Plastic Fabrication: Definition, Types, Methods, Applications, Advantages & Disadvantages
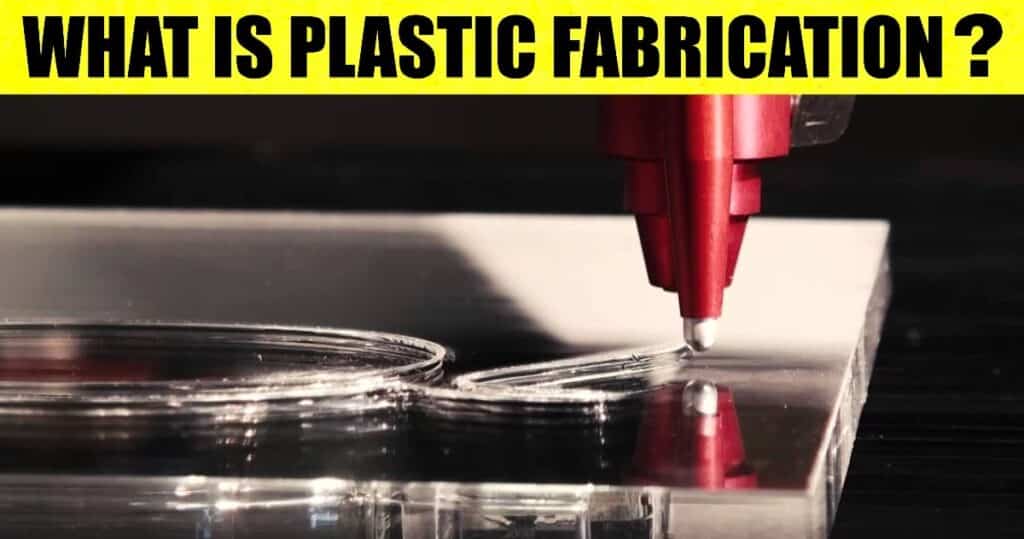
Plastic Fabrication Introduction:
Plastic Fabrication: Definition, Types, Methods, Applications, Advantages & Disadvantages: – Plastics may be the most universal material on earth utilized for all that from baby bottles to aviation parts, and everything in between. Lightweight, adaptable, and capable of being shaped and molded in manners different materials could not, plastics enabled inventors and brands to accomplish new levels of advancement.
What is Plastic Fabrication?
Plastic fabrication alludes to the most widely recognized approach of making objects together with plastic like synthetic designs and other synthetic or semi-synthetic polymers. The process of plastic fabrication incorporates various steps beginning with planning and design and closing with the manufacture, assembly, and finishing of the planned object. In today’s time, we view plastics with regard to their lasting impact on the climate. Early plastics were a valued substitute for materials made using regular resins reaped from plants and bugs which were at times difficult to get.
Types of Plastic Fabrication Methods
Plastic fabrication includes various strategies. Injection molding, plastic extrusion, and FDM 3D printing are some of the plastic fabrication methods and there are a lot more we will discuss below.
1. Injection Molding
Injection molding is the most widely recognized plastic fabrication process. It can process thermoplastic and thermoset polymers. This fast plastic fabrication strategy work by heating plastic pellets until they melt or soften, and from that point forward, forcing the molten plastic into a metal mold using a reciprocating screw. The molten material cools down, solidifies, and accepts the state of the mold cavity. The strong part is then ejected from the mold. Injection molding is reasonable for a huge variety of materials and parts.
2. Blow Molding
Blow molding is a plastic molding process that is less utilized than injection molding. This plastic fabrication process work utilizing a mold and a molten thermoplastic tube which is called a parison. Pressurized air enters the parison, making the plastic expand and touch the internal walls of the mold, in the end expecting the shape of the mold activity.
3. Vacuum Casting
Vacuum casting is a plastic fabrication process normally utilized for small batches or clumps of brilliant prototypes. It utilizes silicone molds to make urethane plastic parts. During this plastic fabrication process, the operator pours urethane casting resin into a silicone mold; a vacuum then, at that point, eliminates air pockets and bubbles, bringing about an exceptionally smooth finished part. The urethane parts are then restored in an oven.
