Electrochemical Machining (ECM): Definition, Parts, Working, Materials, Applications, Principles, Benefits & Limitations
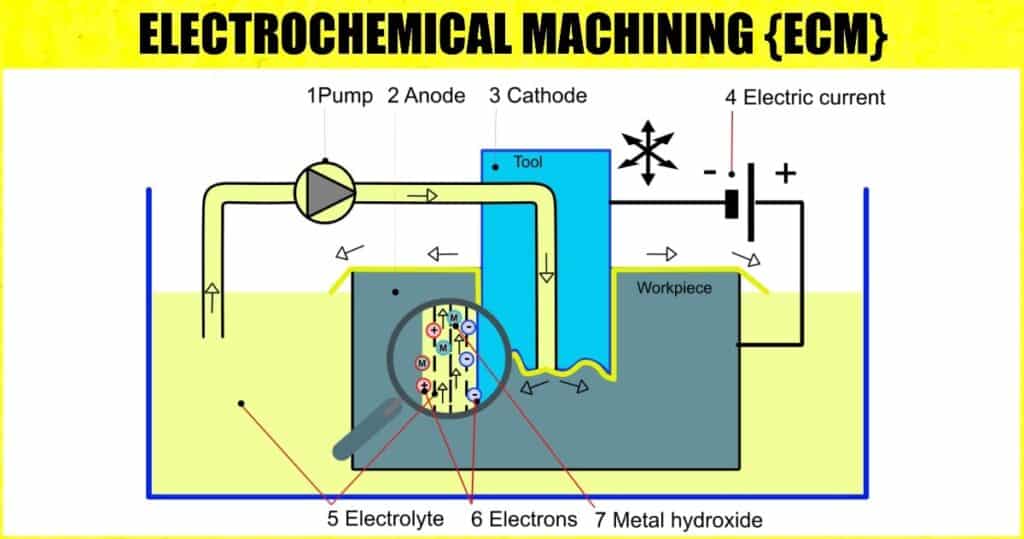
Electrochemical Machining Introduction:
Electrochemical Machining (ECM): Definition, Parts, Working, Materials, Applications, Principles, Benefits & Limitations: – Electrochemical machining utilizes both an electrolyte solution and an electrical flow to alter the workpiece. Since electrical conductivity is important for electrochemical machining, the workpiece material should be conductive.
What is Electrochemical Machining?
Electrochemical machining (ECM) is a process of removing metal with the assistance of the electrolysis process. The electrochemical process is otherwise called the reverse of the electroplating process while in electrochemical machining the metal is eliminated from the workpiece. This process is utilized for the large-scale production of machined parts.
In traditional or conventional machining processes, the tool material must be harder than the workpiece material. Be that as it may, the striking feature of Electrochemical Machining being free of solidarity, hardness, and sturdiness of workpiece material makes it suitable for machining of any conductive material and furthermore machining complex cavities in high-strength materials.
What is the ECM Process?
In the electrochemical process, how the material is taken out from the workpiece is quite unique. The electrochemical reaction happens at the anode (workpiece) and the cathode (device), as well as the encompassing electrolyte fluid. As the electrical current is applied across the anode, ions move between the tool and the workpiece. In electrochemical machining, positive ions or particles move toward the tool, and negative ions or particles move toward the workpiece. This is something contrary to electroplating.
As electrons cross the gap between the workpiece and the tool metal particles go over from the workpiece. These ions combine with hydroxyl ions to form metal hydroxides which are carried by the electrolyte solution. The outcome is a smoothly completed workpiece with the ideal material eliminated to create the necessary shape.
Working of Electrochemical Machining
The working of electrochemical machining begins with the advancement of the tool toward the workpiece. The tool and the workpiece are kept in a suitable electrolyte with a tiny gap between them.
When the potential difference is applied (DC), the workpiece starts acting as an anode and the tool begins acting as a cathode.
At the point when the state of electrolysis is fulfilled, the removal of metal from the workpiece begins. The removal happens as per the shape of the tool. Material is removed from the workpiece and gets settled down as a slug, which is because of the flow of electrolytes.
The electrolyte then, at that point, goes through a filtration process. In the filtration process, the electrolyte is passed through a centrifuge where the slug is eliminated. Then, at that point, it passes through a filter where other remaining impurities are taken out. Assuming that there is an increase in the pressure of the electrolyte, the pressure valve deviates the progression of the electrolyte directly to the tank.
