4 Types of Stirling Engine: Application & Working Principle [Complete Details]
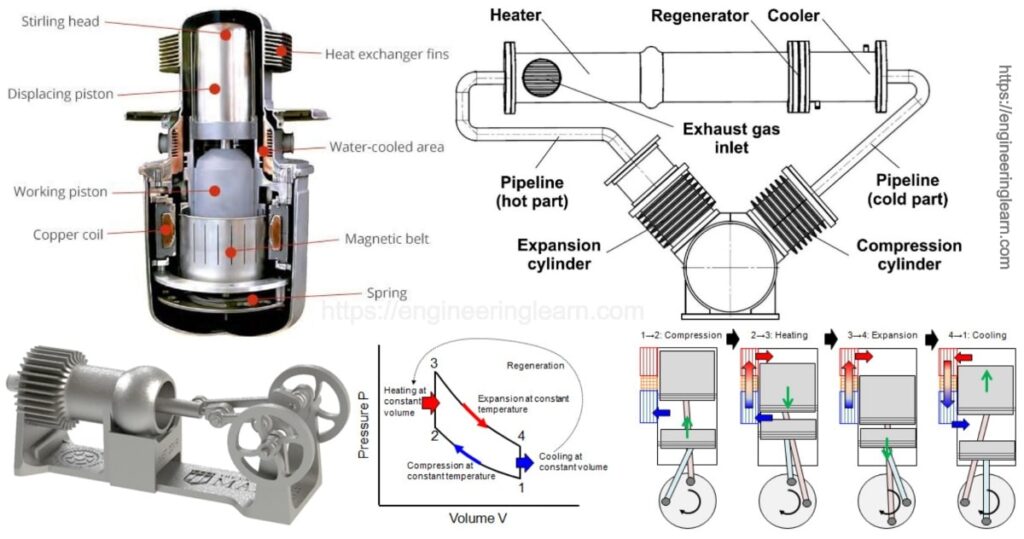
Introduction of Stirling Engines
Types of Stirling Engine: Application & Working Principle :- Invention of a Stirling engine was done in the year 1816 by Rev. Robert Stirling who wanted to create a safer alternative to steam engines, as steam engines were found to be dangerous due to the often explosion of its boiler with the effect of high steam pressure and also the limitations of some primitive materials which were available at that time.
The working of the Stirling engine is same as the other heat engines which are used to convert the heat energy into the mechanical energy. Whereas the essential features of a Stirling engine are that it is a closed cycle and an external combustion engine which means that the engine uses a fixed amount of working fluid, usually air and some other gases, which are enclosed in a sealed container and the heat which is consumed by the engine is provided externally. This feature allows the engine to work on any heat source which can include fossil fuels, hot air, solar, chemicals, nuclear energy etc.
It is also good to know that these engines can also work with very low temperature differentials as well which can be as low as 7°C, between the heat source and the heat sink so that it can be powered by the heat of the body and the steam.
Stirling Engine Working Principle
The main working principle of the Stirling Engine relies on the property of gases which says that it expands when heated and contracts when cooled, or it can be explained as the gas which is contained in any fixed volume will increase the pressure on heating and decrease on cooling.
In case the gas is filled in any volume container which is variable or is made from a piston in a cylinder which is movable and closed at one end so it will be noticed that the pressure will increase and decrease and will cause the piston to move in and out. The heating and cooling process will develop a reciprocating movement of the piston which shall be converted into a rotary motion by the use of a conventional connecting rod and a crankshaft accompanied with a flywheel.
The rate at which the temperature of the gas varies due to heating and cooling, so the cylinder is kept limited to a large thermal capacity of working pistons and cylinders. However, this constraint can overcome by the movement of gas from one end of the cylinder to the other by maintaining a constant high temperature at one end and constant cold temperature at the other end of the cylinder. The condition is attained by the help of a loose fitting piston which is known as displacer. The displacer moves consistently inside the cylinder, which shuttles the gas from one end to the other end. As the displacer is kept moving, the gas starts leaking around the gap which is present in between the displacer and the cylinder wall. The displacer does not produce power itself whereas only uses enough energy to circulate the amount of gas within the cylinder.
Application of Stirling Engines
Stirling engines are found having various applications are used in a variety of forms from 1930s with a motive of power in the range of vehicles and engines of 75kW and more have been developed. Even if the early engine developments were for automotive use due to its low specific power, the Stirling engine still better suited for stationary applications. So, here are some of the most commonly known applications of Stirling engines:
- Combined Heat and Power: The Stirling engine is an ideal engine for its use in small combined heat and installations of power to capture the wastage of heat. These engine generators are used to develop the electrical power output between 1 kW and 10 kW and are most commonly available for domestic applications with an utmost aim to use the waste heat by the central heating boiler. The overall thermal efficiency of this system can be the highest till 80%.
- Solar Power: The depositors of Stirling engine generators are used to generate the electricity from the thermal energy which is captured by very large solar thermal arrays.
Types of Stirling Engine
- The Stirling Engine (Alpha Configuration)
- The Stirling Engines (Beta Configuration)
- The Stirling Engines (Gamma Configuration)
- Double – Acting Stirling Engine (Swash Plate)
1. Alpha Configuration Types Stirling Engine
There are two cylinders which is enclosed with a fixed amount of air and other fluids, one being hot and the other being cold. It is shuttled forward and backward between both these cylinders. This is done as the hot air expands which is present in the hot cylinder and the contracts when interacts with the cooled air which is present in the cold cylinder. This is the source of energy which is used to perform mechanical work in the process.
2. Beta Configuration Types Stirling Engine
You would be amazed to know the thermodynamics of the Stirling beta engine are very similar to the alpha engine but the fact is that their physical configuration are quite different from each other.
This engine consists of only one cylinder which is highly heated from one end and kept cooled at the other. For this a single power piston is arranged coaxially accompanied a displacer which move within the cylinder. The displacer piston does not take any sort of power from the gases which are expanding but only serves to transfer the working gas back and forth within the two ends.
3. Gamma Configuration Types Stirling Engine
This engine with the gamma configuration is same as that of a Stirling beta engine which does not has the power piston mounted coaxially with respect to the displacer piston.
4. Double – Acting Types Stirling Engines (Swash Plate)
The gas which works consistently is moved back and forth with the help of regenerators in between the adjacent cylinders that are heated from the top and are cooled at the bottom. The arrangement is found having no displacers as the pistons in the nearby cylinder performs this function well. It is important to keep the cylinders closed from both the ends and also the connecting rods should pass through the seals into the adjoining cylinder caps as the lower side in order to protect the gas from escaping the cylinder.