Water Jet Machining: Definition, Parts, Working Principle, Application, Advantages & Disadvantages
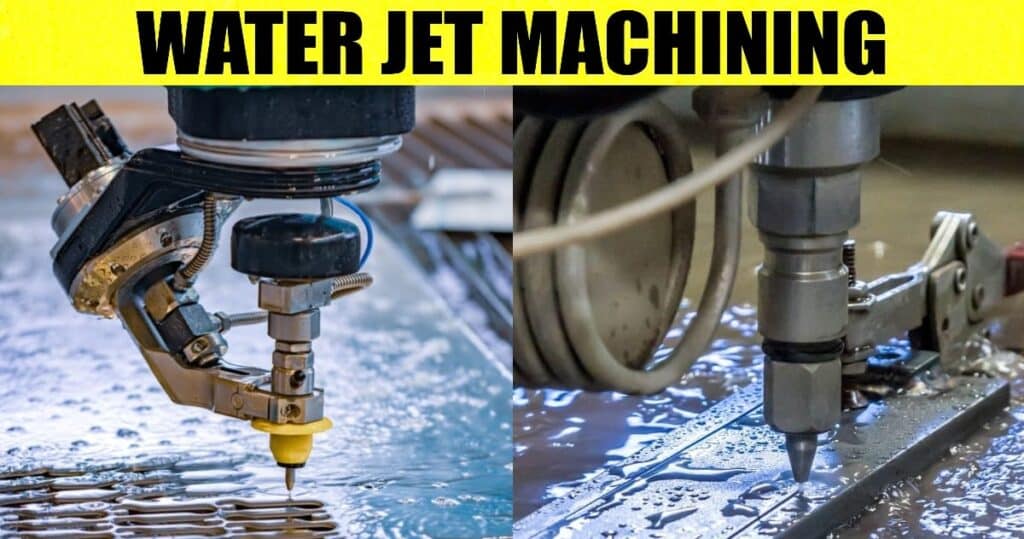
Water Jet Machining Introduction:
Water Jet Machining: Definition, Parts, Working Principle, Application, Advantages & Disadvantages: – Utilizing Water jet Machining, A jet of water to cut a sheet of metal might sound unimaginable, however, it is based on the guideline we learn from the get-go in our lives. A simple illustration of a Water jet is the point at which a finger is put over part of the tap, the stream of water flows with higher pressure so it washes away mud undeniably, giving a jet-cleaned item. Throughout recent years, because of the potential for reducing dust and related hazards while cutting coal or rock utilizing water jet machining.
What is Water Jet Machining?
One of the advanced and innovative machining processes which is used to machine different sorts of work pieces which ranges from plastics to metals is known as water jet machining. For machining softer materials, for example, plastics and fibers, simple water jet machining is utilized. However, with regards to harder materials, for example, metals, water alone can’t provide palatable outcomes. Thus Abrasive particles are blended in with the water jet to play out the cutting action. The pressure varies as per the work piece from which the material is to be removed. This process is like the water erosion peculiarity that exists in nature.
It is essentially used to remove materials from soft and non-metallic work pieces like plastics, elastic, glass, and so on. A high-velocity water jet is utilized in this process to eliminate materials from the work piece. The basic standards of this process are that the kinetic energy of the water jet must be converted into pressure energy so it eliminates the material from the work piece.
Exactly when the Jet of water collides with a work piece with kinetic energy, this kinetic energy will be converted or changed over into pressure energy. This pressurized energy will incite stress to the work piece, and because of this, the tension material will start to move away from the work piece.
Working Principle of Water Jet Machining
Water jet machining works on the standard of deterioration of the area on which the high-speed water jet strikes. All the while, first, the pressure of water is increased to a few thousand bars and afterward, the pressure energy is converted into kinetic energy of the water jet. This kinetic energy as a high-velocity water stream is sufficient to eliminate material from the surface of the work piece or penetrate the work piece resulting in a cutting action.
Let us Understand How it Works Step-by-Step
- Water from the repository first enters the hydraulic pump.
- There is increase in the pressure of water at around five bars by hydraulic pump and finally sends it to the intensifier.
- Accumulator provides a high-pressure water supply to the blending chamber at whatever point required.
- In the wake of passing through the intensifier water needs to go through the pressure control valve where pressure is controlled.
- Subsequent to passing through the control valve it reaches the flow control valve, where the flow of water is checked
- Along these lines, high-pressure water reaches the blending chamber where it is blended in with an abrasive stream of water and abrasives strike the work piece.
- Material evacuation happens because of the disintegration of material from the outer layer of the work piece.
- The waste water is taken out through the channel and is supplied to the reservoir with the assistance of a pump.
- The water supply is halted and the completed product is removed.
What is the Process for the Construction of Water Jet Machining?
In Water jet machining, the water repository is connected to the hydraulic pump which is utilized to increment pressure. The hydraulic pump is then connected or associated with the intensifier. The essential supply from the intensifier is connected to the accumulator and the subsequent supply is connected to the blending chamber through a pressure control valve and flow control valve. The mixing chamber is connected to two supply lines, one for high-pressure water and the drain system channel which in turn is connected to the supply repository through the pump.
Parts of Water Jet Machining
1. Water Reservoir
A water reservoir is utilized to store water which is to be utilized for the machining process. The repository is for the most part situated fairly over the entire setup. This ensures a constant and continuous flow of water.
2. Hydraulic Intensifier
A hydraulic intensifier is the primary part of a water jet machining setup. For increasing the pressure of water, hydraulic intensifier plays an very essential role. Hydraulic or Pressure driven intensifiers are a bunch of three concentric cylinders that use the weight or heaviness of inlet water to build the pressure of outlet water.