Materials and Designs Used in the ECM Process
A) Materials
- Any electrically conductive materials, yet the most ideal for high strength, hard (> 400 VPN), or challenging to-machine materials.
- Component is stress-free with no distortion, however, has a lower weariness life than that produced by stress-inducing cycles like USM.
- Poor operating circumstances can prompt hydrogen pick-up in steels.
B) Design
- Tolerances are exceptionally reliant upon component geometry, total design, and working circumstances. Typically exactness’s are; for contoured cavities; ± 0.1 mm, and for front-facing cuts or cutting with special tools; ± 0.025 mm.
- Holes down to 3 mm diameter. For more small holes ESM and STEM can be utilized. Deep holes have a taper of 0.001 mm – 1.
- “Overcut” is 0.13-1 mm, however, can be nearly disposed of with a special tool design.
- Internal radii 0.2 mm, outer radii 0.05 mm.
- Surface roughness regularly 0.4-0.8 µm Ra, however “mirror finishes” of 0.1 µm Ra are conceivable with front-facing cuts in specific materials. Side gaps are rougher because of the lower current density.
Principles of Electrochemical Machining:
Electrochemical machining works on the Faraday law of electrolysis which state that assuming that two electrodes are set in a container which is loaded up with a conductive liquid or electrolyte and high ampere DC voltage applied across them, metal can be depleted from the anode (Positive terminal) and plated on the cathode (negative terminal).
This is the fundamental principle of electrochemical machining. In this machining system, the tool is connected or associated with the negative terminal of the battery (functions as a cathode) and workpiece is associated or connected with the positive terminal of the battery (fill in as anode). The two of them are put in an electrolyte solution at a small distance. At the point when the DC current is supplied to the electrode, metal is removed from workpiece. This is an essential thing of electrochemical machining.
What is the Conceptual Electrochemical Model?
NaCl is utilized as an electrolyte, the workpiece is set as the anode, the tool (desired shape) is utilized as the cathode and a potential difference is applied. There is a small gap between the workpiece and the tool for the removal of material.
When a potential difference is applied between the anode and the cathode, the ions start moving from the anode to the cathode.
The negative ions or particles are drawn in towards the workpiece which is placed at the +ve potential and positive ions are drawn in towards the tool which is placed at the – ve potential.
Different Construction Parts of the Electrochemical Machining Setup
An electrochemical plant has different parts, those are as per the following,
1. Power Supply
The power supply is the source of energy that is given to the setup. The power supply is by and large a DC battery comprising a potential difference from 3 to 30V relying on the requirement.
2. Electrolyte
An electrolyte is a salt solution wherein the workpiece and tool are kept during the process of machining. It goes about as a current-carrying medium between the workpiece and the tool. It likewise helps in the removal of waste products from internal gaps and furthermore acts as a coolant by forestalling overheating of the tool and the workpiece.
3. Work Piece
A workpiece is an object that should be machined from which material goes into the solution. The workpiece is made of the anode in ECM. The material evacuation rate or machining is just reliant upon the atomic weight and valency of the work material.
The workpiece can be any electrically conducting material and is insulated from the system with the goal that there is no leakage or short-circuiting of current.
4. Tool
The tool or cathode utilized in ECM is one of the electrodes. It is likewise the ideal shape in which the workpiece is to be cut. The tool utilized in ECM ought to constantly have precise dimensions.
The tool is chosen and manufactured keeping in mind the accompanying properties:
- They are good conductors of electricity.
- They are rigid enough to take up the load and liquid pressure.
- They are chemically inert with respect to the electrolyte.
- They are effectively formable and machinable to the ideal shape.
- They Ought to be manufactured with incredible precision.
5. Tank
The tank contains the electrolyte, tool, and workpiece. Every kind of reactions happens here.
6. Mechanical System
Perhaps one of the main components of ECM is the mechanical system. It is utilized for the progression of a tool that is opposite to the workpiece and is at a constant velocity.
7. Flow Control Valve
A flow control valve is utilized to control the flow of electrolytes which is provided to the tool.
8. Pressure Relief Valve
In the event that the pressure of electrolyte flow surpasses a specific limit, the pressure relief valve opens and it sends the electrolyte back to the tank.