4. Rotational Molding
Rotational molding is another plastic molding process that utilizes high temperatures and low pressure to form plastic parts. It works by pivoting or rotating a mold to move the plastic material around inside. During the rotational molding process, powdered plastic is put in a shape, which is heated and rotated about (no less than two) axes. This rotation or turn guarantees that molten plastic covers the total of within the mold and recognizes the shape of the cavity.
5. Fused Deposition Modeling
Fused deposition modeling (FDM) is the most widely recognized 3D printing process for plastic fabrication. FDM works by heating extruded thermoplastic fiber, then, at that point, depositing it in precise shapes from a moving nozzle as per instructions of a computer. In small quantities, FDM is extremely fast and cost-effective and can produce many shapes, incorporating those with complex internal geometries.
6. Plastic Machining
Plastic machining is an exceptionally popular plastic fabrication process. Although various machines work in various ways, plastic machining for the most part involves entails cutting away sections from a plastic work piece utilizing either manual or computer-controlled cutting tools. Machining is particularly precise, works with different plastics, and is better than molding for making thick-walled parts.
7. Plastic Pultrusion
Plastic pultrusion is a variation of plastic extrusion where the material is pulled through a die as opposed to push. The plastic fabrication method of pultrusion is suited to fiber-reinforced plastics. During the process of plastic pultrusion, a roll of supported fibers are pulled through a tank of plastic resin, which impregnates the fibers, and a while later through a heated die, giving the fiber-reinforced resin its custom profile.
8. Plastic Extrusion
Plastic expulsion is the most common way of forcing plastic through a die to make an extended plastic part with a consistent profile. This high-volume plastic fabrication process works by heating plastic in a barrel, then forcing it to sing a reciprocating screw into a die, giving it its final shape with a consistent profile. The subsequent plastic extrusion solidifies as it cools down.
9. Plastic Welding
Welding is by and large connected with metals, yet plastic welding is a significant plastic fabrication process for joining thermoplastic parts which are not reasonable for gluing or other assembly systems. The plastic welding process has countless variations, including hot gas welding, speed tip welding, and contact welding. Most of the variations include preparing the outer layer of the plastic, applying heat and pressure, and after that cooling.
10. Selective Laser Sintering
Selective laser sintering (SLS) is a plastic fabrication process and one more form of 3D printing. SLS is a powder bed fusion process. It works by using a laser to sinter 2D shapes in plastic powder, layer by layer, fabricating an all-out plastic part explicitly.
11. Stereolithography
Stereolithography (SLA) is an alternate form of plastic 3D printing that works with photo polymeric resins rather than thermoplastic polymers. It works by specifically curing photo polymeric resins utilizing a light source like a laser. Parts are printed layer by layer as the print bed travels through the resin vat. SLA produces brittle however exceptionally smooth parts, which can likewise be transparent.
12. Thermoforming
Thermoforming is a kind of plastic fabrication that appears as molding yet utilizes tenderly heated plastic sheets rather than totally molten plastic. The plastic fabrication strategy method requires an oven and a mold. During the Thermoforming process, the plastic sheet is heated until pliable, it is then stretched over a mold typically utilizing a vacuum prior to being trimmed and cooled.
Choosing the Right Plastic Fabrication
Before you select a plastic manufacturing process for your product, taking into account the following factors is ideal:
A) Form
Different plastic parts have various features and resilience requirements. It will be ideal in the event that you consider these factors prior to choosing a plastic fabrication process. The manufacturing processes might rely upon the design’s geometry. It might likewise require the optimization of design for manufacturing. This ensures a more economical production.
B) Material
Choosing or Picking a material for your applications needs you to think about certain factors. Consequently, need to think about aesthetic and functional necessities and balance them with the cost. Examine the best features of your applications.
C) Lead Time
Another important factor you really want to consider is the manner how soon you need the finished products. Some fabric fabrication processes create the initial parts in a day. Other high-volume processes incorporate tooling and setup that might take a couple of months.
D) Cost / Volume
It is important to understand the total volume of parts you need to manufacture. A few processes have extra expenses for setup and tooling. Be that as it may, they produce economical parts on a per-part basis. Then again, some low-volume processes have lower setup costs with constant expense per part.
