Servomotor Working Principle
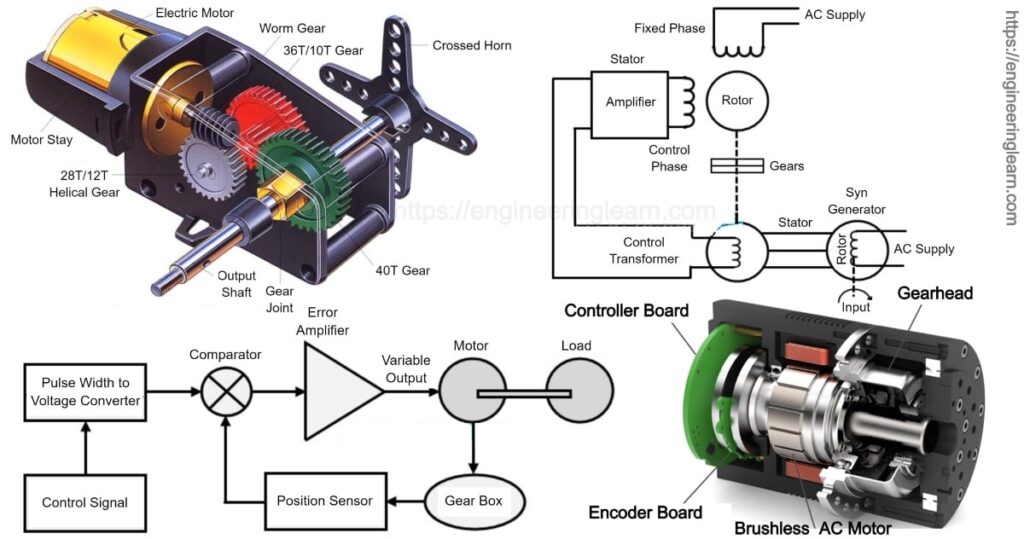
Servomotor Working Principle:- A servomotor is a linear and rotary actuator. An actuator is a device which is responsible for movement of a component of a system. In closed loop systems, the final control elements are actuators. A servomotor controls the linear and angular motion of the shaft; more precisely it is a device which is used for precise control of linear or angular position, velocity and acceleration.
In order to control the linear or angular position, velocity and acceleration, the servomotor uses a closed loop control mechanism. If a DC motor is used to control the system then it is called DC controlled servomotor and if an AC motor is used to control the system then it is called AC controlled servomotor.
The closed loop control system contains a measurement device which measures the position and then converts it into an electrical signal. Such measurement devices are called encoders. The system also contains an amplifier whose purpose is to amplify the signal so as to work with it more precisely and properly.
The simplest of servomotors measure only position. Thus they are only equipped with position encoders. They have a set point for the position which is called as command position. They measure the actual position with command position and if there is difference in the values then that means the error is not zero in the closed loop control system. The error has to be brought to zero by the controller by changing the actual position.
The simplest of servomotors use potentiometers as encoders. These cannot be used in complex applications. They are not common in industrial applications. Although for some industrial applications, the position signal can be electrically differentiated in order to bring speed control into the system. These encoders coupled with PID controller warrant precise control for some industrial operations.
In most complicated industrial applications, rotary encoders are used along with variable speed drive to control the speed by varying input frequency. This coupled with PID control mechanism provides an excellent control with less overshooting.
Servomotors are found in many industrial applications, they are used in almost all mass transfer applications which require variable speed or variable power input to the system depending on the concentration of components in the feed stream. They are used in chemical reactors and also widely used in semisolid industries. They are found in many household electronics, like in inkjet printers, CD and DVD drives, in remote controlled devices and many more applications.
A servomotor is much more versatile than standard electrical motors. The standard electrical motors start running when power is applied to them. The speed can be controlled but they keep running as long as the power is being supplied. The servomotors run according to the signal commanded to it. They run for the period instructed and then wait for the next signal. They can also turn to whatever angle commanded by the controller.
The various parts of the servomotor control system are usually integrated in order to reduce the footprint and make the system more compact to handle. Usually the encoder and amplifier are joined together. Also, the motor, encoder, drive and the auxillary electronics can all be fit into a single package. In order to reduce cost for large volume applications, the controllers are designed around microcontrollers.