9. Pressure Gauge
A pressure gauge is utilized to measure the pressure of electrolytes which is provided to the tool.
10. Pump
The pump helps in circulating the electrolyte. The pace of pumping and pressure at which electrolytes will be pumped ought to be decided in advance relying upon the application or requirement of the process.
11. Reservoir Tank
The tank that stores unadulterated Electrolytes is known as the reservoir tank.
12. Filter and Centrifuge
A filter is utilized to filter the electrolyte arriving at the reservoir tank. Furthermore, it prevents the accumulation of excess electrolytes. The role of a centrifuge is to separate the slug from the electrolyte.
13. Slug Container
A slug container is utilized to store the slug which is separated from the electrolyte. This slug can be utilized for different experimental purposes.
Applications of Electrochemical Machining:
- Electrochemical Machining is utilized for Die sinking and hole molding activity.
- Grinding by consolidating with the grinding process to eliminate material. The process is additionally referred to as electrochemical grinding.
- Cutting cavities, penetrating further and, surprisingly, irregularly shaped holes in complex designs like jet engine turbine sharp edges.
- Trepanning (by utilizing a device cathode with a cavity) and micro- machining to fabricate micro components since ECM gives a stress-free and great surface completion which has broad application in Nanofabrication and nanotechnology.
- Profiling and machining complex profiles like steam turbine sharp edges within close limits.
Benefits of the ECM Process:
The essential advantage of electrochemical machining is that it delivers precise parts with tight resilience than additional customary techniques. This is on the grounds that ECM works by eroding material in an exceptionally focused manner, permitting it to shape parts to demanding details exactly.
- How much waste produced by electrochemical machining is exceptionally low, as it utilizes no solvents or harmful acids.
- Electrolysis delivers no fumes or vapor that are perilous to people or creatures.
- ECM can be utilized for making complex shapes, delivering small features, and making parts with intricate geometries.
- ECM increases production rates and longer device life.
- ECM process is quick and requires low energy consumption.
- Electrochemical machining isn’t restricted to a particular machine tool and can be utilized on some other machine.
- Machine tool tolerances are precise even after electro-chemically treated material is mounted on it, thus ensuring the exact cutting of parts with no dimensional errors.
- Electrochemical machining produces exceptionally top-notch parts
- ECM provides the ability to work with various sorts of materials including titanium, aluminum, copper, silver, gold, and platinum since they have excellent electrical conductivity.
- It produces clean parts with no welding to make them fit together.
- This process doesn’t need high temperatures for material to bond appropriately, which limits the risk of melting or burning during operation.
- It produces chips with good electrical conductivity and low resistance, which makes them ideal for sensors.
- It can make exact cuts in thin metal sheets.
Limitations of the ECM Process:
While electrochemical machining offers a few advantages over additional conventional techniques, there are a few weaknesses too.
- The time has come consuming since the process should be done on various occasions to accomplish desired results.
- when compared with different methods, EMC offers poor surface finish and uniformity due to its inclination of utilizing solvents rather than metals.
- Electrochemical machining is a high-cost installation.
- The process additionally requires a lot of power which makes it more costly than different processes that use molten metal.
- On the off chance that you are cutting hard metals like steel or stainless steel, you will observe that electrochemical machining isn’t truly adept at producing sharp edges since it utilizes a chemical reaction to remove material from the surface.
- Electrochemical machining requires exceptional ranges of abilities from your operators since they must be trained on the most proficient method to work the machines securely and effectively.
- It has lower costs due to reduced consumables (no lubricants or coolants required, less expense of power), energy use reduction, lower maintenance requirements, and so on.
Conclusion
Electrochemical machining offers two or three clear benefits over more conventional assembling methods, for example, extended accuracy and further improved life expectancy for equipment utilized in production cycles yet those benefits incorporate a couple of pitfalls. Assuming that you need precise components produced rapidly and sensibly, ECM probably will not be your by and large ideal choice; anyway, accepting for a moment that you’re searching for high-quality parts with tight tolerances that will continue on through extended use cycles, then, electrochemical machining could legitimize thinking regardless of what are its drawbacks.
Eventually, whether this method is perfect for you will rely on your particular necessities and monetary plan objectives so try to actually take a look at the benefits in general and limitations preceding picking what’s best for your business.
Image Source: – wikipedia