3. Hydraulic Pump
A hydraulic pump is utilized to transfer water from the repository and supply it further at a pressure of around 5 bars. The hydraulic pump is furnished with a pressure gauge to measure the pressure of water being passed.
4. Abrasive Storage Tank
Abrasive particles are vital while working with hard materials. The regularly utilized Abrasive particles are aluminum oxides, sand, garnet, glass particles, and so on. The abrasive storage tank is utilized to store the abrasive particles.
5. Accumulator
A tank that stores high-pressure water utilized for machining is known as an Accumulator. It supplies water at whatever point there is a pressure drop and all the more high-pressure water is required. The accumulator is a significant component as it aids in the smooth running of the water jet machining process.
6. Valves
There are two valves utilized during the process of water jet machining. They are as per the following:-
(i) Pressure Control Valve
A pressure control valve is utilized to control the pressure as well as the direction of the water.
(ii) Flow Regulator Valve or Flow Control Valve
Managing the progression of water is utilized. On the off chance that more water is provided, the valve will be closed.
7. Nozzle
One of the important parts of water jet matching is that converts the pressure energy of water into kinetic energy and is known as a nozzle. A nozzle has a diminishing area of cross-section and consequently can increase the kinetic energy of water. The nozzle is made of ruby or jewel so that no cutting action ought to occur at the nozzle end.
8. Mixing Chamber
The blending chamber is the volume where high-pressure water is blended in with the abrasive particles.
9. Drain System
The drain system accumulates the water subsequent to machining and sends it back to the repository tank. The drain system is connected or associated with a pump which assists in the transfer of water to the supply tank.
10. Flow Regulator
The progression of water arriving from the control valve is regulated utilizing a flow regulator. In the wake of managing the flow regulator, the water will go through the nozzle, i.e., the high pressure of the water will be converted into high-velocity water.
11. Catcher or Drain
Catchers or drains are utilized to gather water subsequent to cutting the work piece. From here, water is sent for additional filtration or can be reflowed.
Application of Water Jet Machining
The applications of Water jet Machining are as per the following mentioned below:-
- In aviation industries for machining, Cabin panels, engine parts, trimming turbine blades, and so on are generally utilized for water jet machining. This process is utilized in light of the requirement of high accuracy during machining.
- Average water jet machining is also used in textile or material industries for cutting soft or delicate as well as thin materials with high precision and accuracy and also without the generation of heat intensity.
- Exceptionally large setups of Abrasive water jet machining are utilized for cutting rocks through the principle of erosion by a pressurized stream of water and abrasive particles.
- Not many machining processes are equipped for cutting fragile materials like glass. One of these machining incorporates water jet machining which is moreover used for machining different glass products like mirrors.
- Mostly in automobile industries water jet machining is utilized for machining different automotive parts. This is because of the minimum wastage of material during the machining process.
Advantages of Water Jet Machining
A) Accuracy
Accuracy is one of the essential parameters in water jet machining. The accuracy or precision of finished products which is acquired by water jet machining is extremely high. A tolerance of around 0.12mm can be obtained utilizing water jet machining.
B) Clean Process
Water jet machining is an ideal cycle as it is without dust (Dust –free) and waste materials are cleaned or wiped out through the channel. This gives a superior surface completion of the work piece.
C) Complex Structures
The surge of water produced in water jet machining can be in the order of a*0.01mm. This gives a benefit while manufacturing complex structures and detailed items.
D) No Heat Generation
Heat generation in a water jet machining process is quite negligible. Because of heat generation, there are no thermal breaks produced in the work piece. This outcome in a superior quality product.
E) Adaptability
A water jet machining setup can be utilized for hard materials like metals as well as materials that are delicate or sensitive like plastics and fibers. Machining soft materials are unrealistic using traditional machining techniques as the heat produced would burn soft materials.
F) Eco-friendly
Water jet machining is an eco-friendly process as there are no pollutants or contaminations produced simultaneously. Waste management is likewise simple on account of water jet machining.
G) Low Cost of Running
Due to the absence of moving parts, the expense of running a water jet machining is minimal. There are no electrodes or cutting devices utilized and water utilized in the process can be reused. This variable additionally helps in lessening the cost of running.
Disadvantages of Water Jet Machining
A) High Initial Cost
If we talk about the initial cost and expense of water jet machining setup it is basically high. This is because of different pressure-increasing parts. The nozzle utilized is made of ruby or jewel which is additionally expensive.
B) Material Thickness
One of the significant hindrances of water jet machining is that it can’t cut exceptionally thick materials.
C) Low Efficiency
If we compare traditional machining work with water jet machining, water jet machining takes is more time to complete a task as compared to traditional one. This outcome in low output or lower efficiency of the machining plant.
D) Corrosion
Clearly when we machine a work piece utilizing water jet machining, the metal surface might get corroded because of moisture. This is one of the disadvantages of water jet machining as corrosion might bring about diminished strength of the work piece.
Conclusion
Water jet machining is a broadly used manufacturing process in Automotive, Aviation, Food processing, Safeguard and military, Clinical, surgical equipment, and mining since it can cut material or shape that is challenging to cut utilizing traditional manufacturing techniques. The food processing industry likewise utilizes it to cut and slice food products since it is a more effective and clean operation than other cutting processes. A significant benefit of water jet machining is that no heat or intensity affected zone happens because of its cold cutting technique. Not in the least does cold cutting empower clean cuts, yet additionally increments the operators safety and wellbeing altogether by eliminating the risk and dangers of burns.
Image Source: – southernrubber, thefabricator