Applications of Plastic Fabrication
Plastic fabrication essentially has an impact on different industries. Industry-wise, the uses of plastic fabrication are as per the following.
1. Construction Industry
Plastic comes in numerous alternative forms and specific materials. Options like polyurethane and polycarbonate might be available in handy for things like windows and doors. Vinyl is useful in exterior applications and any place where additional durability is required. Polyvinyl Chloride and similar plastics can work well for the fabrication of pipe systems and other interior applications. Plastic fabrication is a service that enables or empowers customers to design and shape things that meet their specifications.
2. Aerospace Industry
Plastics kept on succeeding within the Aerospace industry, design, manufacturing, most importantly, the variability of utilization. In past, Materials like vinyl were used to line fuel tanks and different sorts of plastics were utilized in radar covers thanks to their transparency to electromagnetic waves. Besides the fact that this significantly improves radar technical capacity, however more stronger and flexible plastics were additionally involved on helicopters as they supply increased security and can withstand the helicopter vibrations.
3. Automotive Industry
Plastic has been assuming a huge part in the design and manufacturing of automotive vehicles. It has been furnishing the industry with stringent guidelines and changing the propensities for shoppers towards driving less expensive, eco-friendly, and lightweight vehicles. Fuel efficiency has become one of the chief significant features in self-propelled vehicle design on account of the rising fuel costs and stricter environmental guidelines. This, combined with the popularity of automotive vehicles rising income in emerging economies will, in any case, drive demand for plastics within the automotive industry.
Advantages of Plastic Fabrication
Plastic is an excellent decision due to the many benefits that come along with utilizing it.
1. Plastic Can be Utilized to Form Different Shapes
Plastic has an exceptionally low melting point notwithstanding high flexibility, which makes it an optimal material for fabricating parts into a wide range of shapes and sizes. Whether you really want to fabricate plastic into an exceptionally basic shape or a more complex shape, you will find that it will not be difficult to work with.
2. Plastics take Limited Time to Fabricate than Different Materials
Since plastic is so easy to work with, you can usually fabricate the parts you want much faster than if you were working with an alternate material. Plastic fabrication normally brings about faster cycle times and turnover rates, so you will not need to invest a great deal of time in making it happen.
3. Plastic doesn’t Need to be Completed After the Completion of Fabrication
Most metals should be finished off whenever they have been fabricated. The opposite is valid for plastic. With plastic, you can change the shade of it during the fabrication process, which wipes out the need to paint or finish it off later. Whenever it has been fabricated, the production is normally finished and doesn’t require another step later.
4. In Comparison to some other Metals Plastic Weighs a Lot Less
At the point when you do metal fabrication, you will as a rule be left with a lot of parts that are on the heavier side, contingent on which metal you utilized. Plastic is basically light, nonetheless, so you will be left with lighter parts that are simpler to move around.
Disadvantages of Plastic Fabrication
Plastic fabrication also has some disadvantages. Below are some of its limitations: –
1. Limited Temperature Resistance
Plastic has an exceptionally low resistivity towards higher temperatures. They can be melted or deformed effectively at elevated temperatures.
2. Structural Weakness
Although, Plastics are used for parts that need good strength and durability, they fail to provide structural strength of higher quality. They can’t be utilized for heavy equipment parts or in building structures.
3. Limited Wear Resistance
Plastics additionally don’t have good resistance towards corrosive elements or acridity. Plastics can undoubtedly lose structural integrity when they come in contact with materials which are corrosive.
4. Non-degradable
Most plastics are non-degradable and they might set aside some margin to break down once they’re landfilled. With an ever-increasing number of plastic products, especially plastic packaging, being disposed of not long after their purchase, the landfill space required by plastic waste may be a growing concern.
Conclusion
Choosing the best plastic fabrication process requires a decent knowledge of the most proficient method to fabricate plastic. As we discussed above. This article presents the main plastic manufacturing processes. The data above assist with understanding what they involve. We additionally covered the various elements you should consider to pick the best cycle for your application.
Content Source: – bridgewaterstudio, bridgville, 3erp
Image Source: – ateamplastics