with the workpiece or on the machine table.
Disadvantages of Vertical Machining Center
A) Limited Space
Vertical machining centers are limited as far as how much space they can take up is one of its main drawbacks. This is on the grounds that vertical machining centers normally have a smaller footprint. For Manufacturers with limited space in their facilities can be a big problem for them.
B) Limited Tool Capacity
One more limitation of vertical machining center is that they typically have a smaller tool capacity. This implies producers who utilize vertical machining focuses may have to change apparatuses every now and again than the individuals who utilize level machining focuses. This can prompt expanded personal time and diminished efficiency.
C) Limited Workpiece Size
Another limitation of vertical machining centers is that they are typically limited as far as the workpiece size that they can accommodate. This is on the grounds that vertical machining centers normally have smaller beds. For Manufacturers who need to machine large Workpieces, smaller beds can be a big issue for them.
D) Higher Operating Costs
One more hindrance of vertical machining centers is that they normally have higher operating costs than horizontal machining centers. This is on the grounds that vertical machining centers require more energy to utilize and frequently require unique cooling systems to forestall overheating.
E) Increased Vibration
One more detriment of vertical machining centers is that they will generally vibrate more. This vibration can reduce precision and increase wear on tooling and fixtures. Also, this vibration can be an issue for its manufacturers machining delicate or fragile parts or components.
Conclusion
Vertical machining centers offer manufacturers many benefits, including speed, accuracy, and flexibility while performing different operations on small parts or components. Be that as it may, a few limitations are associated with utilizing these machines, for example, their significant cost and limited size, which make them unsuitable for larger projects or components. In this way, manufacturers should cautiously assess their necessities prior to investing in a VMC to ensure that it will meet their requirements while as yet offering some benefit for money as far as efficiency gains over a long time. The high level or significant level models of vertical machining centers include or incorporate a few elements that has modern innovation, which awards it to machine leaves behind the most immune protections.